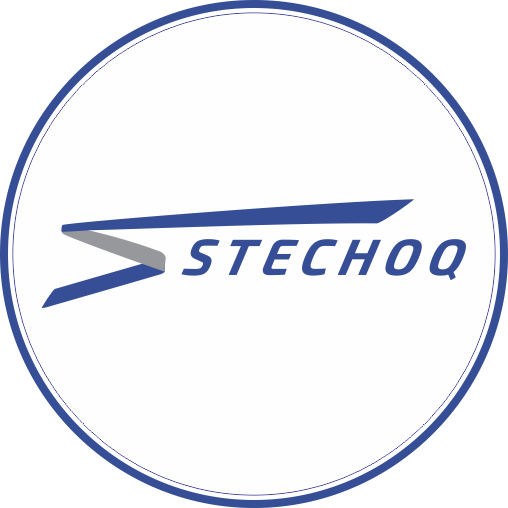
Basic Guidelines for Sheet Metal Fabrication
Panduan dasar untuk untuk melakukan proses fabrikasi pada lembaran logam (sheet metal) ini mencakup beberapa pertimbangan desain yang cukup penting untuk membantu meningkatkan kemampuan dalam manufaktur, meningkatkan penampilan, dan juga mengurangi waktu produksi secara keseluruhan.
Pada prinsip dasarnya, Fabrikasi Lembaran Logam (sheet metal) adalah proses pembentukan bagian-bagian dari lembaran logam dengan cara meninju (punching), memotong (cutting), mengecap (stamping), dan menekuk (bending). Dimulai darii File CAD 3D diubah menjadi kode mesin, yang mengontrol mesin untuk memotong dan membentuk lembaran menjadi bagian akhir dengan tepat. Bagian lembaran logam dikenal karena daya tahannya, yang membuatnya bagus untuk aplikasi penggunaan akhir (misalnya sasis). Suku cadang yang digunakan untuk prototipe volume rendah, dan produksi volume tinggi paling hemat biaya karena penyiapan awal yang besar dan biaya material. Karena bagian dibentuk dari satu lembaran logam, desain harus mempertahankan ketebalan yang seragam. Pastikan untuk mengikuti persyaratan dan toleransi desain untuk memastikan suku cadang mendekati maksud desain dan memotong lembaran logam
Bending adalah proses dimana gaya diterapkan pada lembaran logam yang menyebabkannya menekuk pada sudut dan membentuk suatu bentuk yang diinginkan. Tikungan bisa pendek atau panjang tergantung pada desain yang dibutuhkan. Pembengkokan dilakukan oleh mesin rem tekan yang dapat dimuat secara otomatis atau manual. Rem tekan tersedia dalam berbagai ukuran dan panjang yang berbeda (20-200 ton) tergantung pada persyaratan proses.
Gambar 2. Mesin Bending
Gambar 3. Proses Bending
Rem tekan berisi alat atas yang disebut punch dan alat bawah (lower tool) yang disebut die di mana lembaran logam ditempatkan, dapat dilihat pada gambar 2. Lembaran itu ditempatkan di antara keduanya dan ditahan di tempatnya oleh penahan seperti pada gambar 3. Sudut tikungan ditentukan oleh kedalaman pukulan yang memaksa lembaran ke dalam cetakan. Kedalaman ini dikontrol dengan tepat untuk mencapai tikungan yang dibutuhkan. Perkakas standar biasanya digunakan untuk pukulan dan mati. Bahan perkakas meliputi, dalam rangka meningkatkan kekuatan, kayu keras, baja karbon rendah, baja perkakas dan baja karbida.
Bagian yang akan ditekuk disediakan sebagai pola datar (flat pattern) dengan informasi tekukan. Terkadang posisi tikungan diukir dengan takik tikungan, atau takik ini bisa dipotong untuk menunjukkan pada tikungan di mana harus menekuk. Setelah laser memotong bagian yang rata, mereka dapat dikirim untuk ditekuk. Rem tekan membentuk pola datar menjadi bagian yang bengkok.
Critical Dimensions
Berikut ini adalah beberapa terminologi yang digunakan dalam lembaran logam. Desainer harus mematuhi pedoman permesinan saat merancang untuk pembengkokan. Tikungan dapat dicirikan oleh parameter ini. Beberapa dimensi kritis yang perlu dipertimbangkan ketika menyiapkan lembaran logam dalam perangkat lunak CAD adalah ketebalan lembaran logam, faktor-k dan radius tikungan. Seseorang perlu memeriksa bahwa faktor-faktor ini konsisten dengan perkakas yang akan digunakan dalam pembuatan. Panduan ini memberikan panduan penting untuk praktik desain yang baik.
Bend line – Garis lurus pada permukaan lembaran, di kedua sisi tikungan, yang menentukan ujung flens level dan awal tikungan.
Bend Radius - Jarak dari sumbu tikungan ke permukaan bagian dalam material, antara garis tikungan.
