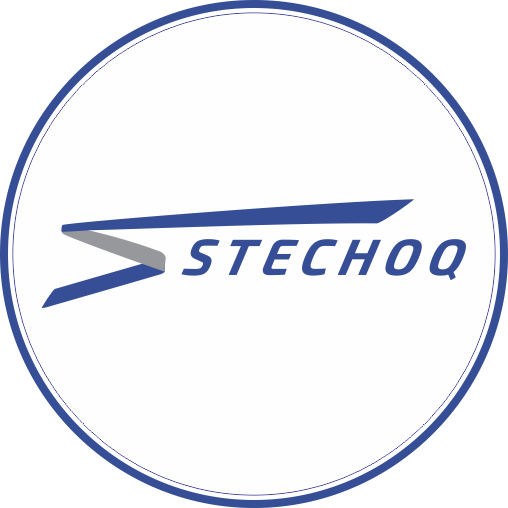
Proses pemilihan motor, seperti yang ditunjukkan pada gambar 3.4.1, dapat dimulai segera setelah semua parameter beban ditetapkan.
Proses pemilihan motor seperti yang dijelaskan di sini juga menjelaskan popularitas program Motor Sizing. Proses penghitungan ulang persyaratan torsi untuk setiap kombinasi motor/penggerak individu bisa sangat memakan waktu mengingat banyaknya jumlah motor yang tersedia di industri. Program/software motor sizing dapat mempersingkat waktu tersebut. Yang perlu diingat, tujuan dari Motor Sizing adalah untuk menemukan motor yang optimal untuk aplikasi dan itu hanya dapat dicapai dengan pilihan yang cukup tersedia, yaitu dengan sejumlah besar motor yang berlaku.
Sebelum proses pemilihan aktual berdasarkan perbandingan inersia, kecepatan dan torsi, masuk akal untuk memutuskan teknologi motor mana yang paling cocok untuk aplikasi tersebut. Metode ini akan membatasi jumlah motor yang perlu diselidiki dan dengan demikian akan mengurangi waktu yang dibutuhkan untuk menemukan motor yang optimal.
Teknologi motor yang biasa digunakan untuk aplikasi servo adalah:
Stepper
Brushed DC
BLDC (Magnet Permanen)
AC Sinkron
AC Asinkron (Motor Induksi)
Teknologi DC Brushless dan Synchronous AC sebenarnya identik; beberapa produsen lebih suka menyebutnya DC Brushless atau BLDC, yang lain lebih suka menggunakan AC Synchronous atau AC Servo.
Sementara empat teknologi pertama yang terdaftar biasanya digunakan untuk kontrol posisi, teknologi AC Asinkron sangat populer untuk aplikasi kecepatan konstan, tetapi juga cocok untuk aplikasi kontrol kecepatan dan torsi.
Faktor | Stepper | DC | BLDC | Induksi | Komentar |
Biaya rendah |
Y |
Y |
Y |
N | Biaya terendah biasanya dengan motor stepper atau motor DC; biaya motor BLDC sedikit lebih tinggi. |
Pengoperasian yang lancar (kebisingan minimal, getaran) |
N |
Y |
Y |
N | Kinerja komutasi yang tinggi, seperti komutasi sinusoidal, akan berkontribusi untuk membuat operasi motor BLDC lebih lancar. |
Kecepatan tinggi | N | Y | Y | N | Motor stepper biasanya tidak berputar lebih cepat dari 3000 rpm. |
Daya tinggi | N | N | Y | Y | Motor stepper dan motor DC biasanya tidak tersedia pada kisaran di atas 1 kiloWatt |
Rasio Torsi ke Ukuran Tinggi |
Y |
N |
Y |
Y | Motor BLDC memberikan spektrum torsi yang lebih baik seiring kecepatan meningkat, sementara kinerja motor stepper turun secara signifikan pada kecepatan yang lebih tinggi. |
Kemudahan penggunaan | Y | N | N | N | Tidak ada umpan balik dan tidak perlu penyetelan servo. |
Sirkuit Kontrol Paling Sederhana | N | Y | N | N | Semua teknologi motor, selain DC Brush, memerlukan lebih dari satu rangkaian amplifier per motor. |
1) Motor Stepper
Motor stepper pada dasarnya adalah motor DC brushless. Mereka memposisikan diri dan mereka tidak memerlukan encoder untuk umpan balik posisi. Namun, beberapa aplikasi mungkin menggunakan encoder hanya untuk tujuan mendeteksi "kemacetan" selama gerakan.
Motor stepper menghasilkan torsi tinggi untuk ukuran dan berat tertentu. Namun, torsi yang tersedia dari motor stepper turun drastis dengan kecepatan yang lebih tinggi dan kurva kinerja yang kompleks (torsi di atas kecepatan) memperumit pemilihan untuk aplikasi tertentu. Kecepatan maksimum mereka berada di sekitar 5000 rpm dengan torsi yang sangat rendah. Rentang daya motor stepper hingga beberapa ratus watt, tetapi hampir tidak di atas level itu.
