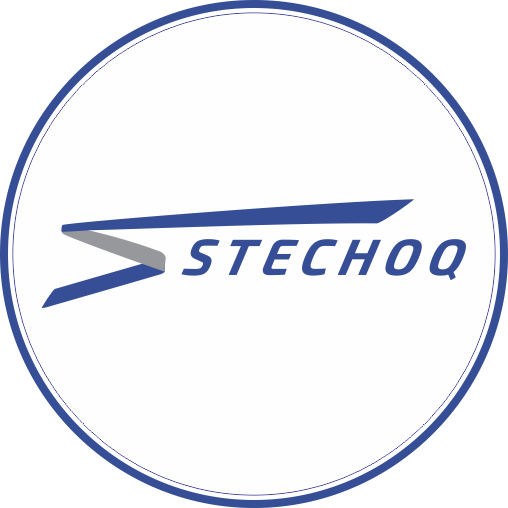
Procurement management adalah kegiatan yang dilakukan oleh perusahaan untuk menyediakan input, berupa barang maupun jasa, yang dibutuhkan dalam kegiatan produksi maupun kegiatan lain didalam perusahaan.
Sistem pengadaan harus dibuat ringkas dan jelas. Maka dari itu, dibutuhkan tim yang memiliki tugas untuk memastikan semua kebutuhan perusahaan bisa terpenuhi. Bila tidak diatur, maka akan kesulitan bagi perusahaan mendata mana barang yang sudah dibeli ataupun belum.
Bila tidak diatur dalam sebuah sistem maka proses pengadaan juga tidak bisa dibuat dengan ringkas. Dengan sistem manajemen yang jelas, maka pengadaan barang juga bisa dilakukan dengan mudah. Misalnya jadi lebih jelas mengenai timeline dari sebuah pengadaan barang. Perusahaan bisa melihat dengan jelas kapan akan dilakukan tender dan kapan barang sudah bisa dipakai.
Bahkan di zaman yang punya perkembangan teknologi cukup pesat, sistem procurement dilakukan secara elektronik atau biasa disebut dengan e-procurement. Dengan sistem ini perusahaan jauh lebih bisa menekan biaya operasional. Perusahaan tak perlu lagi menghabiskan biaya untuk konsumsi rapat hingga pembelian kertas.
Perusahaan hanya tinggal menunjuk satu orang sebagai penanggung jawab untuk setiap barang dan membekalinya dengan perangkat digital. Cara-cara inilah yang menjadi cara perusahaan supaya bisa menekan biaya operasional.
Semua pengadaan barang pastinya akan direkap di dalam sebuah sistem. Dengan demikian, kegiatan pengadaan akan jauh lebih transparan. Semua bagian bisa mengecek harga yang ditawarkan oleh pihak luar atau vendor. Kecurangan seperti melakukan mark up harga tidak akan terjadi karena bisa dicek melalui sistem.
Proses ini juga membantu pengawasan terhadap procurement management. Apalagi semua proses penunjukkan hingga pengadaan akan direkam oleh sistem dan dijadikan arsip. Data supplier maupun vendor juga bisa direkap dan bisa diakses dengan mudah. Langkah ini bisa menjadi cara untuk mencegah korupsi, kolusi dan nepotisme. Perusahaan juga bisa menjaga supaya semua pembayaran dilakukan tepat waktu.
Semua sistem yang dibuat akan memudahkan semua proses penunjukkan hingga pengadaan. Misalnya bila dilakukan dengan sistem tender, maka dengan mudah perusahaan mengecek dan membandingkan penawaran. Ini tentu akan jauh lebih efisien bila tidak memakai sistem karena harus mengecek kertas penawaran satu per satu.
Perusahan juga bisa melakukan filter. Misalnya mencari vendor atau supplier yang memberikan penawaran terendah atau yang sesuai budget. Dengan demikian, tim procurement tidak perlu lagi membaca semua penawaran yang memang tidak sesuai budget. Pada saat penunjukkan supplier juga lebih mudah.
Dengan sistem, tim akan bisa melihat detail dari penawaran vendor. Misalnya mulai dari jangka waktu pengiriman dan waktu pembayaran. Data-data ini pun bisa disimpan dalam sistem. Bila sewaktu saat dibutuhkan maka tak perlu lagi repot mencari data vendor maupun supplier.
Dengan bantuan procurement management, semua proses pengadaan barang bisa dilakukan dengan cepat dan mudah. Semua tahap mulai perencanaan hingga pembayaran bisa dilakukan dengan cepat. Dengan demikian tim procurement tak perlu lagi membutuhkan waktu lama saat mengerjakan satu pengadaan barang.
Proses yang lebih cepat juga membantu perusahaan lebih produktif. Hal ini juga bisa mempengaruhi dari biaya produksi yang dikeluarkan oleh perusahaan. Apalagi sistemnya juga mudah dipakai dan bisa menyimpan banyak arsip. Proses procurement bisa dilakukan tanpa perlu memulainya dari awal.
Kesalahan manusia sangat mungkin terjadi dalam semua proses di perusahaan. Dengan sistem procurement management, semua karyawan bisa melihat dengan jelas tahapan-tahapan yang harus dilewati untuk melakukan pengadaan barang. Dengan adanya panduan ini, tentunya tim yang bertanggung jawab tidak akan melewatkan tahapan tersebut.