Band Angel – Sudut tikungan, diukur antara sayap bengkok dan posisi aslinya, atau sebagai sudut yang disertakan antara garis tegak lurus yang ditarik dari garis tikungan. Kadang-kadang ditentukan sebagai radius tikungan bagian dalam. Jari-jari tikungan luar sama dengan radius tikungan dalam ditambah ketebalan lembaran.
Neutral Axis – Lokasi di lembaran yang tidak diregangkan atau ditekan, dan karena itu tetap pada panjang yang konstan.
K-faktor – Lokasi sumbu netral dalam material, dihitung sebagai rasio jarak sumbu netral T, dengan ketebalan material t. Faktor K bergantung pada beberapa faktor (bahan, operasi pembengkokan, sudut tekuk, dll.) dan lebih besar dari 0,25, tetapi tidak boleh melebihi 0,50. Faktor K = T/t
Bend Allowance – Panjang sumbu netral antara garis tikungan atau panjang busur tikungan. Tunjangan tikungan yang ditambahkan ke panjang flensa sama dengan total panjang rata.
K-Factor
K-Factor adalah rasio antara sumbu netral dengan ketebalan material.
Pentingnya faktor-K dalam desain lembaran logam
Faktor K digunakan untuk menghitung pola datar karena berkaitan dengan seberapa banyak material yang diregangkan selama pembengkokan. Oleh karena itu penting untuk memiliki nilai yang benar dalam perangkat lunak CAD. Nilai K-factor harus berkisar antara 0 – 0,5. Untuk lebih tepatnya K-faktor dapat dihitung dengan mengambil rata-rata 3 sampel dari bagian bengkok dan memasukkan pengukuran kelonggaran tikungan, sudut tikungan, ketebalan material dan radius bagian dalam ke dalam rumus berikut:
Wall Thickness
Bagian perlu mempertahankan ketebalan dinding yang seragam di seluruh. Umumnya kemampuan ketebalan 0,9mm – 20mm dapat dibuat dari lembaran (<3mm) atau pelat (>3mm) tetapi toleransi ini terutama tergantung pada bagiannya.
Saat mempertimbangkan ketebalan lembaran logam, satu lembaran dengan pukulan (lubang) adalah aturan praktis yang baik. Beberapa fitur seperti countersinks dapat dilakukan tetapi counter bores dan fitur mesin lainnya sulit untuk diproduksi karena memerlukan post machining.
Bend Radius
Rem tikungan lembaran logam digunakan untuk membengkokkan material ke dalam bagian geometri yang diinginkan. Tikungan yang berada pada bidang yang sama perlu dirancang dalam arah yang sama untuk menghindari orientasi ulang bagian, untuk menghemat uang dan waktu. Menjaga radius tikungan tetap konsisten juga akan membuat suku cadang lebih hemat biaya. Bagian yang tebal cenderung menjadi tidak akurat sehingga harus dihindari jika memungkinkan. Tikungan kecil hingga besar.
Saat membengkokkan sepotong lembaran logam, tegangan sisa pada material akan menyebabkan lembaran sedikit terdorong ke belakang setelah operasi pembengkokan. Karena pemulihan elastis ini, perlu untuk menekuk lembaran dalam jumlah yang tepat untuk mencapai radius tikungan dan sudut tikungan yang diinginkan. Jari-jari tikungan akhir akan lebih besar dari yang awalnya terbentuk dan sudut tikungan akhir akan lebih kecil. Rasio sudut tikungan akhir dengan sudut tikungan awal didefinisikan sebagai faktor pegas, KS. Jumlah springback tergantung pada beberapa faktor, termasuk material, operasi bending, dan sudut tikungan awal dan radius tikungan.
Ukuran:
Untuk mencegah bagian dari patah atau mengalami distorsi, pastikan untuk menjaga radius tikungan bagian dalam setidaknya sama dengan ketebalan material
Sudut tikungan:
A +/- 1 derajat toleransi pada semua sudut tikungan umumnya dapat diterima di industri. Panjang flensa harus minimal 4 kali ketebalan material.
Aturan praktis
Disarankan untuk menggunakan jari-jari yang sama di semua tikungan, dan panjang flensa harus setidaknya 4 kali ketebalan material.
Bend Relief
Ketika sebuah tikungan atau sudut dibuat dekat dengan tepi, material dapat robek kecuali jika diberikan bantuan sudut.
Tikungan 1 menunjukkan tear relief.
Tikungan 2 menunjukkan potongan relief persegi panjang menjadi bagian, kedalaman relief harus lebih besar dari jari-jari tikungan. Lebar relief harus setebal bahan atau lebih besar.
Bend relief digunakan di mana tikungan memanjang di tepi. Relief takik ditambahkan untuk mencegah robek. Relief tikungan tidak akan lebih dalam dari ketebalan material ditambah radius tikungan.
