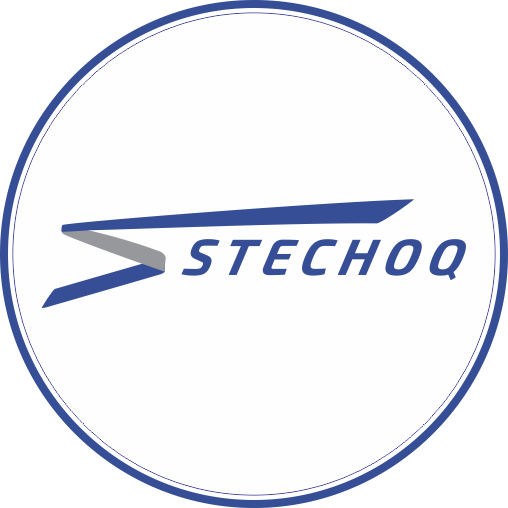
Supply Chain Management mengemukakan dua perbedaan sistem dasar, yaitu push system dan pull system. Push system terjadi saat perusahaan dapat memproduksi barang dalam jumlah besar (mencapai economics of scale) yang nantinya akan didistribusikan kepada konsumen. Sedangkan pull system terjadi saat perusahaan menginginkan tingkat efisiensi yang tinggi. Perusahaan tidak memproduksi barang/jasa sampai terjadi pesanan konsumen terhadap produk perusahaan. Dengan kata lain, pull system menghendaki produksi barang/jasa dan penambahan nilai suatu produk terjadi saat permintaan konsumen sudah ada, sehingga perusahaan tidak memerlukan persediaan (inventory). Sistem Tarik (Pull dimulai dari perkiraan tingkat output yang akan diperlukan, kemudian ditarik kebelakang untuk menentukan berapa barang yang diproduksi, kebutuhan bahan baku, sumberdaya yang diperlukan serta kebutuhan tenaga kerjanya. Konsep sistem tarik inilah yang menjadi dasar penerapan Just in Time (JIT).
Pull system atau sistem tarik adalah suatu sistem produksi yang dilakukan dengan menarik segala sumber daya (material, mesin, manusia) untuk membuat produk yang hanya sesuai dengan permintaan customer saja. Pada sistem produksi yang menggunakan pull system biasanya dibantu oleh pergerakan Kanban. Dengan menggunakan kanban, maka petunjuk produksi menjadi jelas dan terarah. Produk apa yang akan dibuat, mesin mana saja yang akan dilalui, dan berapa jumlah yang harus diproduksi bisa dikontrol dengan kartu Kanban. Dalam upaya menyiapkan proses perumusan solusi perbaikan sistem tarik ada beberapa hal yang harus dilakukan, yaitu:
a. Konsep 5S (Seiri, Seiton, Seiso, Seiketsu dan Shitsuke)
Konsep 5R / 5S merupakan proses perubahan sikap dengan cara menerapkan aspek penataan, kebersihan dan kedisiplinan di tempat kerja. Dengan menerapkan prinsip “A place for everything and everything in its place” maka setiap anggota organisasi dibiasakan bekerja dalam lingkungan kerja dengan standar tempat yang jelas. Pada konsep 5R / 5S juga bagian dari konsep kaizen yang memiliki arti penyempurnaan secara berkesinambungan pada kehidupan pribadi, kehidupan di keluarga, lingkungan sosial ataupun juga tempat kerja. Pengertian falsafah 5S yaitu:
Seiri/Sortir/Ringkas
Seiri adalah dengan menyisihkan barang yang dianggap tidak diperlukan dan barang
yang dianggap tidak diperlukan di tempat kerja dibuang.
Seiton/Susun/Rapi
Seiton (susun) adalah dengan menata peralatan kerja yang digunakan dengan rapi dan
menghilangkan kegiatan mencari agar alat-alat tersebut bisa dengan mudah ditemukan
secara cepat.
Seiso/Sapu/Resik
Seiso adalah dengan memelihara kebersihan pada tempat kerja. Setelah menjadi rapi,
langkah berikutnya adalah membersihkan tempat kerja, ruangan kerja, peralatan dan
lingkungan kerja.
