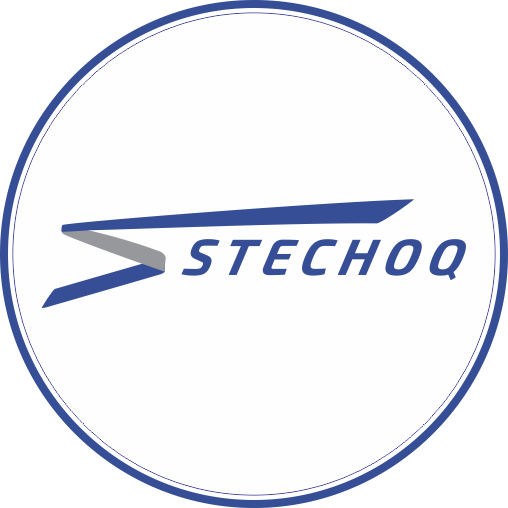
Abnormalitas adalah suatu kondisi proses kerja yang tidak sesuai dengan standar yang sudah ditetapkan. Didalam konsep ini Built-In Quality (BIQ) adalah kualitas yang dibangun atau dibuat didalam proses, bukan melalui perbaikan atau diproses selanjutnya. BIQ adalah membangun kualitas produk dari dalam proses-nya itu sendiri, atau dengan kata lain BIQ adalah konsep mencegah terjadinya cacat produk yang dilakukan oleh operator langsung didalam dan disaat proses. Di dalam konsep ini, operator bertindak pula sebagai Inspektor kualitas dalam satu rangkaian proses produksi.
Kesehatan dan Keselamatan Kerja memiliki istilah K3 yang merupakan bidang terkait dengan kesehatan, keselamatan, dan kesejahteraan manusia yang bekerja di sebuah institusi maupun lokasi proyek. Konsep terkait K3 ini dapat didukung dengan adanya Sistem Manajemen Keselamatan dan Kesehatan Kerja (SMK3) karena pembentukan dan penerapannya menjadi langkah awal dalam manajemen terstruktur sistem kesehatan dan keselamatan di lingkungan kerja. Tujuan utama penerapan SMK3 adalah menciptakan manajemen K3 di tempat kerja dengan mengintegrasikan pihak manajemen, pekerja, kondisi, dan lingkungan kerja untuk mencegah dan mengurangi kecelakaan dan penyakit akibat kerja, serta menciptakan tempat kerja yang aman, efisien dan produktif.
Di BDI Factory, sistem respon terhadap abnormalitas dibuat lalu dijelaskan pada stakeholder terkait untuk memahami alur penyelesaian abnormalitas, namun untuk memvisualisasikan sistem tersebut, belum tersedianya suatu visualisasi baik dengan poster atau dalam bentuk digitalisasi.
Di area mesin injeksi, operator akan langsung mengkomunikasikan masalah kepada supervisor dan supervisor akan melakukan koordinasi dengan bagian yang berkaitan dengan masalah yang muncul. Sementara itu, di proses logistik respon terhadap abnormalitas belum bisa diidentifikasi dengan jelas apakah sudah ada atau belum. Berikut merupakan kondisi layout BDI Factory saat ini:
Pendataan abnormalitas yang muncul di lantai produksi berfungsi untuk melakukan evaluasi efektivitas dan efisiensi proses produksi yang ada sehingga mempermudah dalam menganalisis dan melakukan perbaikan pada proses di lantai produksi. Teknik pengumpulan data yang digunakan untuk pendataan abnormalitas adalah prinsip 5 Gen yaitu Genri, Gensoku, Genba, Genbutsu, dan Genjitsu.
Pengumpulan data dilakukan mengikuti prinsip teori umum dan pendekatan ilmiah, kemudian memecahkan masalah serta melakukan peningkatan proses, kemudian meninjau secara langsung dimana suatu permasalahan terjadi, melihat suatu kejadian atau benda dengan matanya sendiri, serta merasakan adanya abnormalitas pada proses produksi maupun proses kerja di dalam suatu industri. Pengumpulan data ini bertujuan untuk mengetahui langkah lanjutan untuk mengetahui respons ketika terjadi abnormalitas. Dalam pengumpulan data abnormalitas atau permasalahan apa saja yang timbul di proses produksi, belum dilakukan suatu prosedur pendataan di BDI Factory.