Bend Height
Tinggi tikungan lembaran logam harus setidaknya dua kali ketebalan lembaran logam ditambah radius tikungan
H=2t + r
Jika tinggi tekukan terlalu kecil akan mengakibatkan deformasi dan kualitas tekukan yang rendah.
Forming near holes
Ketika sudut dibuat terlalu dekat dengan lubang, lubang bisa berubah bentuk. Lubang 1 menunjukkan lubang yang menjadi berbentuk tetesan air mata karena masalah ini. Untuk menghemat biaya punching atau pengeboran dalam operasi sekunder, rumus berikut dapat digunakan untuk menghitung jarak minimum yang diperlukan:
Untuk slot atau lubang berdiameter <25mm, jarak minimum ke pusat Lubang 2:
D = 2t + r
Sebagai aturan praktis jarak dari bagian luar material ke bagian bawah potongan harus sama dengan panjang sayap minimum seperti yang ditentukan oleh bagan gaya tikungan udara.
D = 2,5t + r
Saat menggunakan punch press, atau pemotongan laser, lubang tidak boleh kurang dari ketebalan material.
Jarak Minimum dari lubang yang diekstrusi ke bagian tepi
kstrusi logam adalah salah satu aplikasi tekanan paling ekstrim dalam pekerjaan tekan dan menghasilkan banyak gesekan dan panas. Jika lubang yang diekstrusi terlalu dekat dengan tepi bagian, dapat menyebabkan deformasi atau robeknya logam. Disarankan bahwa jarak minimum antara lubang yang diekstrusi ke tepi bagian harus setidaknya tiga kali ketebalan lembaran.
Laser Cutting adalah jenis produksi yang menggunakan laser untuk memotong berbagai logam. Laser memiliki sinar energi tinggi yang mudah terbakar melalui bahan. Pemotongan laser dapat digunakan pada bahan seperti logam, aluminium, plastik, kayu, karet, dll. Laser menggunakan pemrograman yang dikendalikan secara numerik (CNC) komputer untuk menentukan bentuk dan posisi potongan. Ketebalan material hingga 20mm dapat dipotong dengan laser. Ada keuntungan dan kerugian dalam menggunakan lasercutting. Laser CO2 lebih tradisional, dan dapat memotong bahan yang lebih tebal tetapi tidak menghasilkan potongan yang akurat seperti laser serat. Laser serat umumnya dapat memotong bahan yang lebih tipis dan memiliki kecepatan potong yang jauh lebih tinggi daripada CO2.
Keuntungan dari pemotongan laser dibandingkan pemotongan secara mekanis mencakup workholding yang lebih baik, kontaminasi benda kerja yang berkurang, presisi yang lebih baik, dan kemungkinan melengkung yang lebih kecil karena zona yang terkena panas kecil. Beberapa kelemahannya adalah bahwa pemotongan laser tidak selalu memotong dengan baik dengan beberapa bahan (misalnya tidak semua aluminium) dan tidak selalu konsisten. Terlepas dari kekurangannya, pemotongan laser sangat efisien dan hemat biaya.
Pembatasan Material
Bahan yang tidak cocok untuk pemotongan laser termasuk bahan cermin atau reflektif, papan Masonite, komposit yang mengandung PVC.
Bahan yang Dapat Diterima
Umumnya bahan-bahan berikut ini cocok untuk pemotongan laser: logam, baja tahan karat, beberapa ketebalan aluminium, kayu dan beberapa plastik.
Pengerasan lokal
Pengerasan lokal terjadi di tepi di mana laser telah dipotong. Pengerasan ini menghasilkan tepi yang tahan lama dan halus tanpa perlu finishing setelah menggunakan pemotong laser
Distorsi
Zona yang terpengaruh panas (HAZ) dihasilkan selama pemotongan laser . Dalam baja karbon, semakin tinggi hardenability, semakin besar HAZ. Distorsi dari pemrosesan laser adalah akibat dari kenaikan suhu material yang tiba-tiba di dekat zona pemotongan. Distorsi juga diciptakan oleh pemadatan cepat dari zona pemotongan. Selain itu, distorsi juga dapat dikaitkan dengan pemadatan cepat bahan yang tersisa di sisi potongan.
Garitan
Selama pemotongan laser, sebagian bahan terbakar saat laser memotong, meninggalkan celah kecil. 'Kesenjangan' ini dikenal sebagai laser garitan dan berkisar antara 0,08 – 0,45 mm tergantung pada jenis bahan, ketebalan, dan faktor kondisional lainnya. Jarak minimum 1-2mm antara bagian harus dibiarkan untuk menghindari pemotongan crossover yang tidak disengaja.
Disarankan juga untuk menjauhkan bagian 2-5mm dari tepi bahan karena beberapa lembar melengkung atau sedikit terlepas dalam ukurannya. Seseorang harus selalu memotong bagian dalam batas ukuran lembaran dan tidak menggunakan tepi lembaran sebagai batas.