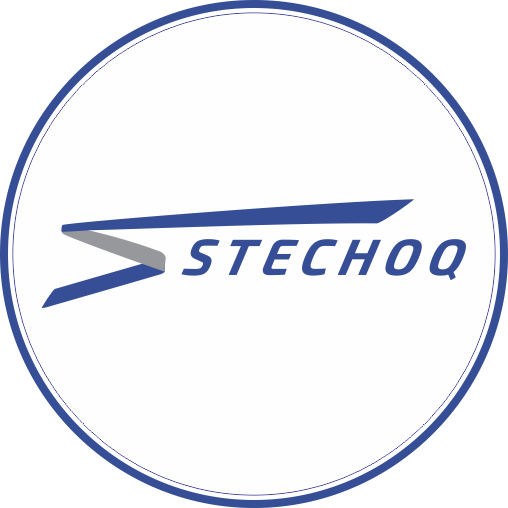
Operator adalah orang yang mengoperasikan atau menjalankan atau mengendalikan jalannya mesin produksi untuk membuat hasil produk di dalam Pabrik Industri. Sehingga seorang operator bisa di pastikan akan selalu berhubungan atau berhadapan langsung dengan mesin produksi di dalam Pabrik Industri. Dalam proses produksi, efisiensi adalah sebuah hal yang sangat penting. Dengan adanya efisiensi, output yang dihasilkan akan lebih optimal. Oleh karena itu perlu dilakukan perumusan solusi perbaikan proses kerja operator menjadi lebih efisien lagi.
Solusi perbaikan efisiensi proses kerja operator dilakukan untuk membuat jalannya proses produksi menjadi lebih baik sehingga output yang dihasilkan akan menjadi lebih optimal. Dalam upaya menyiapkan proses perumusan solusi perbaikan efisiensi proses kerja operator ada beberapa hal yang harus dilakukan, yaitu:
Metodologi merupakan prosedur ilmiah yang didalamnya termasuk pembentukan konsep, preposisi, model, hipotesis, dan teori, termasuk metode itu sendiri. Jadi metodologi perumusan perbaikan efisiensi proses kerja operator merupakan langkah-langkah atau prosedur yang dibuat dengan tujuan dapat memberikan efisiensi proses kerja operator. Berikut merupakan rancangan flowchart metodologi perumusan perbaikan efisiensi proses kerja operator.
Flowchart metodologi perumusan perbaikan
No | Prosedur/langkah | Penjelasan | Contoh BDI |
---|---|---|---|
1 | Identifikasi permasalahan pada kerja operator | Merumuskan permasalahan yang terjadi di sistem kerja operator. Dapat dilakukan dengan melihat apakah ada keadaan yang tidak sesuai dengan yang diharapkan. Beberapa tools yang dapat digunakan yaitu : VSM, ketidaksesuaian keadaan. |
Permasalahan: Kurang efisiennya proses produksi saat ini karena terdapat 3QC |
2 | Penetapan tujuan dan batasan perbaikan |
|
Tujuan: Batasan Perbaikan: |
3 | Penyusunan rekomendasi perbaikan | Rekomendasi dibuat sesuai dengan kebutuhan yang ada dengan memperhatikan problem, tujuan dan batasan ruang lingkup |
Gambaran Rekomendasi Perbaikan: Melakukan penerapan Quality Assurance (QA) pada proses produksi di BDI Factory |
4 | Simulasi rekomendasi perbaikan | Simulasi atau peragaan rekomendasi dilakukan untuk mengetahui seberapa aplikatifnya rekomendasi yang dibuat |
Simulasi: Melakukan penerapan Quality Assurance (QA) pada sebuah mesin Inject |
5 | Analisis dan Evaluasi | Dari simulasi yang sudah dilakukan, analisis diperlukan untuk mengetahui bagian mana yang perlu di improve atau di perbaiki. |
Analisis dan Evaluasi: Melakukan pembuatan SOP, TSK, dan TSKK sesuai penerapan QA |
6 | Penyusunan Rencana Implementasi | Disusun rencana implementasi rekomendasi perbaikan dengan memperhatikan target, waktu dan biaya |
Rencana:
|
7 | Implementasi | Melakukan implementasi sesuai rencana yang sudah dibuat. |
Implementasi: Pelaksanaan |
Process engineering adalah kegiatan merancang dan merekayasa proses dalam pembuatan produk dari material mentah hingga barang jadi. Process engineering dapat memberikan dasar untuk disiplin engineering lainnya dalam menetapkan desain yang lebih detail dan juga biaya. Process engineering yang ada di BDI factory disajikan pada flowchart berikut:
Flowchart Process Engineering di BDI Factory
