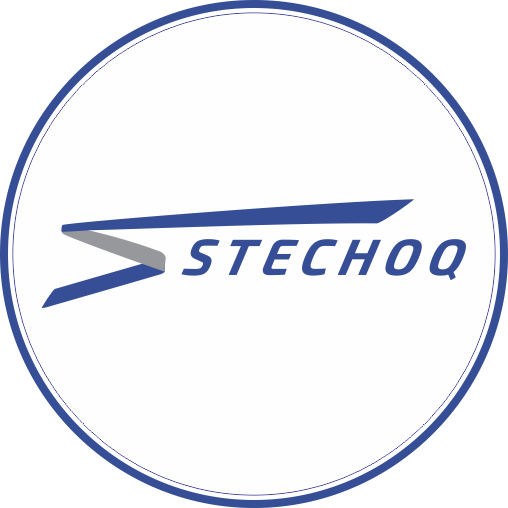
Pendekatan dasar untuk sistem produksi “Just-in-Time” (JIT) adalah untuk mengurangi biaya produk melalui penghapusan pemborosan. Dalam fasilitas produksi, pemborosan dapat didefinisikan sebagai cacat, stok, antrian, dan keterlambatan. Dengan menghilangkan tumpukan persediaan di lantai pabrik, inefisiensi operasi dapat diekspos. Oleh karena itu, memproduksi atau menerima persediaan "tepat waktu" untuk proses produksi selanjutnya dapat menghilangkan persediaan persediaan.
Manufaktur Just-In-Time (JIT) merupakan filosofi manajemen Jepang yang diterapkan dalam manufaktur. Pada dasarnya ini melibatkan barang yang tepat dengan kualitas dan kuantitas yang tepat di tempat yang tepat pada waktu yang tepat. Saat ini, semakin banyak perusahaan Amerika Utara mempertimbangkan pendekatan JIT dalam menanggapi lingkungan yang semakin kompetitif.
Kemampuan untuk mengelola persediaan (yang seringkali merupakan 80 persen dari biaya produk) untuk bertepatan dengan permintaan pasar atau mengubah spesifikasi produk dapat secara substansial meningkatkan keuntungan dan meningkatkan posisi kompetitif produsen dengan mengurangi persediaan dan pemborosan. Just In Time (JIT) merupakan filosofi manajemen, pendekatan terintegrasi untuk mengoptimalkan penggunaan sumber daya perusahaan, yaitu, modal, peralatan, dan tenaga kerja. Tujuan JIT adalah menghilangkan total pemborosan dalam proses pembuatan.
JIT merupakan serangkaian kegiatan terintegrasi yang dirancang untuk mencapai produksi volume tinggi menggunakan inventory minimal bahan baku, barang dalam proses dan barang jadi. Just In Time juga didasarkan pada logika bahwa tidak ada yang akan diproduksi sampai dibutuhkan. (H.k.Shivanad, 2006).
Prinsip dasar pertama dari produksi just-in-time merupakan sistem tarikan Selama bertahun-tahun sistem tarik telah mendapatkan banyak ketenaran di dunia manufaktur. Ini dapat dikaitkan terutama dengan salah satu alat yang digunakan dalam sistem tarik, kanban. Meskipun kanban adalah alat yang sangat baik untuk menerapkan sistem tarik, itu hanyalah alat. Seringkali saya menemukan di lautan luas materi tentang lean manufacturing dan TPS bahwa ada daya tarik dengan alat yang digunakan oleh Toyota dan orang lain untuk menerapkan tepat waktu. Meskipun ini tidak selalu merupakan hal yang buruk, penting untuk dipahami bahwa ini hanyalah alat dan sistem dapat diimplementasikan menggunakan berbagai alat. Beberapa orang ingin Anda percaya bahwa tanpa kanban, sistem tarikan tidak dapat diterapkan. Ini salah (Stewart, 2011). Esensi sebenarnya dari sistem tarik adalah aliran informasi. Dalam organisasi tradisional, informasi didorong melalui sistem. Karena bahan pada akhirnya akan mengikuti aliran informasi, bahan tersebut akhirnya didorong melalui sistem, menciptakan stok persediaan pada berbagai tahap proses pembuatan. Dalam didorong melalui sistem dan ada tiga puluh enam setengah hari inventory disistem. Ini adalah banyak modal kerja yang terikat dalam produk yang tidak memiliki nilai nyata bagi pelanggan.