Karyawan juga dengan mudah mengoreksi tahapan yang dilakukan. Pekerjaan juga bisa dilakukan lebih cepat dan tanpa perlu khawatir ada kesalahan manusia. Sistem juga memungkinkan tahapan transaksi sebelumnya dibuka kembali. Dengan demikian seseorang bisa melakukan perbandingan dengan pengadaan sebelumnya. Hal ini juga bisa mengurangi risiko kesalahan manusia.
Salah satu masalah yang kerap muncul karena pengadaan barang adalah kecurangan antar vendor atau supplier. Istilah ‘orang dalam’ kerap membuat sistem pengadaan barang jadi kurang sehat. Dengan adanya sistem yang jelas, maka semua peserta tender atau lelang bisa mendapatkan keadilan. Semua vendor dan supplier yang memenuhi syarat pastinya bisa mengikuti tahapan pengadaan barang. Perusahaan juga jauh lebih diuntungkan karena bisa menemukan barang atau jasa yang mungkin memang lebih sesuai dan berkualitas.
Proses pengadaan barang akan erat kaitannya dengan laporan keuangan. Dengan sistem procurement management yang jelas, maka akuntan bisa dengan lebih mudah menyusun laporan keuangan yang lebih transparan dan juga lebih kredibel. Risiko terjadinya fraud akan lebih diminimalisir.
Apalagi data atau arsip dibuat dengan jelas dan rapi. Dengan demikian tim keuangan perusahaan akan dengan mudah melakukan pengecekan. Proses pembayaran juga hanya dilakukan pada segala sesuatu yang benar-benar terjadi. Tidak akan terjadi sebuah pembayaran terhadap pesanan barang fiktif.
Ternyata memang manfaat sistem procurement management sangat menguntungkan perusahaan. Tak hanya bisa mendapatkan barang atau jasa yang terbaik. Perusahaan juga bisa mencegah hal-hal yang merugikan terutama dari segi keuangan. Proses pengadaan barang juga terjadi lebih adil dan transparan.
Menurut Netsuite, procurement dikategorikan dalam beberapa cara tergantung pada langsung tidaknya suatu pengadaan dilakukan dan bagaimana perusahaan akan menggunakan barang atau jasa yang dibeli. Adapun jenis-jenis procurement itu antara lain adalah sebagai berikut:
Procurement | Purchasing |
---|---|
Sebuah proses panjang dari analisis dan identifikasi kebutuhan barang dan jasa oleh manajer pengadaan. | Hanya bagian dari keseluruhan proses procurement yang mencakup proses pembelian secara khusus yang dilakukan dari pembuatan pesanan hingga pembuatan slip pembelian. |
Terdapat perencanaan vendor atau supplier sebelum dilakukan kontrak dilakukan. | Langsung melakukan transaksi kepada vendor atau supplier yang telah ditentukan. |
Melakukan riset terhadap sumber atau supplier sebelum menentukan kontrak terhadap supplier atau vendor. | Melakukan tanya jawab seputar barang yang dipesan sebelum pemrosesan pembayaran. |
Membangun hubungan atau relasi dengan supplier atau vendor. | Proses relasi berakhir saat proses pembayaran pada supplier. |
Evaluasi terhadap layanan supplier atau vendor secara umum sebelum melakukan kontrak. | Evaluasi dilakukan terhadap barang yang diterima. |
Berikut ini adalah 7 langkah atau tahapan yang ada dalam proses procurement menurut Tradeready:
Proses procurement dimulai dengan menganalisis kinerja perusahaan saat ini dan kemudian mengidentifikasi kebutuhan serta target perusahaan sebelum mengembangkan strategi pengadaan. Hal ini dilakukan dengan melibatkan beberapa jenis data dari setiap divisi atau departemen dalam perusahaan.
Pengumpulan data dalam proses awal procurement dilakukan untuk dapat memproyeksikan kinerja perusahaan ke depan beserta biaya yang akan dikeluarkan untuk peningkatan kinerja itu melalui pengadaan. Proses analisis procurement ini dilakukan oleh sebuah tim atau bagian khusus yang dipimpin oleh manajer pengadaan untuk dapat melihat dan menguraikan potensi efisiensi dan penghematan biaya perusahaan dengan melakukan pengadaan eksternal.
Setelah melakukan analisis dan identifikasi terhadap kebutuhan perusahaan, tim pengadaan strategis atau manajer pengadaan lantas melanjutkan proses procurement dengan identifikasi vendor atau supplier potensial yang ada di pasaran. Identifikasi ini dilakukan dengan melihat relevansi dan korelasi kebutuhan perusahaan dengan ketersediaannya di tiap vendor atau supplier.
Daftar vendor dan supplier ini dapat dilakukan dengan melihat kinerja mereka di beberapa perusahaan lain sebelumnya. Baik vendor maupun supplier adalah calon mitra perusahaan yang tentunya berpotensi akan bekerja sama dalam jangka waktu tertentu. Untuk itu diperlukan sebuah proses perbandingan antar vendor atau supplier terkait harga, penawaran, kualitas, hingga pengiriman barang sehingga jarak tempuh yang ingin dicapai tidak terlalu jauh dan memakan biaya.