Proses manufaktur yang berkembang dari zaman ke zaman dan perkembangannya dipengaruhi oleh sikap terhadap manajemen sumber daya. Tujuan dari proses manufaktur adalah bagaimana keuntungan maksimum atau maksimal dengan investasi modal yang minimum secara umum telah menjadi tujuan dari proses manufaktur atau proses produksi. Oleh karena itu, produsen masa depan harus fokus pada kebutuhan konsumen dan cenderung penciptaan nilai yang efisien dalam proses produksi. Akibatnya, industri dipaksa untuk memiliki siklus inovasi yang lebih pendek dan proses produksi yang kompleks. Pentingnya atau tujuan trend baru ini menjadi sesuatu yang penting dengan munculnya popularitas pada sistem atau proses manufaktur. Trend baru di bidang manufaktur yang mengikat ke dalam transformasi paradigma produksi saat ini dapat diamati pada gambar di bawah. Manufaktur sosial akan menjadi kekuatan pendorong untuk kustomisasi dan personalisasi produk sesuai dengan paradigma dan dalam pelaksanaannya menjadi layanan cerdas bagi customer. Untuk dapat beradaptasi dengan paradigma baru ini, sistem manajemen visual baru perlu dimasukkan ke dalam produksi proses. Ini dapat membantu meningkatkan kontrol dan kinerja dalam kompleksitas produksi baru. Sistem semacamnya dapat mencakup, antara lain, kemampuan mengontrol dan memonitoring secara virtual dan real time dari stock warehouse maupun monitoring dan capture proses produksi secara real time, dimana sistem tersebut dapat menghasilkan penjadwalan produksi secara efisien dan dapat mencapture atau mencatat proses produksi yang lebih efisien. Sistem manajemen visual dapat diimplementasikan dalam lingkungan sistem produksi cerdas (smart production activity) yang berfokus pada peningkatan efisiensi produksi dan pengurangan biaya. Intinya, sistem ini dapat mengumpulkan informasi dari berbagai sumber dan menggunakan kecerdasan teknik pemrosesan, berdasarkan operasi historis dan proyek masa depan, untuk menghasilkan manajemen sumber daya yang cerdas dalam penjadwalan dan proses produksi. Untuk mencapai sistem ini, diperlukan alat manajemen visual yang unik dan inovasi untuk proses manufaktur.
Sistem visual manajemen menggabungkan keseluruhan proses manufaktur melihat proses transparansi di seluruh perusahaan. Sistem ini akan berfungsi pada dua tujuan. Pertama, itu akan berfungsi sebagai titik akses ke kolaborasi dan smart system, dimana klien, manajer, atau pabrik lain dapat berbagi sumber daya dan kedua, dapat digunakan untuk meningkatkan teknik manajemen sumber daya melalui penggunaan alat manajemen visual digital. Oleh karena itu, studi tentang metodologi implementasi sistem manajemen visual akan dieksplorasi dalam perusahaan produksi.
Sistem manajemen visual ini dapat secara signifikan membantu pertumbuhan sistem dan proses manufaktur. tetapi agar alat atau sistem ini dapat diimplementasikan dengan benar, ruang lingkup pengumpulan data harus mengakomodasi semua kemungkinan aktivitas sistem produksi. Berikut adalah masalah yang dihadapi saat ini serta alternatif solusi perbaikan.
a. Masalah
Masalah utama aktivitas respon abnormalitas yaitu setelah seorang mengidentifikasi abnormalitas yang muncul, maka orang tersebut harus melihat dan memahami terlebih dahulu sistem flowchart respon abnormalitas tersebut untuk melakukan suatu penyelesaian baik secara individu ataupun dengan bagian lain. Individu tersebut juga perlu mendata secara manual jenis dan lamanya waktu abnormalitas tersebut diselesaikan. Selain itu, layout yang ada di BDI Factory belum sesuai dengan standar industri sehingga terdapat banyak barang yang berada tidak di tempatnya.