Kelemahan utama motor stepper adalah kebisingan dan getaran yang dihasilkannya. Terutama getaran dapat mempengaruhi masa pakai sistem mekanis secara signifikan. Namun, ada langkah-langkah untuk mengurangi getaran seperti teknik penggerak microstepping atau peredam mekanis, tetapi biasanya tidak menghilangkan masalah sepenuhnya.
2) Motor Brushed DC
Motor DC Brush cocok untuk berbagai aplikasi, terutama untuk penentuan posisi, tetapi juga untuk kontrol kecepatan dan torsi. Mereka memang membutuhkan encoder untuk aplikasi pemosisian.
Motor DC Brush tersedia dalam berbagai ukuran, hingga beberapa kilo watt. Rentang kecepatannya bisa mencapai 10.000 rpm dan bahkan lebih tinggi. Mereka berjalan lancar dan relatif tenang.
Kerugian utama dari motor DC Brush adalah sikatnya (brush), yang aus seiring waktu dan perlu diganti. Mereka juga dapat bertanggung jawab untuk busur listrik.
Kelemahan lain adalah bahwa motor DC Brush memberikan torsi yang relatif rendah dibandingkan dengan ukuran dan beratnya.
3) BLDC (Brushless DC)
Sama seperti motor DC Brush, motor DC Brushless membutuhkan encoder untuk umpan balik posisi. Namun, ini adalah teknologi motor yang paling banyak digunakan untuk aplikasi servo. Motor DC tanpa sikat berjalan dengan relatif mulus dan senyap; mereka tidak memerlukan sikat mekanis untuk pergantian.
Karena fitur termodinamika yang sangat baik, ia mampu menghasilkan torsi tinggi untuk ukuran tertentu. Motor DC Brushless tersedia dalam rentang daya yang luas dan dapat beroperasi pada kecepatan sangat tinggi hingga 30.000 rpm dan bahkan lebih.
Kelemahan dari motor DC Brushless adalah harganya yang mahal karena penggunaan bahan magnetik tanah jarang untuk menghasilkan torsi. Mereka juga membutuhkan amplifier yang cukup kompleks dan karenanya lebih mahal.
4) Motor Induksi
Secara tradisional, motor induksi AC telah digunakan sebagian besar untuk aplikasi kecepatan konstan. Desainnya sederhana (tidak ada magnet di rotor atau stator) dan karenanya mereka bekerja dengan andal untuk waktu yang lama; mereka berbiaya rendah ketika digunakan untuk aplikasi kecepatan konstan.
Karena munculnya kontrol elektronik yang lebih canggih, yang membawa kompleksitas tertentu dan menambah total biaya sistem, motor induksi AC dapat digunakan untuk aplikasi kontrol kecepatan dan torsi. Meskipun secara teknis layak dengan teknik kontrol elektronik ini, motor induksi AC jarang digunakan untuk aplikasi penentuan posisi.
Kriteria seleksi dasar adalah:
Kecepatan pengenal motor harus sama dengan atau melebihi kecepatan maksimum aplikasi
Torsi intermiten motor harus sama atau melebihi torsi maksimum (intermiten) beban5
Torsi pengenal motor harus sama dengan atau melebihi torsi RMS beban
Rasio inersia beban terhadap inersia rotor harus sama dengan atau kurang dari 6:16
Tugas pertama dan paling mudah dalam proses pemilihan motor adalah membandingkan kecepatan pengenal motor dengan kecepatan maksimum seperti yang dipersyaratkan oleh aplikasi.
Namun, kecepatan rated motor serta torsi rated adalah data yang kurang lebih dapat diinterpretasikan dari profil performa motor (torsi vs. kecepatan) dan biasanya ditentukan oleh pabrikan (akan dijelaskan subbab 2.3.4 Interpretasi Torsi/ Kurva Kecepatan)
Aturan praktis yang umum digunakan adalah bahwa momen inersia armature/rotor harus sesuai dengan momen inersia beban, yaitu rasio 1:1 antara beban dan inersia motor akan menjadi skenario yang ideal.
Alasan untuk mencocokkan momen inersia adalah:
1. Motor tidak akan dapat mengontrol kecepatan dan posisi beban secara akurat jika beban terlalu berat. Hal ini akan mengakibatkan ketidakstabilan sistem seperti getaran dan dapat menyebabkan kerusakan mekanis. Perubahan cepat dalam kecepatan atau posisi menjadi sangat sulit.
2. Jika inersia beban terlalu ringan, yaitu motor terlalu besar untuk aplikasi, sebagian besar daya akan digunakan untuk mempercepat atau memperlambat rotor, daripada beban. Dari sudut pandang konsumsi daya, hal ini merupakan pemborosan daya dan juga dapat menyebabkan panas berlebih pada motor.