Prinsip dasar kedua just in time adalah aliran produksi. Produksi aliran kontinu didasarkan pada konsep menghilangkan berhenti dan mulai terkait dengan manufaktur, sehingga menjaga proses produksi diratakan dan mempertahankan aliran material melalui proses. Aliran produksi bekerja bersamaan dengan sistem tarikan untuk mengurangi waktu tunggu pabrikasi secara keseluruhan dan mengurangi tingkat persediaan dalam proses. (Stewart, 2011) Idealnya pemrosesan aliran dicapai dengan memproduksi produk satu per satu. Untuk mencapai aliran satu bagian, produk diproduksi satu per satu dan diteruskan ke proses selanjutnya. Memproduksi komponen dalam batch untuk proses selanjutnya tidak diizinkan berdasarkan konsep one-piece flow. Dengan mencapai one-piece flow, kita dapat mengurangi start dan stop yang terkait dengan produksi batch tradisional. (Stewart, 2011).
Aspek fundamental terakhir dari produksi just-in-time adalah takt time. takt time adalah sinkronisasi produksi berdasarkan permintaan pelanggan. Ironisnya, takt time berakar di Jerman. Takt berasal dari kata Jerman Takzeit, yang berarti waktu siklus. Ini menarik karena waktu siklus dan takt time adalah dua konsep yang sama sekali berbeda, meskipun terkait (Stewart, 2011)
Takt Time = Total Waktu Produksi Harian / Total kebutuhan pelanggan setiap hari
Waktu Siklus = Total Waktu Produksi Harian / Total unit yang mungkin diproduksi
Takt time adalah waktu yang diperlukan untuk menghasilkan satu produk melalui proses produksi. Waktu ini diambil dengan mengambil total kebutuhan pelanggan per hari dan membaginya menjadi total waktu produksi harian yang tersedia. (Stewart, 2011) Misalnya, mari kita asumsikan bahwa permintaan pelanggan untuk produk tertentu adalah dua puluh ribu produk per bulan. Karena kami memiliki jadwal produksi dua puluh hari, ini memberi kami persyaratan produksi harian seribu produk per hari. Jika hari produksi saya didasarkan pada tujuh setengah jam produksi, itu memberi saya empat ratus lima puluh menit produksi, yang berarti setiap produk membutuhkan dua puluh tujuh detik untuk menghasilkan. Waktu takt saya untuk produk ini adalah dua puluh tujuh detik. (Stewart, 2011).
Staf manajemen produksi dan peningkatan berkesinambungan Toyota telah memasukkan rasa hormat terhadap kemanusiaan ke dalam Sistem Produksi Toyota dengan cara-cara berikut (Monden, 2012).
1) Semua jenis kegiatan yang sia-sia dihilangkan dari lantai pabrik. Operasi manusia yang sia-sia diganti dengan operasi bernilai tambah, sehingga mengurangi total waktu operasi standar dan jumlah pekerja. Pekerjaan yang berharga diberikan kepada manusia, sehingga meningkatkan moral sekaligus meningkatkan produktivitas.
2) Lini produksi dapat dihentikan oleh pekerja ketika masalah terjadi di lini tersebut. Seperti disebutkan sebelumnya dalam buku ini, praktik ini disebut jidoka, yang merupakan sistem kontrol cacat otonom. Di dunia Barat, ini disebut sebagai pemberdayaan.
3) Kelompok kecil seperti QC melakukan kegiatan peningkatan berkelanjutan dan menginstal perangkat kontrol cacat otonom. Selain itu, ada sistem saran yang dapat digunakan pekerja.
Sistem kanban adalah sistem informasi yang secara harmonis mengontrol produksi produk yang diperlukan dalam jumlah yang diperlukan pada waktu yang diperlukan dalam setiap proses pabrik dan juga di antara perusahaan. Ini dikenal sebagai produksi just-in-time (JIT). Di Toyota, sistem kanban dianggap sebagai subsistem dari seluruh Sistem Produksi Toyota. Dengan kata lain, sistem kanban tidak setara dengan Toyota Production System, meskipun banyak orang salah menyebut sistem kanban. Dalam bab ini, berbagai jenis kanban, penggunaannya, dan aturannya dijelaskan. Bagaimana kanban terhubung dengan banyak rutinitas pendukung di jalur produksi juga dibahas (Monden, 2012)
Banyak orang salah menyebut Sistem Produksi Toyota sebagai sistem kanban. Sistem Produksi Toyota membuat produk; sistem kanban mengelola metode produksi JIT. Singkatnya, sistem kanban adalah sistem informasi yang secara harmonis mengontrol jumlah produksi dalam setiap proses. Kecuali jika berbagai prasyarat sistem ini tidak diterapkan dengan sempurna (mis., Desain proses, standarisasi operasi, dan kelancaran produksi), maka JIT akan sulit direalisasikan, bahkan ketika sistem kanban diperkenalkan. (Monden, 2012)
Untuk mewujudkan tujuan JIT dari kanban, aturan berikut harus diikuti:
Inventory is at the minimum level necessary to keep operations running