b. Solusi Perbaikan
Dibuatnya suatu sistem yang mana operator hanya perlu mengidentifikasi permasalahan yang muncul, lalu secara otomatis bagian lain yang berkaitan (dengan abnormalitas yang muncul) akan mendapatkan sinyal untuk melakukan penyelesaian di area yang bermasalah. Sementara terkait pendataan, kolaborasi beberapa aplikasi akan ditambahkan ke penelitian untuk pengumpulan data yang lebih besar dalam produksi proses untuk sistem visualisasi informasi yang lebih rumit dan akurat. Selain itu, dapat menggunakan dashboard untuk menampilkan informasi mengenai semua proses ataupun abnormalitas yang ada pada lantai produksi dan dapat mengontrol proses produksi secara realtime serta dapat mencatat konsumsi daya shop floor production, konsumsi daya mengenai semua mesin di shop floor production dan efisiensi manajemen sumber daya manusia. Efisiensi dibagi dan direpresentasikan dalam grafik garis yang menunjukkan efisiensi sebelumnya, saat ini, dan target mendatang. Pengumpulan data dan pengolahan dapat memungkinkan perusahaan untuk memiliki tingkat kontrol yang lebih tinggi atas sumber daya produksi.
Penyesuaian layout dan shop floor di BDI Factory merupakan salah satu langkah yang tepat guna mendukung proses produksi yang lebih efektif dan efisien. Shop Floor dibuat sesuai dengan standar factory dimana terdapat pedestrian, area produksi, area material dan lain sebagainya. Dengan adanya layout dan shop floor menjadikan barang di factory memiliki ruang masing-masing sehingga saat dibutuhkan tidak membutuhkan waktu yang lama untuk mencarinya.
3. Identifikasi Kemungkinan Kesulitan Serta Dampak Positif Setiap Alternatif Solusi
Perbaikan Visualisasi Dan Sistem Respons
a. Alat bantu visualisasi
1. Flowchart sebagai alat bantu visualisasi dan sistem respon abnormalitas yang ada di setiap lini produksi. Kemungkinan kesulitan serta dampak positif yang ditimbulkan dari alternatif solusi adalah sebagai berikut:
2. Visualisasi Dashboard
a) Kemungkinan Kesulitan
b) Dampak Positif
1) Karakter Proses
Perbaikan visualisasi dan respon abnormalitas ini akan menyederhanakan alur dan rantai koordinasi penyelesaian masalah sehingga kebutuhan penyelesaian masalah dapat direspon dengan cepat
2) Jenis Mesin
Jenis mesin atau alat yang digunakan adalah Digital Control System yang terhubung dengan sistem kontrol bagian lain, digunakan di area mesin injeksi untuk mempermudah pemberian sinyal abnormalitas serta pendataan abnormalitas terkait.
3) Lokasi Kerja
Pada sistem yang dulu, untuk mempermudah pemberian sinyal respon abnormalitas, bagian lain yang berkaitan dengan penyelesaian masalah seperti maintenance harus berada di dekat area produksi atau mesin, sementara untuk solusi perbaikan ini, bagian lain yang terkait bisa fokus melakukan tugas dan berada di lini masing-masing karena akan mendapatkan sinyal secara online jika muncul suatu abnormalitas yang berhubungan dengan bidang tersebut.