Seiketsu/Standardisasi/Rawat
Seiketsu adalah dengan mempertahankan seiri, seiton, dan seiso agar proses tersebut
bisa berlangsung secara terus-menerus.
Setsuke/Swa disiplin/Rajin
Setsuke adalah suatu bentuk kedisiplinan yang mana hal tersebut menjadi kebiasaan,
sehingga para pekerja menjadi biasa mematuhi peraturan dan dilaksanakan penyuluhan
kepada para pekerja agar dapat bekerja dengan profesional. (Restupuri dan Wahyudin,
2019)
b. Konsep 7 Waste
Pengertian untuk tiap waste itu sendiri memiliki arti yang berbeda-beda, semua jeniswaste bersifat interdependen dan berpengaruh terhadap jenis lain. Tujuh waste dapat
dikelompokkan ke dalam tiga kategori utama yang dikaitkan terhadap man, machine, dan
material. Kategori man berisi konsep motion, waiting, dan overproduction. Kategori machine
meliputi overproduction waste, sedangkan kategori material meliputi transportation,
inventory, dan defect (Khannan dan Haryono, 2015) Berikut ini adalah tujuh jenis pemborosan
yang tidak bernilai tambah
c. Kesehatan dan Keselamatan Kerja
Keselamatan di tempat kerja diibaratkan sebagai sebuah investasi bisnis karena jika keselamatan kerja mengurangi kerugian finansial maka akan ada efek positif pada aspek kondisi kerja yakni terjadi penurunan kecelakaan kerja, tingkat produktivitas meningkat, dan kualitas hidup pekerja meningkat. Konsep terkait K3 ini dapat didukung dengan adanya Sistem Manajemen Keselamatan dan Kesehatan Kerja (SMK3) karena pembentukan dan penerapannya menjadi langkah awal dalam manajemen terstruktur sistem kesehatan dan keselamatan di lingkungan kerja. Tujuan utama penerapan SMK3 adalah menciptakan manajemen K3 di tempat kerja dengan mengintegrasikan pihak manajemen, pekerja, kondisi, dan lingkungan kerja untuk mencegah dan mengurangi kecelakaan dan penyakit akibat kerja, serta menciptakan tempat kerja yang aman, efisien dan produktif. Penerapan SMK3 ini melibatkan fungsi manajemen diantaranya program K3, pengorganisasian, pelaksanaan program, dan pengendalian (Hedaputri dkk, 2021).
Sinkronisasi dan volume pemenuhan permintaan sistem tarik dipengaruhi oleh beberapa faktor, yaitu:
a. Permintaan
Permintaan konsumen yang fluktuatif atau sukar diprediksi menyulitkan perusahaan untuk memenuhi berbagai macam permintaan untuk suatu periode.
b. Changeover
Dalam industri manufaktur, changeover berarti proses pergantian aktivitas produksi di suatu lini produksi dari satu produk ke produk lainnya. Waktu changeover dapat bervariasi tergantung kepada jenis produknya. Setiap melakukan pemenuhan pesanan dengan produk yang berbeda dipengaruhi oleh seberapa baik adaptasi sumber daya dalam menyesuaikan kondisi dengan jenis permintaan, seperti seberapa baik dan cepat setup mesin dalam menyesuaikan proses dengan karakteristik produk yang diminta.
c. Waste
Waste adalah suatu kegiatan proses kerja yang didalamnya tidak mampu memberikan nilai tambah atas pengolahan bahan baku di dalam value stream tertentu. Keuntungan sistem tarik adalah tepatnya jumlah permintaan produk yang mana perusahaan hanya perlu melakukan produksi dengan jumlah yang diminta, pola pikir menggunakan toleransi di setiap prosesnya adalah bisa dinyatakan suatu pemborosan. Untuk memenuhi output produk yang tepat sesuai permintaan, perlu mengeliminasi setiap waste yang ada sehingga aliran material dan produksi menjadi lancar.
d. Keseimbangan lini
Keseimbangan lini (line balancing) atau biasa disebut keseimbangan lintasan adalah suatu metode penugasan sejumlah pekerjaan ke dalam stasiun-stasiun kerja, yang saling berkaitan dalam satu lini produksi sehingga setiap stasiun kerja memiliki waktu yang tidak melebihi waktu siklus dari stasiun kerja tersebut. Keseimbangan lini merupakan faktor yang mempengaruhi sinkronnya rantai produksi serta dihasilkannya jumlah produk yang sudah ditentukan. Seimbang bukan berarti setiap lini harus mempunyai luaran dengan jumlah yang sama, melainkan harus sesuai dengan menghasilkan luaran yang didasarkan target jumlah luaran lain.