Material yang berasal dari gudang material kemudian dibawa ke area produksi, kemudian dilakukan proses input material ke mesin injeksi, setelah itu dilakukan proses injeksi. Kemudian dilakukan finishing terhadap produk yang telah diproduksi. Produk tersebut kemudian diinspeksi lalu menjadi produk jadi (finish good). Quality engineering adalah kegiatan merancang dan menentukan aspek yang akan dijadikan pedoman dalam mengukur kualitas sebuah produk. Quality engineering di BDI factory:
Flowchart Quality Engineering di BDI Factory
Value engineering adalah kegiatan merancang atau mendesain nilai intrinsik yang ada di dalam produk atau proses sehingga memiliki nilai tambah dibanding keadaan sebelumnya. Value Engineering di workshop BDI: Material -> mesin injeksi -> barang jadi. Langkah pengaturan, penggabungan serta stabilitas beban kerja di BDI mungkin dilakukan, seperti pengaturan proses pergantian mold, penggabungan 2 proses inspeksi dengan meja karakuri. Langkah-langkahnya adalah seperti pada gambar berikut:
Flowchart Pengaturan, Penggabungan, dan Stabilitas Beban Kerja
Solusi perbaikan efisiensi proses kerja operator dilakukan untuk membuat jalannya proses produksi menjadi lebih baik sehingga output yang dihasilkan akan menjadi lebih optimal. Teknik pengumpulan data yang digunakan untuk pendataan abnormalitas adalah prinsip 5 Gen yaitu Genri, Gensoku, Genba, Genbutsu, dan Genjitsu.
Pengumpulan data dilakukan mengikuti prinsip teori umum dan pendekatan ilmiah, kemudian memecahkan masalah serta melakukan peningkatan proses, kemudian meninjau secara langsung dimana suatu permasalahan terjadi, melihat suatu kejadian atau benda dengan matanya sendiri, serta merasakan adanya solusi perbaikan pada proses produksi maupun proses kerja di dalam suatu industri. Pengumpulan data ini bertujuan untuk mengetahui solusi perbaikan efisiensi proses kerja operator demi proses produksi menjadi lebih baik sehingga output akan lebih optimal.
Solusi perbaikan efisiensi proses kerja orang adalah dengan mengusulkan dua alternatif solusi, yaitu penggunaan meja karakuri serta penerapan Quality Assurance pada proses kerja supaya dapat mengoptimalkan proses kerja yang ada di BDI Factory. Pembahasan yang lebih komprehensif terdapat pada sub bab berikut.
Penggabungan elemen kerja terjadi pada proses inspeksi, pada kondisi saat ini terdapat tiga elemen kerja inspeksi disebabkan sistem dan letak lini perpindahan material dan proses tidak mendukung aliran yang kontinyu serta dikarenakan skill operator yang kurang memadai sehingga membutuhkan proses inspeksi atau quality control yang berulang. Oleh sebab itu, di usulkan alternatif solusi perbaikan yang dapat mereduksi waktu pada proses produksi. Alternatif solusi yang pertama adalah menggunakan meja karakuri, pada proses ini proses injeksi dan pengambilan output digabung menjadi proses injeksi, hal tersebut mereduksi waktu sebesar 6 detik. Kemudian elemen inspeksi yang semula terdapat tiga elemen inspeksi digabung menjadi satu inspeksi saja sehingga mereduksi waktu sebanyak 16 detik.
Sedangkan untuk alternatif solusi yang kedua adalah penerapan QA. Proses finishing dan inspeksi pada kondisi saat ini digabung menjadi finishing & inspeksi operator yang mana dapat mereduksi waktu sebesar 22 detik, hal ini sangat berpengaruh apabila diterapkan di proses produksi.