Pembuatan Shop Floor Control
Kemungkinan kesulitan serta dampak positif yang ditimbulkan dari alternatif solusi
adalah sebagai berikut:
4. TSK & TSKK
a) Kemungkinan Kesulitan
Standar TSK digunakan untuk melihat urutan kerja dan berapa lama waktu kerja tersebut berlangsung akan mudah dimengerti, dipergunakan juga untuk menemukan poin-poin yang diperlukan untuk melakukan kaizen pekerjaan. Sedangkan untuk standar TSKK digunakan untuk menggambarkan gerakan orang dengan lay out dalam satu siklus. Tabel standarisasi kerja ini dipakai juga sebagai alat untuk pengawasan kerja yang dapat langsung terlihat.
a) Kemungkinan Kesulitan
Kesulitan dalam penerapan SCW adalah proses integrasi antara algoritma DCS dengan keadaan aktual yang ada di lapangan.
b) Dampak Positif
Dengan menerapkan SCW dapat menghindari kesalahan penanganan kondisi abnormal yang dapat mengakibatkan terjadinya kecelakaan kerja, kerusakan mesin, mengurangi waste pada proses maupun material, defect produk atau pencemaran lingkungan.
Perencanaan kerja proses perbaikan visualisasi dan sistem respons terhadap abnormalitas akan dilakukan untuk memastikan proses perbaikan ini berjalan sesuai dengan rencana. Pada sub bab ini akan dirancang rencana kerja yang telah disesuaikan dengan kebutuhan perusahaan yaitu terdiri atas flowchart, sistem Stop-Call-Wait (SCW) pada DCS, dan shop floor control.
Perbaikan yang dilakukan terhadap sistem respons terhadap abnormalitas pada area produksi adalah dengan membuat visual kontrol untuk sistem Stop-Call-Wait (SCW) yang awalnya menggunakan andon pada mesin telah dipermudah dengan visualisasi pada DCS. SCW pada sistem DCS akan mempermudah komunikasi terhadap pihak terkait secara real time dan para pengambil keputusan dapat segera bertindak untuk menyelesaikan abnormalitas yang ada. Tidak berhenti disana, telah diberikan alur penanganan untuk kegiatan yang tidak normal (abnormality) lewat pembuatan flowchart proses Stop-Call-Wait (SCW). Selanjutnya perbaikan visual control juga diterapkan lewat implementasi shop floor control yang berorientasi pada kelancaran transportasi dan mobilitas di area produksi. Dengan pembaharuan shop floor control ini kegiatan loading-unloading dan mobilitas kerja dalam area produksi menjadi lebih terstandarisasi serta mengurangi potensi kegiatan abnormalitas.
Solusi perbaikan ini akan diterapkan di area produksi (mesin dan QC), gudang finish good, dan gudang raw material. Proses di dan antar bagian tersebut akan dipelajari dan diperbaiki, setiap bagian tersebut bertanggung jawab untuk memberikan knowledge proses atau alur perintah suatu keputusan dibuat, mengikuti brainstorming terkait rancang perbaikan respon abnormalitas yang baru, serta bertanggung jawab untuk memastikan anggota bagian tersebut mengerti sistem perbaikan yang baru.
a. Rencana kerja perbaikan Visualisasi
Visualisasi alur untuk merespon abnormalitas akan dilakukan dengan memasang poster flowchart pada setiap lini agar operator atau penemu abnormalitas memahami alur penyelesaian masalah. Visualisasi juga akan diterapkan pada monitor kontrol pada alat DCS. Selain itu, perbaikan visualisasi juga akan dilakukan dengan memperbaiki layout yang ada di BDI Factory saat ini sehingga semua area tampak lebih jelas dan mencegah terjadinya kesalahan dalam melakukan proses produksi.
b. Rencana Kerja Perbaikan Respon Abnormalitas
1) Membuat alur respon abnormalitas, alur dapat dilihat pada berkas berikut iniDalam menyelesaikan solusi perbaikan visualisasi dan sistem respons terhadap abnormalitas diperlukan rencana kerja sistem visualisasi dan respons terhadap abnormalitas tersebut. Berikut ini adalah Proses untuk mendapatkan persetujuan rencana kerja perbaikan yang akan dijelaskan pada Gambar dibawah ini. Alur memperoleh persetujuan dalam melakukan perbaikan Proses Perbaikan Visualisasi dan Sistem Respons Terhadap Abnormalitas.