Dalam mengidentifikasi perintah tarik dan perintah produksi terdapat beberapa metode dan alat bantu. yaitu:
a. Material Requirement Planning
Material Requirements Planning (MRP) merupakan salah satu metode yang dapat digunakan untuk merencanakan jumlah kebutuhan bahan baku dalam mendukung kegiatan produksi dan menentukan kapan bahan baku perlu dipesan kembali. Dalam melakukan sistem tarik, perusahaan berarti mendapatkan informasi yang jelas untuk jumlah pemesanan produknya, dalam memenuhi jumlah permintaan, MRP sangat berguna dalam melakukan penjelasan pemenuhan kebutuhan mulai dari bahan baku sampai bagian assembly produk.
b. Just-in-time
Just In Time adalah suatu sistem yang dirancang untuk mendapatkan kualitas yang baik, menekan biaya, dan mencapai waktu dan biaya seefisien mungkin dengan menghilangkan pemborosan yang ada. Dalam sistem tarik, perusahaan tidak akan melakukan produksi jika tidak ada permintaan, maka dari itu metode JIT sangat berguna dalam menghadirkan proses dengan toleransi yang ketat dengan cara melakukan pendatangan bahan baku, proses produksi, dan pengantaran sesuai permintaan yang diajukan oleh konsumen.
c. Kanban
Kanban atau biasa disebut pull system adalah sistem komunikasi atau kartu perintah yang digunakan untuk melakukan pemesanan bahan baku sesuai dengan kuantitas kebutuhan yang diinginkan, kuantitas sesuai dengan kapasitas persediaan untuk menghasilkan suatu produk. Pada beberapa perusahaan yang menggunakan sistem tarik (biasanya dengan karakteristik produk yang terdiri dari banyak bagian), Kanban akan sangat berguna sebagai alat komunikasi perintah untuk memenuhi kebutuhan dari satu departemen ke departemen lain dalam perusahaan.
Sistem tarik atau Pull System merupakan proses operasi mulai dari tahap pembelian hingga delivery customer yang hingga saat ini dianggap modern dan bisa mengikuti arah pasar. Sedangkan istilah yang satunya, yaitu Push system, merepresentasikan sebuah sistem operasi tradisional dan konservatif, identik dengan aktivitas yang tidak memiliki nilai tambah atau istilahnya "waste".
Mengidentifikasi alternatif solusi perbaikan dengan menjawab permasalahan permintaan yang fluktuatif dengan jumlah atau produk yang bermacam-macam, bisa digunakan metode Heijunka untuk memperbaiki kerataan proses produksi berdasarkan beberapa level sinkronisasi level timing dan volume sesuai dengan line stop pergantian jenis produk yang ada di Balai Diklat Industri Yogyakarta. Selain itu dapat juga menggunakan metode Just in Time. Sistem produksi tepat waktu atau Just In Time merupakan sistem manajemen fabrikasi modern yang dikembangkan oleh perusahaan-perusahaan Jepang yang pada prinsipnya memproduksi jenis-jenis barang apa saja yang saat ini diperlukan dan dibutuhkan konsumen. Konsep Just In Time pada persediaan bahan baku dimana bahan baku yang digunakan untuk aktivitas produksi didatangkan pemasok atau supplier tepat pada saat bahan tersebut dibutuhkan pada proses produksi. Salah satu alat yang digunakan untuk merealisasikan sistem produksi Just In Time adalah Kanban. Kanban atau biasa disebut pull system adalah sistem komunikasi atau kartu perintah yang digunakan untuk melakukan pemesanan bahan baku sesuai dengan kuantitas kebutuhan yang diinginkan, kuantitas sesuai dengan kapasitas persediaan untuk menghasilkan suatu produk.