Langkah yang dilakukan setelah melakukan seleksi atau penilaian terhadap para penyedia barang dan jasa adalah menentukan pilihan. Pilihan terhadap penyedia barang dan jasa ini tentunya dipertimbangkan secara efisiensi dan sisi ekonomis. Umumnya terdapat beberapa penyedia untuk tiap-tiap kebutuhan pengadaan yang berbeda dan hal ini berarti diperlukan perhatian terhadap reputasi dari tiap vendor atau supplier tersebut.
Beberapa cara untuk mempermudah tahapan ini salah satunya adalah menggunakan agen di mana ia bertindak untuk melakukan pengelolaan terhadap para vendor atau supplier. Hal ini dapat dilakukan untuk mengurangi permasalahan atau potensi gangguan pasokan dari satu vendor atau yang lainnya. Tentu saja, diperlukan biaya lebih untuk cara ini.
Sebelum melakukan kesepakatan pembelian, perusahaan melalui manajer pengadaan perlu merumuskan strategi terhadap para sumber pemasok barang dan jasa dalam procurement. Strategi itu antara lain adalah sebagai berikut:
Setelah merancang strategi untuk tiap-tiap pemasok terpilih maka langkah selanjutnya adalah pembelian atau purchasing. Proses pembelian dalam procurement memiliki tanggung jawab untuk memastikan beberapa hal berikut ini:
Umumnya, proses pembelian barang atau jasa dalam proses procurement mendahulukan datangnya pesanan kepada perusahaan pemesan. Dalam hal ini perusahaan pemesan dapat melakukan pengawasan dalam penerimaan barang jasa yang terpesan sebelum melakukan pembayaran atau pelunasan. Jika ditemukan beberapa hal yang tidak sesuai kontrak maka perusahaan berhak melakukan negosiasi ulang dengan vendor atau supplier terkait.
Setelah proses pengawasan pengiriman dan penerimaan barang atau jasa terpesan, maka perusahaan pemesan berkewajiban untuk melakukan pembayaran penuh atau pelunasan. Hal ini dilakukan sesuai kesepakatan kontrak dan negosiasi ulang jika terdapat beberapa hal perubahan setelah proses penerimaan. Pembayaran ini juga bergantung pada kontrak atau strategi apa yang diambil perusahaan terhadap para vendor atau pemasok.
Reorder point adalah sebuah titik di mana sebuah barang yang ada di gudang harus ditambah persediaannya sebelum kehabisan. Yang sering jadi pertanyaan adalah; kapankah waktu yang tepat untuk memesan barang tersebut?
Setidaknya ada tiga hal yang dijadikan sebagai parameter khusus dalam menghitung reorder point, yaitu lead time demand, safety stock, dan reorder point itu sendiri.
Lead time adalah suatu jeda waktu yang terjadi antara waktu pemesanan hingga barang tersebut masuk ke gudang Anda. Lead time ini berkisar antara beberapa minggu sampai beberapa bulan lamanya.
Tingkat waktu lead time akan sangat tergantung pada kesulitan barang yang dipesan, jumlah, hingga jarak tempuh pengiriman barang. Bila pemasok berada di luar negeri dan barang yang dipesan berjumlah ribuan, maka bersiaplah untuk menerima barang tersebut hingga beberapa bulan lamanya.
Agar lebih mudah dimengerti, mari kita menggunakan contoh kasus ini.
Anggaplah Anda adalah seorang penjual tas kulit impor dari China. Katakanlah pemasok Anda tidak pernah mengalami masalah terkait stok barang dan sangat siap untuk mengirimkan barang kapan saja. Tapi, untuk pengambilan dan juga packing barang dibutuhkan waktu dua hari.
Setelah itu, pesanan Anda akan dimasukkan dalam truk besar dan memerlukan waktu perjalanan selama lima hari agar bisa mencapai pelabuhan. Dari pelabuhan sendiri, pesanan Anda akan mengarungi Samudra Pasifik dari China ke Indonesia yang memerlukan waktu paling cepat 30 hari.
Sesampainya di Indonesia, barang tersebut pun harus diperiksa lagi oleh bea cukai yang memerlukan waktu selama satu minggu. Kemudian, barang tersebut baru bisa Anda terima di toko melalui jalur darat selama 5 hari.
Berdasarkan contoh kasus diatas, maka total lead time Anda adalah lead time = 2 + 5 + 30 + 7 + 5 = 49 HARI
Data diatas menjelaskan bahwa Anda harus mempunyai stok tas kulit untuk bisa dijual sampai pengiriman yang selanjutnya tiba. Anda juga bisa melakukan antisipasi demand dari pelanggan pada barang tersebut. Hindari kehabisan persediaan sebelum barang yang Anda pesan dari pemasok tiba.
namun, masih ada cara lain untuk menghitung demand ini, yaitu dengan mengalikan angka lead time dengan nilai rata-rata penjualan harian Anda. katakanlah Anda bisa menjual 10 tas kulit perhari, maka lead time usaha Anda adalah Lead Time Demand = Lead Time X Rata-Rata Penjualan Per-Hari, jadi 49 X 10 = 490.
Itu artinya, Anda harus bisa menyediakan 490 tas kulit guna mengantisipasi pesanan pelanggan Anda hingga barang yang dikirim oleh pemasok Anda tiba. Walaupun memang terdengar mudah, namun perhitungan seperti ini hanya bisa dilakukan bila ada hal lain yang diluar dugaan tidak terjadi.