Penggabungan elemen kerja ini sudah sesuai dengan kaidah process engineering karena tidak menghilangkan fungsi dan tujuan dari inti proses sebelumnya, penggabungan elemen inspeksi juga diperkirakan dapat memenuhi kaidah quality engineering karena meskipun elemen inspeksi berkurang namun telah dilakukan rekayasa kualitas dengan menjadikan satu elemen inspeksi di proses perbaikan dengan menghadirkan operator yang terampil (didapatkan dengan melakukan pelatihan) dan didukung dengan tambahan waktu yang memadai. Penggabungan kerja juga dinilai memenuhi aturan value engineering oleh tim karena anggaran yang dibutuhkan dapat dinilai sepadan dengan pengurangan lead time yang mana ini akan bermuara ke penghematan biaya.
di elemen kerja packing produk ke plastik pada proses sebelumnya membutuhkan usaha atau kerja lain untuk menghitung produk dan mengemas produk secara manual ke dalam plastik yang mana ini membutuhkan waktu tersendiri. Sementara packing produk di proses perbaikan akan dilakukan dengan memanfaatkan kemiringan dan gaya gravitasi yang mana produk akan jatuh langsung ke plastik kemasan dan operator akan melakukan perekatan plastik saat produk sudah mencapai jumlah yang sudah ditargetkan. Kegiatan ini memberikan efisiensi sebesar 55,67% atau yang semula membutuhkan 48,5 detik menjadi hanya 21,5 detik.
Pada alternatif kedua yaitu penerapan Quality Assurance (QA) efisiensi kerja dapat diperoleh dari semakin pendeknya alur proses produksi atau pengurangan stasiun kerja yang harus dilewati oleh produk. Menurut hasil perhitungan pada sub bab sebelumnya diperoleh nilai efisiensi mencapai 62,89% atau yang semula membutuhkan waktu sebesar 48,5 detik menjadi hanya 18 detik.
Pada alternatif pertama akan menyelesaikan permasalahan postur kerja dan cara kerja operator pada proses existing dinilai belum ergonomis pada elemen kerja mengambil output dari mesin yang mana membutuhkan kerja yang memaksa operator untuk membungkuk dari posisi duduk dan kemudian berjalan membawa produk ke area Quality Control karena area tersebut diluar jangkauan ergonomis dari posisi operator bekerja. Sementara elemen kerja mengambil output dari mesin di proses perbaikan, tidak membutuhkan usaha dari operator karena produk akan jatuh sendiri dengan memanfaatkan fasilitas perbaikan yang ada dan pemindahan ke area Quality Control dapat terakomodasi dari jangkauan tangan operator karena bantuan meja karakuri. Kegiatan ini secara langsung akan mengurangi takt time pada proses ini karena adanya meja karakuri memberikan pengurangan jarak antara area operator dengan area Quality Control.
Pada alternatif kedua yaitu penerapan Quality Assurance Operator secara ergonomis akan mengurangi jumlah gerakan dan jumlah stasiun kerja yang akan dilewati oleh produk. QA akan membuat semua produk dijaga kualitasnya sejak dari awal pengerjaan, disini jeda waktu operator saat menunggu produk selesai di inject akan digunakan untuk melakukan kegiatan sortir atau Quality Control dan hasil dari operator ini akan langsung diberikan kepada bagian QC Final untuk di packing. Secara ergonomis, kegiatan operator akan lebih optimal karena area kerja yang dilakukan mulai dari menunggu produk inject keluar dari mesin dan kegiatan sortir/ pengecekan dilakukan di area jangkauan operator.
a. Alternatif solusi penerapan meja kara-kuri
1.Kemungkinan kesulitan: Proses kerja yang memakan effort lebih hal ini dikarenakan design dari meja yang telah dibuat sebelumnya ternyata tidak cukup ergonomis bagi pekerja, selain itu pada penggunaannya ternyata meja kara-kuri tidak menambah nilai efisiensi kerja yg cukup signifikan. pada implementasi yang membutuhkan penyesuaian atau adaptasi dengan melakukan pelatihan dan pemahaman pada stakeholder terkait
2. Dampak positif : Proses penyortiran produk NG dapat dilakukan secara bersamaan di satu line, jarak meja yang berdampingan dengan mesin meminimumkan transportasi perpindahan produk, memudahkan proses kerja operator dalam menjalankan pekerjaanya serta mengurangi resiko keluhan fisik akibat postur kerja yang tidak baik.