Dalam hal efisiensi rasio 1:1 antara beban dan inersia motor memberikan transfer daya yang optimal. Namun, rasio 1:1 jarang berguna dalam aplikasi yang sebenarnya, karena akan membutuhkan motor yang lebih besar. Dari segi penghematan biaya, khususnya konsumsi energi, hal ini jarang dapat diterima
Ternyata rasio inersia tidak terlalu kritis sama sekali. Namun, satu pertanyaan yang sedang hangat dibahas di antara para ahli adalah seberapa tinggi ketidakcocokan inersia dapat diregangkan.
Aturan yang banyak digunakan di antara produsen adalah:
Jika rasio beban di atas inersia rotor melebihi kisaran tertentu (untuk motor servo 6:1) pertimbangkan penggunaan gearbox, tingkatkan rasio transmisi dari gearbox yang ada, tingkatkan pitch ball screw, dll. Ini akan mengurangi inersia yang dipantulkan ke motornya. Motor servo tidak boleh dioperasikan dengan rasio 10:1.
Selama proses desain pastikan Anda memilih rasio roda gigi, jarak sekrup, dll. dengan hati-hati, karena ini akan mengurangi inersia yang dipantulkan ke motor dan dengan demikian memerlukan motor yang lebih kecil. Inersia yang dipantulkan adalah inersia beban dibagi dengan rasio kuadrat.
Titik untuk membatasi rentang ketidakcocokan inersia adalah untuk menyederhanakan penyetelan sistem. Perubahan kecepatan yang cepat dan pemosisian menjadi sangat sulit jika rasio ketidakcocokan terlalu tinggi. Beban benar-benar dapat menggerakkan motor selama deselerasi dan akibatnya dapat menyebabkan overshooting dan waktu pengendapan yang lama dan tidak masuk akal.
Bosch Rexroth, misalnya, merekomendasikan 'standar yang baik' untuk ketidakcocokan inersia sebagai berikut:
<2:1 untuk penentuan posisi cepat (quick positioning)
<5:1 untuk pemosisian sedang (moderate positioning)
< 10:1 untuk perubahan kecepatan yang cepat
Rasio inersia dapat digunakan sebagai indikator kemungkinan masalah stabilitas. Namun, itu mungkin bukan penyebab masalahnya. Pastikan rasio inersia berada dalam kisaran yang wajar untuk mencegah masalah apa pun, tetapi juga periksa kekakuan dan linieritas sistem. Serangan balik, misalnya, dapat menyebabkan masalah serupa seperti yang diamati dengan rasio ketidakcocokan inersia yang berlebihan.
Rasio ketidakcocokan yang jauh lebih tinggi daripada 10:1 dapat dicapai dengan penyetelan sistem yang tepat, namun, proses penyetelan yang sebenarnya akan memakan waktu yang sangat lama.
Kinerja kedua teknologi motor, servo brush/brushless di satu sisi dan motor stepper di sisi lain, paling efektif ditunjukkan oleh grafik yang menggambarkan hubungan antara torsi dan kecepatan, yaitu torsi apa yang tersedia pada kecepatan berapa. Sementara sistem stepper juga merupakan sistem servo, ada perbedaan yang signifikan antara kurva kinerja servo dan motor stepper. Pengetahuan mendalam tentang perbedaan dan interpretasi yang tepat dari kurva kinerja sangat penting untuk proses pemilihan motor.
Tidak dapat cukup ditekankan bahwa membandingkan data motor dengan torsi beban dan persyaratan kecepatan harus diselesaikan hanya berdasarkan informasi torsi vs. kecepatan yang realistis (jika data tersebut disediakan), bukan hanya torsi dan kecepatan terukur.
Ketika membandingkan motor servo dari berbagai pabrikan, selalu menguntungkan untuk menggunakan kurva kinerjanya, yaitu torsi di atas kecepatan atau sebaliknya, yang pada gilirannya memerlukan pemahaman yang jelas tentang kurva ini. Misalnya, apakah torsi maksimum tersedia pada kecepatan nol atau maksimum? Apakah kurva mengacu pada motor saja atau kombinasi motor/penggerak? Berapa suhu lingkungan yang diasumsikan? Mungkin ada perbedaan kinerja yang cukup besar antara 25 ° C dan 40 ° C. Faktor lainnya adalah tegangan, yang secara signifikan mempengaruhi kecepatan tertinggi.
Data motor yang diperoleh dari kurva kinerja dan tercantum pada lembar data (seperti torsi terukur, kecepatan terukur) sangat bergantung pada interpretasi pabrikan. Ini bisa menjadi konservatif dan dengan demikian meninggalkan potensi untuk menggunakan motor di luar parameter pengenal dalam keadaan tertentu. Untuk alasan pemasaran interpretasi mungkin lebih agresif terhadap kecepatan yang lebih tinggi atau torsi yang lebih tinggi.
Gambar berikut mewakili kurva torsi vs. kecepatan untuk keduanya, sistem servo brushed dan brushless.