Mudah? Nanti dulu! Perhitungan ini hanya bisa berjalan, jika tak ada hal-hal yang di luar dugaan terjadi.Di dalam manajemen persediaan, Anda harus bisa melakukan antisipasi pada setiap kemungkinan terburuk yang bisa terjadi dan berpeluang mengganggu persediaan barang Anda.
Sebagai contoh ada artis yang tiba-tiba tertarik dan menggunakan tas kulit Anda, lalu Anda mengalami kebanjiran pesanan. Atau ada musibah lain seperti angin topan yang bertiup kencang dari Samudra Pasifik yang secara otomatis mengganggu pengiriman barang.
Berbagai faktor tak terduga ini harus bisa Anda perhitungkan sebelumnya dengan menerapkan safety stock, atau yang lebih dikenal dengan persediaan tambahan. Namun masalahnya, berapa banyakkah jumlah persediaan yang harus Anda persiapkan. Untuk mengetahuinya, Anda bisa menggunakan rumus berikut:
Safety Stock = (Penjualan Harian Tertinggi X Lead Time Terlama) – (Rata-Rata Penjualan Harian X Rata-Rata Lead Time)
Untuk lebih paham, mari kita tetap gunakan asumsi bisnis tas kulit di atas. Dari data sebelumnya, kita sudah mengetahui bersama bahwa Anda berhasil menjual tas kulit sebanyak rata-rata 10 unit per hari, tapi di hari sabtu dan minggu penjualan tas kulit Anda meningkat hingga 20 unit per hari.
Untuk lead time, umumnya pengiriman tas kulit dari Cina memerlukan waktu 49 hari. Tapi karena truk pengantar barang pesanan barang Anda ke pelabuhan China mengalami kendala mesin truk dan mogok, maka pengiriman menjadi lebih lama sampai 54 hari.
Lantas, jika kita menggunakan rumus di atas, maka safety stock Anda adalah (20 X 54) – (49 X 10) = 590
Dengan adanya dua hasil perhitungan ini, maka kita bisa memperoleh nilai reorder point dengan cara menjumlahkan lead time demand dan juga safety stock. Hasil perhitungannya adalah sebagai berikut:
490 (Lead Time Demand) + 590 (Safety Stock) = 1080 (Reorder Point)
Hal tersebut menunjukkan bahwa Anda harus membuat pesanan pada pihak pemasok bila sisa tas kulit yang ada di gudang berjumlah total 1080 unit.
Dengan begitu, Anda bisa memastikan persediaan tas kulit Anda cukup hingga pesanan berikutnya telah tiba. Namun jika terjadi musibah atau hal lainnya yang di luar perkiraan, Anda masih mempunyai persediaan yang cukup untuk bisa melayani pelanggan tanpa perlu khawatir.
Material Requirement Planning atau MRP adalah, sistem yang bermanfaat untuk menghitung rincian jumlah bahan baku, bahan mentah atau komponen, yang dibutuhkan untuk memproduksi sebuah barang pada sebuah perusahaan.
Biasanya sistem MRP ini digunakan oleh perusahaan manufaktur yang memang banyak memproduksi barang dan permintaan.
Intinya, sistem MRP adalah sistem yang biasa digunakan untuk menjawab tiga pertanyaan penting para divisi produksi. Tiga pertanyaan itu adalah:
Tidak hanya sekadar sistem yang memberitahu pihak tim produksi, sistem MRP tentunya membutuhkan bantuan alat perhitungan berupa software komputer.
Nantinya software ini bisa bekerja dengan cara update informasi terkait produksi, secara otomatis di perusahaan manufaktur, seperti software manufaktur.
Sehingga, dengan adanya software ini, perusahaan bisa menggunakannya untuk mengestimasi bahan baku dengan jumlah dan rincian yang tepat yang dibutuhkan saat produksi serta menjadwalkan pengirimannya.
Nah, buat kamu yang masih bingung dengan cara kerja sistem MRP, yuk simak di sini!
Jadi sistem MRP ini akan mengambil informasi dari Bill of Materials (mulai dari daftar semua bahan baku yang digunakan perusahaan, subassemblies, dan komponen lainnya yang dibutuhkan untuk memproduksi sebuah barang lengkap dengan jumlahnya).
Tidak hanya itu, MRP juga memanfaatkan data inventori dan jadwal produksi utama yang berguna untuk menghitung jumlah bahan baku yang dibutuhkan serta kapan bahan baku tersebut akan diperlukan pada saat produksi berjalan.
Sangat membantu tim produksi, metode ini bisa dibilang sangat efektif untuk berbagai jenis perusahaan manufaktur. Sebut saja seperti perusahan manufaktur diskrit (mulai dari pabrik mobil, perkakas atau sejenisnya), hingga perusahaan manufaktur proses (seperti pabrik makanan atau minuman, pabrik kimia dan sejenisnya).
Maka tak heran jika sistem MRP adalah sistem penting yang metodenya sudah diadaptasi oleh banyak perusahaan manufaktur tidak hanya di Indonesia tapi juga di berbagai belahan dunia.
Pada awalnya, material requirement planning menggunakan komputer mainframe untuk mengelola informasi dari bill of materials untuk produk tertentu dan diubah menjadi rencana pembelian dan rencana produksi.
Beberapa tahun kemudian, MRP menyertakan fitur feedback yang memudahkan manajer produksi untuk melakukan perubahan atau update langsung ke sistem jika diperlukan.