b. Alternatif solusi penerapan Quality Assurance
a. Alternatif solusi penerapan meja kara-kuri
Perbaikan ini mungkin akan membutuhkan koordinasi dengan lini warehouse finish good dalam adaptasi dari sistem tarik yang ada. Sedangkan untuk efisiensi kerja operator akan berdampak cukup baik dimana hal ini akan menjadi ranah dari ruang lingkup di lini produksi.
b. Alternatif solusi penerapan Quality Assurance
Perbaikan ini mungkin akan membutuhkan koordinasi dengan seluruh bagian yang ada dalam proses produksi mulai dari penjagaan kualitas raw material oleh bagian warehouse raw material, bagian operator mesin inject, dan bagian QC final serta bagian warehouse finish good dalam penerapan sistem built in quality. Sedangkan untuk efisiensi kerja operator akan berdampak cukup baik pada semua bagian yang ada dalam proses produksi di BDI factory.
Pada kasus riil di lapangan proses kerja operator perlu disusun seefisien mungkin agar terus meningkatkan produktivitas perusahaan. Penyusunan rencana alternatif solusi perbaikan proses kerja operator akan mencakup tingkat fleksibilitas lini produksi menghadapi perubahan order pelanggan dan peningkatan produktivitas orang (man hour/pcs) sesuai dengan sub bab mengenai Solusi perbaikan efisiensi proses kerja operator ditetapkan sesuai dengan manfaat serta biaya investasi, Rencana kegiatan perbaikan efisiensi proses kerja operator disusun sesuai kemampuan dan kebutuhan perusahaan serta Proses untuk mendapatkan persetujuan solusi dan rencana perbaikan dilakukan sesuai prosedur yang akan dijabarkan pada sub bagian berikutnya
a. Menghadirkan Meja Karakuri (Alternatif 1)
Investasi yang dilakukan dalam menghadirkan alat dan fasilitas pada proyek ini sendiri adalah sebesar Rp 3.507.600. Sementara kebermanfaatannya yaitu mengurangi processing time (sampai produk terkemas di gudang) dari 48,5 detik menjadi 21,5 detik. Akibat memperoleh waktu siklus hanya sebesar 21,5 detik, maka untuk memenuhi satu pemesanan (2 box; 3600 unit) hanya memerlukan waktu 3 hari. Artinya setiap bulannya sistem produksi yang baru ini dapat menampung permintaan 8 kali atau sebanyak 16 box dalam seminggu dengan keuntungan Rp2.880.000 per bulan. Maka ROI dari desain perbaikan ini yaitu.
ROI = Keuntungan / Total investasi yang dilakukan
ROI = Rp2.880.000 / Rp3.507.600
ROI = 82%.
Artinya investasi yang dilakukan akan menghasilkan untung sebanyak 82% yang mana akan mulai mendapat untung (balik modal) di bulan ke 2.
b. Penerapan Quality Assurance (Alternatif 2)
Investasi yang dilakukan dalam meningkatkan keahlian/ kompetensi operator lewat pelatihan pada proyek ini sendiri adalah sebesar Rp 5.750.000. Sementara kebermanfaatannya
yaitu mengurangi processing time (sampai produk terkemas di gudang) dari 48,5 detik menjadi
18 detik. Akibat memperoleh waktu siklus hanya sebesar 18 detik, maka untuk memenuhi satu
pemesanan (2 box; 3600 unit) hanya memerlukan waktu 2,25 hari. Artinya setiap bulannya
sistem produksi yang baru ini dapat menampung permintaan 8 kali atau sebanyak 16 box dalam seminggu dengan keuntungan Rp2.880.000 per bulan. Maka ROI dari desain perbaikan ini
yaitu.
ROI = Keuntungan / Total investasi yang dilakukan
ROI = Rp2.880.000 / Rp5.750.000
ROI = 50%.
Artinya investasi yang dilakukan akan menghasilkan untung sebanyak 50% yang mana akan mulai mendapat untung (balik modal) di bulan ke 2.