Servo biasanya memiliki dua zona:
1. Zona tugas kontinu, di mana operasi berkelanjutan dimungkinkan tanpa motor terlalu panas.
2. Zona tugas intermiten di mana operasi, terutama akselerasi, hanya dimungkinkan secara intermiten. Waktu dimana motor atau kombinasi motor/penggerak dapat mempertahankan torsi intermiten terbatas dan sangat spesifik untuk motor. Biasanya terletak antara 0,05 dan 30+ detik (Lihat lembar data pabrikan).
Catatan : Kontributor utama torsi puncak/intermiten yang dibutuhkan adalah akselerasi, karena torsi sama dengan inersia dikalikan percepatan. Selama kecepatan konstan motor hanya perlu mempertahankan torsi konstan karena gaya gesekan
Lembar data motor servo biasanya mencantumkan torsi puncak (baik TPS stall atau TPR terukur) yang 2 hingga 3 kali lebih tinggi daripada torsi kontinu (baik stall TCS atau TCR terukur).
Perlu juga diketahui tegangan dan arus yang dibutuhkan untuk mengoperasikan motor. Gambar 3.4.2.3.2 menunjukkan pengaruh tegangan bus terhadap kurva torsi/kecepatan. Tegangan yang lebih tinggi memberikan kecepatan yang lebih tinggi. Semakin tinggi persyaratan torsi, semakin tinggi arusnya. Oleh karena itu penting untuk mempertimbangkan konstanta torsi motor kt (kt = Torsi per Amp).
Beberapa produsen mencantumkan kecepatan maksimum yang merupakan kecepatan pada tegangan penuh dan tanpa beban. Pendekatan yang lebih konservatif, tetapi lebih andal adalah dengan membuat daftar torsi kontinu dan torsi intermiten terukur yang merupakan persimpangan kurva torsi puncak (intermiten) dan torsi kontinu dengan kecepatan terukur (biasanya 3000+ rpm).
Kecepatan pengenal pada gilirannya biasanya ditetapkan pada titik yang mencakup kisaran tingkat torsi yang agak konstan, sampai, pada kecepatan tertentu torsi tiba-tiba mundur.
Dalam hal membandingkan kebutuhan aplikasi dengan kinerja motor, torsi RMS aplikasi dan kecepatan maksimum harus diverifikasi dengan kurva torsi/kecepatan kontinu motor. Torsi puncak aplikasi, yang merupakan fungsi dari inersia dan akselerasi, harus dibandingkan dengan kurva torsi/kecepatan intermiten. Dalam hal ini berlaku syarat waktu terbatas yang disebutkan sebelumnya dan harus diperhitungkan.
Gambar berikut menunjukkan aplikasi yang persyaratan torsi dan kecepatannya berada dalam kisaran kinerja motor yang baik.
Untuk tujuan referensi, gambar berikut menunjukkan aplikasi yang persyaratan torsi dan kecepatannya berada di luar jangkauan kinerja motor.
Dalam kasus tertentu dimungkinkan untuk menggunakan motor di luar data pengenal, baik torsi atau kecepatan. Contoh berikut mengasumsikan kecepatan yang lebih tinggi dari kecepatan pengenal motor, sedangkan persyaratan torsi rendah.
Contoh ini menunjukkan kecepatan aplikasi yang melampaui kecepatan pengenal motor, namun, dengan torsi RMS yang diperlukan cukup rendah untuk dicakup oleh zona tugas kontinu.
Contoh berikutnya menunjukkan aplikasi torsi RMS kecepatan rendah dan tinggi.
Contoh kedua ini menunjukkan torsi RMS aplikasi yang melampaui torsi kontinu pengenal motor, namun, dengan persyaratan kecepatan yang cukup rendah untuk dicakup oleh zona tugas kontinu.
Bentuk kurva performa motor stepper biasanya sama sekali berbeda dengan kurva motor servo. Jika karakteristiknya disalahpahami dan diterapkan berdasarkan miskonsepsi, penerapannya akan gagal. Biaya yang melekat pada kegagalan ini mungkin signifikan.
Sekilas melihat kurva kinerja motor stepper dalam gambar ini mengungkapkan betapa sulitnya menetapkan torsi atau kecepatan pengenal yang khas. Pengaturan apa pun tidak akan adil terhadap kinerja keseluruhan stepper dan dengan demikian pilihan motor stepper harus sangat spesifik untuk aplikasi. Contoh ini juga menekankan pentingnya memahami dan menganalisis kurva kinerja motor stepper.
“Stall Torque Line” pada gambar mewakili kinerja ideal karena biasanya diterbitkan oleh produsen motor stepper dan sistem penggerak. Kurva ini harus ditafsirkan sangat berbeda dari kurva motor servo. Karena sifat loop terbuka dari sistem stepper dan interaksi dinamis yang kompleks antara motor, penggerak, beban, dan profil gerak, motor stepper akan sering berhenti dengan baik sebelum mencapai garis torsi stall yang ideal. Kecuali umpan balik diberikan, sistem kontrol tidak akan dapat merespons.