Seiring tahun berjalan, sistem material requirement planning terus berkembang dan kini sudah bisa diintegrasikan dengan marketing, keuangan, sampai dengan human resources dalam pembuatan rencana produksi. Karena kompleksitasnya, MRP di tahap ini banyak disebut oleh berbagai pihak sebagai MRP II.
Bukan tanpa alasan, seperti perusahaan manufaktur menggunakan sistem karena pasti memiliki tujuan dalam penerapan MRP (Material Requirement Planning), berikut tujuannya:
Jika dilihat dari tujuan utamanya, MRP adalah sistem untuk menentukan jumlah komponen/bahan baku yang dibutuhkan dan kapan komponen/bahan baku tersebut dibutuhkan sesuai Jadwal Produksi Induk (Master Produksi Schedule).
Nah, dengan adanya sistem ini juga akan membuat perusahaan manufaktur yang bersangkutan hanya perlu membeli material (komponen/bahan baku) tersebut pada saat dibutuhkan saja (mengestimasi).
Sehingga, cara tersebut bisa digunakan untuk menghindari kelebihan persedian material.
Tujuan yang selanjutnya dari MRP adalah bisa membantu mengidentifikasikan jumlah dan waktu material yang dibutuhkan sehingga pihak purchasing bisa melakukan tindakan yang tepat khususnya untuk memenuhi batas waktu yang ditetapkan.
Maka dari itu, penggunaan sistem MRP juga dapat membantu untuk menghindari keterlambatan produksi yang umumnya disebabkan oleh masalah kekurangan material.
Perusahaan yang menggunakan sistem MRP, maka mereka bisa menginformasikan dengan cepat dari pihak produksi ke bagian pengiriman barang sehingga bisa mengestimasi kemungkinan waktu pengirimannya.
Tujuan berikutnya dari MRP adalah bisa membantu setiap unit kerja agar selalu terkoordinasi dengan baik. Dengan begitu, perusahaan dapat meningkatkan efisiensi kegiatan operasionalnya ketimbang perusahaan yang tidak menerapkan sistem MRP.
Seperti sistem pada umumnya, tentu terdapat INPUT dan OUTPUT. Nah, Input dan Output yang ada pada sistem MRP adalah:
Input:
– Master Production Schedule (MPS)
– Jadwal Produksi Induk
– Inventory Status File (Berkas Status Persediaan)
– Bill of Materials (BOM) atau Daftar Material
Output:
– Order Release Requirement (Kebutuhan material yang akan dipesan)
– Order Scheduling (Jadwal pemesanan material)
– Planned Order (rencana pesan di masa yang akan datang). Agar lebih mudah dipahami, intip bagan dari 3 INPUT penting yang ada pada Material Requirement Planning (MRP) atau Perencanaan Kebutuhan Material.
Sebenarnya, dalam proses menganalisis MRP bisa dilakukan dengan dua cara, yakni manual maupun dengan bantuan suatu program aplikasi (software).
Berikut empat langkah dasar prosedur sistem MRP yang bisa kamu terapkan:
Pertama ada proses netting, yang merupakan proses perhitungan untuk menetapkan jumlah kebutuhan bersih.
Di mana nilainya adalah selisih antara kebutuhan kotor dengan keadaan persediaan (yang ada dalam persediaan dan yang sedang dipesan atau tinggal menunggu jadwal penerimaan).
Proses yang kedua adalah lotting atau lot sizing, yang merupakan teknik guna menentukan besarnya kuantitas pesanan, yang optimal untuk setiap item bahan atau material.
Di sini, proses lotting sangat berperan penting dalam perencanaan kebutuhan bahan, terutama pada perusahaan yang memiliki keterbatasan fasilitas atau ruang.
Selanjutnya, ukuran lot dikaitkan dengan besarnya ongkos-ongkos persediaan, sebut saja seperti ongkos pengadaan barang (ongkos setup), ongkos simpan, biaya modal, dan harga barang itu sendiri.
Yang ketiga ada proses offsetting, yang berguna untuk menentukan waktu dilakukannya kegiatan pemesanan sehingga upaya untuk memenuhi tingkat kebutuhan bersih bisa segera tercapai.
Proses yang terakhir adalah explosion yang merupakan sebuah perhitungan kebutuhan tiap item, di mana perhitungannya menilai tingkat yang lebih rendah dari struktur produk yang tersedia.
Perhitungan ini juga didasarkan atas rencana pemesanan yang sebelumnya telah disusun pada proses offsetting.
Unsur manajemen adalah sarana bagi manajemen untuk melakukan kegiatan. Manajemen tidak akan bisa melakukan hal apapun jika tidak memiliki unsur unsur manajemen.Setidaknya. Ada 6 unsur yang hukumnya wajib dimiliki oleh manajemen perusahaan. 6 unsur itu dikenal dengan 6 M
Unsur manajemen yang paling penting dalam mencapai tujuan perusahaan adalah sumber daya manusia. Dilansir dari Encyclopedia Britannica, man mengacu pada unsur manusia dalam sistem operasi, sehingga manajemen manusia adalah salah satu tanggung jawab yang penting. Manusia memiliki keterampilan hingga sifat yang berbeda-beda. Sehingga manajemen manusia dibutuhkan untuk mendapatkan hasil kerja yang maksimal, lingkungan kerja yang sehat dan kondusif, serta ide-ide inovatif yang dapat memajukan usaha.
