Jidoka
- Jidoka” atau “Autonomation” adalah metode yang digunakan oleh Toyota untuk mencegah terjadinya error, defect (cacat) atau kesalahan produksi, dan merupakan salah satu pilar Lean Manufacturing. Konsepnya adalah segera menghentikan pekerjaan/proses ketika ditemukan kesalahan dalam proses tersebut, sehingga cacat dapat dihindari.
- Secara bahasa, Jidoka merupakan gabungan dari dua kata dalam Bahasa Jepang. Jika diterjemahkan kedalam Bahasa Inggris, dua kata tersebut artinya automation dan autonomous. Automation adalah pengambil-alihan kerja manusia oleh mesin, yang diperlukan untuk melakukan pekerjaan yang berulang dan monoton, seperti memasukkan botol kedalam kotak, mengisi folding box ke tempat loading, memasang tutup botol, dan sebagainya. Pekerjaan tersebut, jika dilakukan oleh manusia, akan rentan terhadap kesalahan karena pengulangan akan membuat manusia hilang konsentrasi dan bosan. Kesalahan akan berdampak pada kualitas produk atau keselamatan kerja operator sendiri.
- Jidoka adalah salah satu pilar Lean Production System. Jidoka adalah gabungan dari dua kata yaitu automation dan autonomous, sehingga Jidoka berarti autonomation.
- Automation didefinisikan sebagai pengambi lalihan mesin untuk menggantikan pekerjaan atau proses yang dilakukan manusia.
- Automation mengatasi beberapa kelemahan yang dikarenakan pekerjaan yang dilakukan manusia, dimana manusia akan sering dan memiliki kemungkinan kesalahan atau error terutama terhadap pekerjaan yang mudah dan berulang terus-menerus. Misalkan: pekerjaan untuk memasukkan botol ke dalam kotak, mengisi folding box ke tempat loading, menutup tutup botol, mengetuk bagian atas supaya rapat, dll. Pekerjaan ini terlihat mudah dan sederhana, tapi karena dilakukan terus-menerus dan berulang maka akan membuat manusia menjadi bosan dan menjadi rentan terhadap kesalahan.
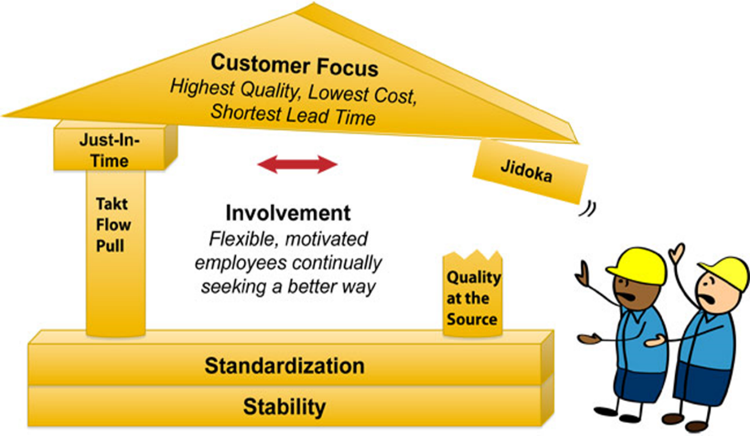
- Kesalahan ini bisa berdampak terhadap quality product atau berdampak ke safety dari operatornya. Automation tampaknya akan mengatasi kelemahan pekerjaan yang dilakukan oleh manusia, karena manusia sangat rentan terhadap kesalahan untuk pekerjaan yang mudah, berulang, dan tidak membutuhkan kreativitas. Ada ungkapan di Lean yaitu “don’t ask human to do machine’s job” yaitu jangan meminta orang untuk mengerjakan pekerjaan yang seharusnya bisa dilakukan mesin.
AUTOMATION
- Apakah automation adalah yang terbaik dalam melakukan proses? Tidak juga.
- Karena dalam proses produksi yang berjalan terus-menerus, ternyata mesin automation gagal dalam menghadapi error yang terjadi pada produk maupun error pada mesin. Dan mesin tidak mampu untuk mendeteksi segala macam kesalahan dan melakukan koreksi atas segala macam kemungkinan kesalahan proses. Sehingga jika dipaksa melakukan automation secara keseluruhan maka bisa dibayangkan seberapa besar mesin tersebut, seberapa lengkap systemnya, seberapa banyak feature pada mesin untuk melakukan koreksi terhadap kesalahan, dan betapa mahal jika membuat full automation seperti itu.
JIDOKA VS OTOMATISASI
JIDOKA
- Ketika terjadi masalah, mesin akan mendeteksi masalah dan akan menghentikan prosesnya.