Juga, bahkan torsi ideal menurun dengan cepat di atas 1 (biasanya 100 – 600 rpm) menjadi hanya 5 – 10% dari torsi penahan TH pada H (biasanya < 3000 rpm).
Jadi, ketika memilih sistem penggerak motor stepper, kecuali jika aplikasi didefinisikan dengan sangat baik dan beban tidak berubah secara signifikan, disarankan agar perancang menggunakan kurva kecepatan torsi yang dikurangi yang serupa dengan "Jalur Operasi Realistis" seperti yang ditunjukkan pada gambar sebelumnya. Garis operasi yang realistis agak sewenang-wenang didefinisikan sebagai 50% dari garis torsi kios. Pilihan yang dihasilkan akan jauh lebih kuat dan aplikasi biasanya akan jauh lebih berhasil.
Meskipun perhitungan perangkat mekanis yang kompleks tampaknya sangat rumit pada pandangan pertama, matematika di baliknya sangat lurus ke depan selama ada pemahaman bahwa sebagian besar komponen berasal dari bentuk dasar (kebanyakan silinder). Juga membantu adalah pengetahuan bahwa transmisi kecepatan sebagian besar dilakukan dengan menggunakan dua silinder (roda gigi, katrol, dll.) dan bahwa setiap transmisi berdampak pada akselerasi, inersia dan torsi yang direfleksikan ke motor.
Pemilihan motor didasarkan pada perbandingan kecepatan, inersia dan torsi. Perhitungan perangkat mekanis digunakan untuk menentukan parameter ini.
Bahkan perangkat mekanis yang paling kompleks pun dihitung berdasarkan tiga komponen "dasar":
Silinder padat
Silinder berongga
Persegi Panjang Padat
Perhitungan komponen-komponen ini ditambah beberapa persamaan fundamental dijelaskan selanjutnya.
1) Persamaan Dasar
Berat
Berat (kgf) = Volume (m3) x Berat jenis (kgf/m3)
Massa
Massa (kg) = Berat (N)/Gravitasi (m/s2)
Radius
Radius (m) = Diameter (m)/2
Torsi total
Torsi total = Torsi akselerasi + Torsi konstan
Torsi akselerasi
Torsi akselerasi (Nm) = Momen Inersia (kg.m2) x percepatan sudut (rad/s2)
Percepatan sudut
Percepatan sudut (rad/s2) = Kecepatan sudut maksimum (rad/s) / waktu akselerasi (s)
Torsi konstan
Tc adalah Torsi akibat gaya-gaya yang konstan selama gerakan seperti gaya gesek, gravitasi, push-pull, preload, effisiensi, dsb.
Torsi RMS
Torsi RMS atau Root Mean Square adalah Torsi "rata-rata" selama duty cycle
Gaya gesek
Gaya gesek (N) = koefisien gesek x Berat beban (N)
2) Silinder Pejal
Persamaan :
Aend | Luas penampang atau sisi silinder |
g | percepatan gravitasi = 9,81 m/s2 |
Ja-a | Inersia terhadap sumbu a-a |
Jb-b | Inersia terhadap sumbu b-b |
L | Panjang silinder |
m | Massa |
ρ � | Kepadatan massa bahan |
r | Radius |
V | Volume |
W | Berat |
3) Silinder Berongga
Persamaan :
Aend | Area sisi ujung silinder |
g | Konstanta Gravitasi = 9,81 m/s2 |
Ja-a | Inersia terhadap sumbu a-a |
Jb-b | Inersia terhadap sumbu b-b |
L | Panjang silinder |
m | Massa |
ρ � | Kepadatan massa bahan |
ro | Radius Luar |
ri | Radius dalam |
V | Volume |
W | Berat |
3) Balok persegi panjang
Persamaan :
Aend | Luas penampang ujung balok |
Aside | Luas area sisi balok |
h | Tinggi balok |
Ja-a | Inersia terhadap sumbu a-a |
Jb-b | Inersia terhadap sumbu b-b |
L | Panjang balok |
m | Massa |
V | Volume balok |
w | Lebar balok |
Proses Motor sizing : Perhitungan beban dan inersia mekanisme penggerak
Bab ini menjelaskan perhitungan mekanisme yang lebih kompleks. Meskipun matematika sebenarnya di balik perhitungan ini cukup jelas, namun tetap bermanfaat untuk mengetahui beberapa keadaan:
Semua perangkat mekanik yang akan dibahas berikut mendukung baik itu gerak putar maupun gerak linier. Beberapa perangkat putar, seperti gearbox, hanya digunakan untuk transmisi kecepatan (mempengaruhi kecepatan yang dibutuhkan dari motor) dan lainnya, seperti meja putar, adalah beban aktual. Semua perangkat linier juga beban, yaitu mereka melakukan pekerjaan yang sebenarnya seperti yang didefinisikan oleh insinyur.