Man (manusia) dalam hal ini adalah tenaga kerja. Bisa jadi pelaksana teknis, operator mesin, sampai dengan pimpinan yang bertugas pada proses produksi. Bahkan tidak menutup kemungkinan faktor Man disini disebabkan oleh pimpinan tertinggi dalam struktur organisasi, yakni manajer.
Method atau metode adalah unsur manajemen yang diperlukan untuk mengatur prosedur maupun standar operasional berjalannya suatu kegiatan. Metode kegiatan ataupun usaha harus dibuat sebaik dan seefektif mungkin untuk menghasilkan kerja yang bagus. Misalnya jam kerja harus diimbangi dengan waktu untuk makan dan beristirahat sehingga pegawai dalam kondisi yang fokus dan tidak kelelahan. Pada produksi suatu barang juga metode produksi harus efektif di mana produksi memiliki alur dan prosedur yang sistematik. Penambahan kontrol kualitas juga diperlukan untuk mendapatkan metode terbaik yang dapat diterapkan pada suatu kegiatan maupun usaha.
Machine atau mesin adalah unsur manajemen yang berupa barang. Mesin dapat berupa peralatan logistik maupun teknologi yang dibutuhkan dalam suatu kegiatan. Pembelian serta penggunaan mesin harus diatur supaya efektif artinya mendapatkan alat yang bagus dengan harga yang ekonomis, namun tetap memiliki performa yang baik untuk produksi.
Material atau bahan adalah unsur manajemen berupa bahan baku yang dibutuhkan dalam suatu kegiatan. Pemilihan bahan baku hingga penggunaanya harus dilakukan sebaik dan seefektif mungkin sehingga tidak ada bahan yang terbuang sia-sia. Pemilihan bahan juga harus disesuaikan dengan kebutuhan usaha juga anggaran dana sehingga bisa mendapat bahan yang berkualitas namun tetap ekonomis.
Money atau uang merupakan unsur yang mendasari semua kegiatan. Uang jarus dikelola dengan bijak dan efisien. Penganggaran serta penggunaan uang harus diatur dengan cermat, bijaksana, efisien, dan dapat dipertanggung jawabkan.
Market atau pasar adalah unsur selanjutnya dari manajemen terutama untuk bisnis atau usaha. Dilansir dari Economidiscussions, unsur pasar adalah perencanaan, pengorganisasian, pengendalian, penerapan program, kebijakan, strategi, dan teknik pemasaran untuk menciptakan permintaan akan penawaran produk atau jasa.
Material Requirement Planning masuk kedalam resource management, metode MRP berguna untuk mengatur kebutuhan material yang akan diproduksi sesuai dengan schedule yang sudah dibuat. Berikut cara membuat MRP
Di dalam membuat material requirement planning atau perencanaan kebutuhan material di perusahaan, kita harus memahami tahapan dalam membuat material requirement planning. 3 hal yang dibutuhkan tersebut adalah
1.Pohon produksi atau Susunan Bill Of Material
2.Master Production Schedule (Jadwal Produksi Induk)
3.Material requirement planning untuk setiap komponen.
Contoh Soal Penerapan Material Requierement Planning (MRP) di Perusahaan
Sebuah perusahaan Pulpen ingin merencanakan kebutuhan bahan untuk setiap komponen pulpen. Perusahaan Pulpen menugaskan kepada manager PPIC untuk membuat jadwal kebutuhan bahan yang diperlukan untuk membuat 240 pulpen perbulan. Maka manager PPIC melakukan kegiatan sebagai berikut
1. Menyusun Bill of material pulpen
Manager PPIC terlebih dahulu membuat struktur bahan yang digunakan untuk membuat pulpen, sebagaimana tertulis dalam gambar dibawah ini :
![]() |
Gambar Bill Of material Pulpen |
Dengan melihat struktur pohon produksi atau bill of material penyusun pulpen diatas, maka manager ppic bisa memahami bahan apa saja yang harus diproduksi atau dipesan untuk membuat sebuah pulpen.
Manager PPIC berkoordinasi dengan manager gudang (warehouse) tentang produksi pulpen yang sudah dibuat di buat beberapa bulan yang lalu, Manager PPIC mendapat informasi bahwa bullpen yang sudah ada sebanyak 80 pcs, sedangkan badan bullpen, tutup bullpen dan tinta pulpen sudah habis atau nol. Persediaan tersebut ditulis dalam kolom tabel (On Hand). Kemudian manager ppic berkoordinasi dengan manajer produksi tentang jumlah pulpen, badan pulpen, tutup pulpen dan tinta yang masih dalam proses (on Order) masing-masing sebesar Pulpen=80 pcs, Badan Pulpen= 100 pcs, Tutup Pulpen 100 pcs, dan Tinta = 80 pcs. Dengan tanggal waktu terakhir penyelesaian (Due Date) adalah tanggal 25 Maret 2021. Dan setiap komponen tersebut mempunyai waktu lead time (waktu tunggu) 1 minggu. Kemudian manager PPIC membuat tabel bill of material Pulpen, supaya mudah dalam membuat perencanaan material produksi.