Mengidentifikasi kemungkinan kesulitan serta dampak positif dari solusi perbaikan sistem tarik mencakup biaya, waktu, luas area, peralatan dan jumlah anggota. Untuk melakukan perbaikan dengan suatu metode, selain akan mendapatkan keuntungan pasti juga akan menimbulkan beberapa kerugian di sisi lain. Berikut merupakan identifikasi dampak positif setiap alternatif solusi perbaikan berdasarkan kebutuhan dan kemampuan Balai Diklat Industri Yogyakarta :
Pada dasarnya karakteristik order konsumen terbagi menjadi 3 jenis antara lain:
Sebelum melakukan perbaikan pada sistem produksi menggunakan sistem tarik, perlu dilakukan perancangan/rencana kerja perbaikan sistem tarik. Dalam membuat sebuah rencana kerja perbaikan yang sesuai dengan sistem tarik ada beberapa hal yang perlu disesuaikan, yaitu:
Solusi perbaikan sistem tarik yang diterapkan di BDI Factory secara nyata dapat ditetapkan dengan tingkat sinkronisasi. Sinkronisasi dan volume pemenuhan permintaan sistem tarik dipengaruhi oleh beberapa faktor, sebagai berikut:
a. Permintaan
Permintaan konsumen yang fluktuatif atau sukar diprediksi menyulitkan perusahaan untuk memenuhi berbagai macam permintaan untuk suatu periode. Jumlah aktual permintaan sebisa mungkin dapat mendekati dengan hasil peramalan agar kondisi kekurangan material (Stock Out) ataupun kelebihan material (Overstock).
b. Proses Pergantian Aktivitas Produksi (Changeover)
Setiap melakukan pemenuhan pesanan dengan produk yang berbeda dipengaruhi oleh seberapa baik adaptasi sumber daya dalam menyesuaikan kondisi dengan jenis permintaan,
seperti seberapa baik dan cepat setup mesin dalam menyesuaikan proses dengan karakteristik
produk yang diminta.
c. Pemborosan (Waste)
Keuntungan sistem tarik adalah tepatnya jumlah permintaan produk yang mana perusahaan hanya perlu melakukan produksi dengan jumlah yang diminta, pola pikir menggunakan toleransi di setiap prosesnya adalah bisa dinyatakan suatu pemborosan. Untuk memenuhi output produk yang tepat sesuai permintaan, perlu mengeliminasi setiap waste yang ada sehingga aliran material dan produksi menjadi lancar
d. Keseimbangan Lini
Keseimbangan lini merupakan faktor yang mempengaruhi sinkronnya rantai produksi serta dihasilkannya jumlah produk yang sudah ditentukan. Seimbang bukan berarti setiap lini harus mempunyai luaran dengan jumlah yang sama, melainkan harus sesuai dengan menghasilkan luaran yang didasarkan target jumlah luaran lain.
Rencana perbaikan yang akan diterapkan sistem perbaikan tarik ini adalah dengan menggunakan metode Just-In Time (JIT). Metode JIT ini akan diimplementasikan dengan penggunaan Digital Control System (DCS) yang mana akan membantu memberikan perintah produksi apabila ada orderan yang masuk secara real time dan tepat jumlah. Nantinya setiap perintah produksi yang diterima oleh DCS akan dapat dikontrol langsung oleh pihak-pihak terkait agar kegiatan produksi benar-benar hanya memproduksi barang sesuai dengan jumlah yang dibutuhkan di waktu itu. Hal ini akan menekan kegiatan produksi yang berlebih dan dapat memperkecil biaya yang timbul dari persediaan.
Dalam menyelesaikan Solusi Perbaikan Sistem Tarik diperlukan rencana kerja perbaikan sistem tarik tersebut. Berikut ini adalah Proses untuk mendapatkan persetujuan rencana kerja perbaikan yang akan dijelaskan pada Gambar flowchart berikut. Alur memperoleh persetujuan dalam melakukan perbaikan Sistem Tarik.