Perangkat mekanis dapat dikategorikan sebagai berikut:
Beban Putar :
Nip Roll
Meja Putar
Winder
Untuk perhitungan perangkat linier, perlu diketahui lead atau pitch, yang mewakili panjang linier yang ditempuh selama satu putaran pada poros input. Timbal atau pitch juga dapat dihitung, misalnya, untuk konveyor, dengan melihat keliling puli sisi motor.
Konveyor
Aktuator Linier
Leadscrew
Rack-Pinion
Transmisi Kecepatan
Untuk perhitungan kecepatan alat transmisi perlu diketahui rasio transmisi. Dalam kasus timing belt, rasio dapat ditentukan sebagai rasio antara diameter puli sisi motor dan diameter puli sisi beban.
Belt-Pulley (Timing Belt)
Gearbox (Servo Reducer)
Rem
Kopel
Disk
Ada juga dua parameter penting yang diperlukan untuk perhitungan perangkat mekanis; mereka dapat, bagaimanapun, menyebabkan banyak kebingungan, baik karena kurangnya pengetahuan atau hanya karena data tidak tersedia dari produsen perangkat.
Parameter ini adalah:
2. Efisiensi Mekanisme
Kedua parameter juga sangat penting untuk aplikasi vertikal linier, karena mereka mempengaruhi torsi konstan secara berbeda selama gerakan ke atas dan ke bawah.
Koefisien gesekan adalah besaran tak berdimensi dan digunakan untuk menghitung gaya gesekan. Dalam hal perangkat mekanis seperti yang dibahas dalam bab berikut, gaya gesekan menggambarkan gesekan antara dua permukaan. Misalnya, dalam kasus leadscrew, gaya gesekan berlaku antara sekrup dan mur. Dalam kebanyakan kasus, cukup menggunakan koefisien sekitar 0,15 yang mewakili baja pada baja (dilumasi).
Efisiensi mekanisme juga merupakan besaran tak berdimensi antara 0 dan 1,0 atau 0 hingga 100%. Ini menjelaskan kerugian, misalnya, antara dua roda gigi di gearbox atau antara sekrup dan mur leadscrew. Misalnya, efisiensi sekrup bola bisa antara ~0,85 dan 0,95.
1) Disk
Disk umumnya merupakan komponen mekanis yang paling banyak digunakan dalam hal perhitungan inersia. Disk dapat digunakan untuk menyerupai komponen mekanis lainnya seperti katrol, sekrup, pinion, roda gigi, kopling, dll.
Secara umum, piringan (disk) tidak lain adalah silinder padat (atau berongga) dan dengan demikian persamaan untuk piringan dan silinder padat (atau berongga) adalah sama.
g | Percepatan Gravitasi = 9,81 m/s2 |
JDisk | Inersia Disk |
L | Panjang/Tebal Disk |
m | Massa |
ρ � | Kepadatan massa bahan |
r | Radius |
W | Berat |
2) Penggerak Rantai
Penggerak rantai terdiri dari dua roda gigi (sproket) dan rantai. Selanjutnya piringan di sisi motor disebut sproket penggerak, piringan di sisi beban disebut sproket penggerak. Kedua sproket dihitung seperti piringan biasa (silinder) atau, jika perlu, silinder berongga.
g | Percepatan Gravitasi = 9,81 m/s2 |
JDisk | Inersia Disk |
L | Panjang/Tebal Disk |
m | Massa |
ρ � | Kepadatan massa bahan |
r | Radius |
W | Berat |
Kecepatan transmisi perangkat sproket rantai diturunkan dari diameter sproket atau jumlah gigi pada kedua sproket.
Nr | rasio transmisi |
DTL | Diameter sproket di sisi beban |
DSM | Diameter sproket di sisi motor |
NTL | Jumlah gigi di sisi beban |
NTM | Jumlah gigi di sisi motor |
Inersia total perangkat sproket rantai mencakup inersia sproket penggerak, kelembaman rantai yang direfleksikan ke sisi motor dan kelembaman sproket yang digerakkan yang direfleksikan ke sisi motor.