![]() |
Tabel Struktur bill of material perusahaan |
Singkat cerita setelah berkonsultasi dengan direktur perusahaan dan bagian pemasaran, akhirnya diperoleh jadwal produksi induk sebagai berikut
![]() |
Tabel Jadwal Produksi Induk Perusahaan |
3. Material Requirement Planning
Berikut adalah tahapan dalam membuat material requirement planning, dimana penulis menggunakan metode lot for lot, lot for lot adalah metode yang tidak menyediakan penyimpanan material (bahan baku) di tempat produksi. Sehingga biaya penyimpanan nol. langkah pertama saudara buat tabel MRP sebagaimana tertulis di bawah ini, sesuaikan dengan nama kode dengan kode bill of material yang ada, di bawah ini adalah tabel material requirement planning untuk bill of material Pulpen
![]() |
Tabel MRP kosong |
1) Mari lihat ke tabel 1.3 dibawah tertera kode BU, lead time 1 minggu dan jumlah 1 , hal tersebut merujuk kepada bill of material tabel 1.0. kemudian tulis nilai 60 dari minggu pertama sampai minggu ke delapan sesuai dengan dari jadwal master production schedule yang ada. sebagaimana gambar di bawah ini :
![]() |
Tabel Master Production Schedule |
2) kolom ke 1 (pertama) schedule receipt adalah 80, diperoleh dari tabel 1.0 bill of material . kita letakkan di kolom Schedule receipt minggu pertama sebesar 80.
3) nilai on hand diperoleh dari tabel 1.0 tertulis bahwa on hand (persediaan di gudang) adalah 80, kita masukkan dalam kolom on hand 80. Kolom minggu 1 (pertama) bernilai 100 diperoleh dari penjumlahan kolom on hand minggu ke 0 + Schedule receipt minggu ke 1 – gross requirement minggu ke 1
80 +80-60 = 100.
Kolom on hand minggu ke 2 diperoleh dari kolom on hand minggu ke 1 + Schedule receipt minggu ke 2 – gross requirement minggu ke 2
100 + 0 – 60 = 40
Kolom on hand minggu ke 3 Kolom on hand minggu ke 3 diperoleh dari kolom on hand minggu ke 2 + Schedule receipt minggu ke 3 – gross requirement minggu ke 3
40 + 0 – 60 = -20
Karena nilai kolom on hand menunjukkan nilai negatif maka hal tersebut tidak sesuai dengan material requirement planning, sehingga kita kosongkan. sehingga tertulis seperti tabel 1.4 di bawah ini.
![]() |
Tabel On hand kode BU |
4) Kita lanjutkan ke kolom di bawahnya, yakni kolom net requirement. Kolom minggu ke 3 net requirement diperoleh dengan mengurangi kolom gross requirement minggu ke 3 dengan kolom on hand minggu ke 2
60 – 40 = 20
Kolom minggu ke 4 net requirement diperoleh dengan mengurangi kolom gross requirement minggu ke 4 dengan kolom on hand minggu ke 3
60 – 0 = 60
Kolom minggu ke 5,6,7 dan 8 net requirement diperoleh dengan cara yang sama seperti kolom minggu ke 4, sehingga nilainya sama 60 semua.
![]() |
Tabel Net Requirement kode BU |
5) Kolom planned order receipt diisi sesuai dengan net requirement yang ada, karena kita menggunakan metode lot for lot, lot for lot adalah metode yang meniadakan biaya simpan atau biaya simpan sama dengan 0, maka kolom planned order receipt kita sesuaikan dengan kolom net requirement, dengan menulis ulang di kolom net requirement dari minggu ke 3 sampai ke 8
![]() |
Tabel Planed order Receipt kode BU |
![]() |
Tabel Planned Order Release kode BU |
Tabel MRP Kode B untuk badan Pulpen
Mari lihat ke tabel 1.8, dibawah tertera kode B, lead time 1 minggu dan jumlah 1, hal tersebut merujuk kepada bill of material tabel 1.0. nilai dari minggu kedua sampai minggu ke 8 diperloh dari jadwal master planned order release tabel mrp level 0. sebagaimana tertulis dalam gambar dibawah
![]() |
Tabel Master Production Schedule |
1) kolom 1 schedule receipt adalah 100, diperoleh dari tabel 1.0 bill of material. kita letakkan di kolom Schedule Receipt minggu kedua sebesar 100.
![]() |
Tabel Gross Requirement kode B |
2) nilai on hand diperoleh dari tabel 1.0 tertulis bahwa on hand (persediaan di gudang) adalah 0, kita masukkan dalam kolom on hand minggu pertama. Kolom minggu ke 2 (kedua) bernilai 80 diperoleh dari penjumlahan kolom on hand minggu ke 1 + Schedule receipt minggu ke 2 – gross requirement minggu ke 2
0 + 100 - 20 = 80.
Kolom on hand minggu ke 3 diperoleh dari kolom on hand minggu ke 2 + Schedule receipt minggu ke 3 – gross requirement minggu ke 3
80 + 0 – 60 = 20
Kolom on hand minggu ke 4 Kolom on hand minggu ke 4 diperoleh dari kolom on hand minggu ke 3 + Schedule receipt minggu ke 4 – gross requirement minggu ke 4
20 + 0 – 60 = -20
Karena nilai kolom on hand menunjukkan nilai negatif maka hal tersebut tidak sesuai dengan material requirement planning, sehingga kita kosongkan.