e | Efisiensi mekanisme |
g | Konstanta Gravitasi = 9,81 m-s2 = 386 in-s2 |
DSM | Diameter sproket di sisi motor |
Jtotal | Inersia total termasuk beban |
JSM | Inersia sproket di sisi motor |
JTL->M | Inersia sproket sisi beban direfleksikan ke motor |
JC->M | Inersia rantai direfleksikan ke motor |
JL->M | Memuat inersia yang direfleksikan ke motor |
JTL | Inersia sproket sisi beban |
JL | Muat inersia |
Nr | Rasio transmisi |
Wc | Berat rantai |
e | Efisiensi Mekanisme |
Nr | Rasio transmisi |
TL->M | Torsi beban direfleksikan ke motor |
TL | Beban torsi |
3) Coupling
Kopling tidak lain adalah silinder padat (atau berongga) dan dengan demikian persamaan untuk kopling dan silinder padat (berongga) adalah sama. Biasanya kopling dihitung seperti silinder berongga
Aend | Area sisi ujung silinder |
g | Konstanta Gravitasi = 9,81 m-s2 / 386 in-s2 |
JC | Inersia kopling |
L | Panjang kopling |
m | Massa |
ρ � | Kepadatan massa bahan |
ro | Radius Luar |
ri | Radius dalam |
V | Volume |
W | Berat |
4) Roda Gigi (Gear)
Gears (pasangan roda gigi) pada dasarnya adalah dua roda gigi di mana satu roda (sisi motor) menggerakkan yang lain (sisi beban). Kedua roda dihitung seperti piringan biasa (silinder) atau, jika perlu, silinder berongga.
g | Percepatan Gravitasi = 9,81 m/s2 |
JDisk | Inersia Disk |
L | Panjang/Tebal Disk |
m | Massa |
ρ � | Kepadatan massa bahan |
r | Radius |
W | Berat |
Nr | Rasio transmisi |
DGL | Diameter roda gigidi sisi beban |
DGM | Diameter roda gigi di sisi motor |
NTL | Jumlah gigi di sisi beban |
NTM | Jumlah gigi di sisi motor |
e | Efisiensi mekanisme |
g | Konstanta Gravitasi = 9,81 m-s2 = 386 in-s2 |
Jtotal | Inersia total termasuk beban |
JGM | Inersia gigi di sisi motor |
JGL->M | Memuat inersia roda gigi samping yang direfleksikan ke motor |
JL->M | Memuat inersia yang direfleksikan ke motor |
JGL | Memuat inersia roda gigi samping |
JL | Muat inersia |
Nr | rasio transmisi |
e | Efisiensi Mekanisme |
Nr | Rasio transmisi |
TL->M | Torsi beban direfleksikan ke motor |
TL | Beban torsi |
5) Gearbox (Reducer)
Gearbox dan roda gigi yang didokumentasikan sebelumnya hampir identik dalam fungsinya, tetapi dalam hal ini kami tidak memperhatikan pekerjaan bagian dalam gearbox. Semua yang benar-benar penting untuk diketahui adalah inersia gearbox, kecepatan transmisi dan efisiensi ditambah inersia beban. Namun matematika pada dasarnya sama.
Servo Reducer pada dasarnya identik dengan gearbox, tetapi beberapa pabrikan lebih suka menggunakan istilah yang lebih canggih daripada gearbox, karena konstruksi mekanis bagian dalamnya bisa jauh lebih kompleks daripada gearbox sederhana yang dibuat melalui roda gigi biasa. Meskipun perhitungannya sama dengan gearbox, reduksi servo memiliki keterbatasan dalam hal kecepatan dan torsi input/output.
e | Efisiensi mekanisme |
Jtotal | Inersia total termasuk beban |
JG | Inersia gearbox |
JL->M | Memuat inersia yang direfleksikan ke motor |
JL | Muat inersia |
Nr | rasio transmisi |
e | Efisiensi Mekanisme |
Nr | Rasio transmisi |
TL->M | Torsi beban direfleksikan ke motor |
TL | Beban torsi |
6) Belt-Pulley
Belt Pulley (atau timing belt) terdiri dari dua piringan (pulley) dan sebuah sabuk. Piringan pada sisi motor disebut katrol sisi motor, piringan pada sisi beban disebut katrol sisi beban. Kedua puli dihitung seperti piringan (silinder) biasa atau, jika perlu, silinder berongga.
g | Percepatan Gravitasi = 9,81 m/s2 |
JDisk | Inersia Disk |
L | Panjang/Tebal Disk |
m | Massa |
ρ � | Kepadatan massa bahan |
r | Radius |
W | Berat |
Nr | Rasio transmisi |
DPL | Diameter katrol sisi beban |
DPM | Diameter katrol samping motor |
Inersia total katrol sabuk meliputi inersia katrol sisi motor, kelembaman sabuk yang direfleksikan ke sisi motor dan kelembaman katrol sisi beban yang direfleksikan ke sisi motor.
e | Efisiensi mekanisme |
g | Konstanta Gravitasi = 9,81 m-s2 = 386 in-s2 |
DPM | Diameter Puli samping motor |
Jtotal | Inersia total termasuk beban |
JPM | Inersia Puli sisi motor |
JPL->M | Inersia Puli sisi beban direfleksikan ke motor |
JB->M | Inersia Belt direfleksikan ke motor |
JL->M | Memuat inersia yang direfleksikan ke motor |
JPL | Inersia katrol sisi beban |
JL | Inersia Beban |
Nr | Rasio transmisi |
WB | Berat Belt |
e | Efisiensi Mekanisme |
Nr | Rasio transmisi |
TL->M | Torsi beban direfleksikan ke motor |
TL | Beban torsi |
7) Konveyor
g | Percepatan Gravitasi = 9,81 m/s2 |
JDisk | Inersia Disk |
L | Panjang/Tebal Disk |
m | Massa |
ρ � | Kepadatan massa bahan |
r | Radius |
W | Berat |
Nr | Rasio transmisi |
DPL | Diameter katrol sisi beban |
DPM | Diameter katrol samping motor |
Inersia total konveyor meliputi inersia katrol sisi motor, inersia sabuk yang direfleksikan ke sisi motor dan kelembaman katrol sisi beban yang direfleksikan ke sisi motor.
e | Efisiensi mekanisme |
g | Konstanta Gravitasi = 9,81 m-s2 = 386 in-s2 |
DPM | Diameter Puli samping motor |
Jtotal | Inersia total termasuk beban |
JPM | Inersia Puli sisi motor |
JPL->M | Inersia Puli sisi beban direfleksikan ke motor |
JB->M | Inersia Belt direfleksikan ke motor |
JL->M | Memuat inersia yang direfleksikan ke motor |
JPL | Inersia katrol sisi beban |
JL | Inersia Beban |
Nr | Rasio transmisi |
WB | Berat Belt |
e | Efisiensi Mekanisme |
Nr | Rasio transmisi |
TL->M | Torsi beban direfleksikan ke motor |
TL | Beban torsi |
8) Leadscrew
Untuk menghitung inersia leadcrew, sekrup dianggap sebagai disk, sehingga inersia sekrup dihitung seperti disk. Rasio transmisi leadcrew disebut pitch (rev/in) atau lead (in/rev).
Inersia total dari leadcrew termasuk inersia beban yang direfleksikan (dalam hal ini beban berisi berat meja dan berat beban aktual) dan inersia sekrup.
g | Percepatan Gravitasi = 9,81 m/s2 |
JDisk | Inersia Disk |
L | Panjang/Tebal Disk |
m | Massa |
ρ � | Kepadatan massa bahan |
r | Radius |
W | Berat |
e | Efisiensi mekanisme |
g | Konstanta Gravitasi = 9,81 m-s2 = 386 in-s2 |
Jtotal | Inersia total termasuk beban |
JS | Inersia sekrup |
JL->M | Memuat inersia yang direfleksikan ke motor |
PS | Pitch sekrup utama |
WL | Berat Beban |
WT | Berat meja |
e | Efisiensi mekanisme |
γ � | Sudut aplikasi (Theta) |
μ � | Koefisien Gesekan |
Fg | Gaya gravitasi |
Ffr | Gaya gesekan |
FP | Gaya tarik-dorong |
PS | Pitch sekrup utama |
TL->M | Torsi beban direfleksikan ke motor |
Tp | Torsi preload |
WL | Beray Beban |
WT | Berat meja |
9) Linear Actuator
Aktuator linier sebenarnya bukanlah perangkat mekanis yang berdiri sendiri; cara kerja bagian dalam bisa berupa leadcrew atau belt- pulley (timing belt). Berikut ini mengambil pendekatan yang sangat umum untuk perhitungan aktuator linier. Perhitungan aktuator linier biasanya sangat spesifik pabrikan. Inersia, misalnya, sangat tergantung pada panjang aktuator, jenis slide dan peralatan khusus pabrikan lainnya. Silakan merujuk ke lembar data pabrikan untuk informasi rinci tentang perhitungan inersia.
e | Efisiensi mekanisme |
g | Konstanta Gravitasi = 9,81 m-s2 = 386 in-s2 |
Jtotal | Inersia total termasuk beban |
JA | Inersia aktuator |
JL->M | Memuat inersia yang direfleksikan ke motor |
PS | Pitch aktuator |
WL | Berat Beban |
WT | Berat meja (geser) |
Produsen aktuator linier biasanya menyediakan "faktor inersia" untuk menghitung inersia beban yang direfleksikan ke motor. Dalam hal ini inersia yang direfleksikan dihitung sebagai:
Inersia beban ke motor = Berat Beban x Faktor Inersia
e | Efisiensi mekanisme |
γ � | Sudut aplikasi (Theta) |
μ � | Koefisien Gesekan |
Fg | Gaya gravitasi |
Ffr | Gaya gesekan |
FP | Gaya tarik-dorong |
PS | Pitch sekrup utama |
TL->M | Torsi beban direfleksikan ke motor |
Tp | Torsi preload |
WL | Berat Beban |
WT | Berat meja |
Produsen aktuator linier tidak selalu menyediakan semua data yang diperlukan untuk persamaan seperti yang tercantum dalam bab ini, meskipun parameter seperti, misalnya koefisien gesekan, dapat berdampak pada torsi total terutama dalam aplikasi vertikal. Untuk hasil perhitungan yang tepat, silakan merujuk ke spesifikasi pabrikan