![]() |
Tabel On Hand kode B |
3) Kita lanjutkan ke kolom di bawahnya, yakni kolom net requirement. Kolom minggu ke 4 net requirement diperoleh dengan mengurangi kolom gross requirement minggu ke 4 dengan kolom on hand minggu ke 3
60 – 20 = 40
Kolom minggu ke 5 net requirement diperoleh dengan mengurangi kolom gross requirement minggu ke 5 dengan kolom on hand minggu ke 4
60 – 0 = 60
Kolom minggu ke 6 dan 7 net requirement diperoleh dengan cara yang sama seperti kolom minggu ke 5, sehingga nilainya sama 60 semua.
![]() |
Tabel Not Requirement kode B |
4) Kolom planned order receipt diisi sesuai dengan net requirement yang ada, karena kita menggunakan metode lot for lot,lot for lot adalah metode yang meniadakan biaya simpan atau biaya simpan sama dengan 0, maka kolom planned order receipt kita sesuaikan dengan kolom net requirement, dengan menulis ulang di kolom net requirement dari minggu ke 4 sampai minggu ke 7
![]() |
Tabel Planned Order Receipt kode B |
5) Kolom planned order release, ditulis sesuai dengan permintaan yang ada, dimana lead time 1 minggu, Maka kolom planned order receipts kita majukan selama 1 minggu. Sehingga hasilnya sesuainya dengan kolom di bawah ini
![]() |
Tabel Planned Order Release kode B |
Tabel MRP kode T
Mari lihat ke tabel, dibawah tertera kode T, yakni tutup Pulpen, kode T berada pada level yang sama dengan kode badan Pulpen, sehingga perhitungannya sama dengan kode B untuk badan Pulpen, karena schedule receipt untuk tutup Pulpen juga sama dengan badan Pulpen maka hasil tabel MRP sama dengan tabel mrp badan bullpen sebagaimana tertulis di bawah ini
![]() |
Tabel Master Production Schedule kode T |
Tabel MRP kode I
Mari lihat ke tabel, dibawah tertera kode I, lead time 1 minggu dan jumlah 1, hal tersebut merujuk kepada bill of material tabel 1.0, karena tinta pada pohon produksi (susunan bill of material) terletak di bawah badan Pulpen, yakni level 2 maka gross requirement tinta mengikuti kolom planned order release dari badan bulpen.
![]() |
Tabel Master Production Schedule kode I |
1) kolom 1 schedule receipt adalah 80, diperoleh dari tabel 1.0 bill of material. kita letakkan di kolom minggu ketiga sebesar 80.
![]() |
Tabel Schedule Receipt kode I |
2) nilai on hand diperoleh dari tabel 1.0 tertulis bahwa on hand (persediaan di gudang) adalah 0, kita masukkan dalam kolom on hand 0. Kolom minggu ke 3 bernilai 100 diperoleh dari penjumlahan kolom on hand minggu ke 2 + Schedule receipt minggu ke 3 – gross requirement minggu ke 3
0 +80- 40 = 40.
Kolom on hand minggu ke 4 diperoleh dari kolom on hand minggu ke 3 + Schedule receipt minggu ke 4 – gross requirement minggu ke 4
40 + 0 – 60 = -20
Karena nilai kolom on hand menunjukkan nilai negatif maka hal tersebut tidak sesuai dengan material requirement planning, sehingga kita kosongkan. Kita lanjutkan ke kolom di bawahnya, yakni kolom net requirement
![]() |
Tabel On Hand kode I |
3)Kolom minggu ke 4 net requirement diperoleh dengan mengurangi kolom gross requirement minggu ke 4 dengan kolom on hand minggu ke 3
60 – 40 = 20
Kolom minggu ke 5 net requirement Kolom minggu ke 5 net requirement diperoleh dengan mengurangi kolom gross requirement minggu ke 5 dengan kolom on hand minggu ke 4
60 – 0 = 60
Kolom minggu ke 6 net requirement diperoleh dengan mengurangi kolom gross requirement minggu ke 6 dengan kolom on hand minggu ke 5
60 – 0 = 60
![]() |
Tabel Net Requirement Kode I |
4) Kolom planned order receipt diisi sesuai dengan net requirement yang ada, karena kita menggunakan metode lot for lot,lot for lot adalah metode yang meniadakan biaya simpan atau biaya simpan sama denga 0, maka kolom planned order receipt kita sesuaikan dengan kolom net requirement, dengan menulis ulang di kolom net requirement dari minggu ke 4 sampai ke 6.
5)Kolom planned order release, ditulis sesuai dengan permintaan yang ada, dimana lead time 1 minggu, maka kolom planned order receipts kita majukan selama 1 minggu. Sehingga hasilnya sesuainya dengan kolom di bawah ini
![]() |
Tabel Planned Order Release kode I |
Output (Hasil Material Requirement planning)
Terdapat 2 output dari pembuatan material requirement planning
1)Output 1 adalah Rekomendasi jadwal produksi,yang membutuhkan awal proses produksi dan data pennyelesainnya, setiap tahapan pada pada bill of material memenuhi permintaan dari jadwal produksi induk (master production schedule)
2) Ouput 2 adalah Rekomendasi jadwal purchasing, hal ini berguna bagi staff purchasing untuk mengatur ketersediaan bahan baku yag ada supaya memenuhi pesanan jadwal produksi.