- Defect tidak terjadi dan tools tidak rusak.
- Mudah melokalisie abnormality dengan instalasi stop device.
- Keuntungannya adalah dapat menghemat sumber daya manusia
OTOMATISASI
- Ketika terjadi masalah, mesin akan terus beroperasi sampai mesin operator switch off mesin.
- Defect terjadi berulang, banyak tool rusak.
- Sulit untuk membuat countermeasure terhadap masalah yang terjadi, karena penyebab masalah sulit ditemukan.
- Sumber daya manusia tidak berkurang/tetap
AUTONOMOUS
- Autonomous yaitu tindakan dari manusia sebagai operator sangat diperlukan. Manusia meskipun memiliki kelemahan untuk proses yang mudah dan berulang dalam hal menginspeksi dan mendeteksi, tapi memiliki kemampuan yang jauh diatas mesin dalam hal menanggapi kesalahan, menyikapi masalah baru, dan kemampuan untuk melakukan koreksi terhadap permasalahan. Disinilah Jidoka atau Autonomation masuk, yaitu mengambil kelebihan positif dari mesin dan kelebihan positif dari manusia secara bersamaan.
- Jidoka akan mempermudah manusia dalam menjalankan prosesnya, mempermudah dalam melakukan aktivitas berulang, mempermudah dalam mendeteksi kesalahan pada proses, produk, dan juga pada mesin. Mempermudah dalam memberikan deteksi dan warning jika terjadi kesalahan, dan sekaligus mencegah terjadinya kesalahan untuk aktivitas yang dilakukan manusia.
Mengapa JIDOKA dilakukan?
- Dapat meminimalisir cacat produk.
- Cacat lebih cepat dapat diidentifikasi.
- Umpan balik. Sehingga penanggulangan cepat dapat dilakukan. (Karena masalah dapat segera diketahui maka proses identifikasi dan penyelesaian masalah dapat lebih cepat diatasi).
Jidoka adalah salah satu faktor untuk keberhasilan implementasi Lean, mengapa ?
- Tingkat cacat yang tinggi menyebabkan penghentian jalur yang sering, yang akan membuat aliran dan tarik menjadi sulit.
- Cacat akan membahayakan takt time dan membuat ketidakseimbangan proses, meningkatkan lead time dan biaya
MANFAAT JIDOKA
- Memastikan & menjaga keamanan.
- Peningkatan kualitas.
- Memberdayakan orang.
- Cegah barang yang rusak dikirim ke tahap produksi berikutnya.
- Mengenali kelainan dalam produksi otomatis sehingga penyesuaian / perbaikan dapat dilakukan dengan cepat.
- Memungkinkan pemisahan mesin dan pekerjaan manusia.
- Menghilangkan kebutuhan operator untuk terus mengawasi mesin jika terjadi kerusakan.
- Penggerak utama untuk keuntungan besar dalam produktivitas
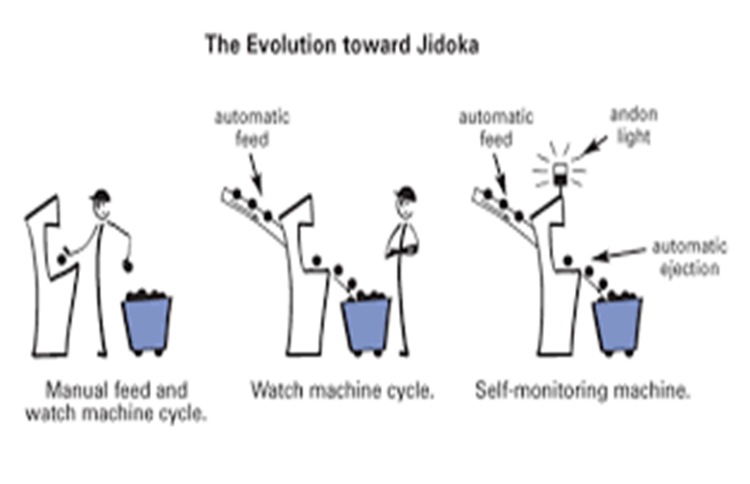
- Toyota Production System atau TPS, sering digambarkan sebagai sebuah rumah dengan dua pilar. Salah satu pilar mewakili Just-In-Time (JIT), dan pilar lainnya mewakili Jidoka. Logikanya, sebuah rumah tidak akan mampu berdiri tanpa pilar penyangganya, begitupun dengan TPS.
- Namun, yang terjadi adalah, kebanyakan dari perusahaan hanya berfokus pada mekanisme pelaksanaannya – takt time, standar kerja, kanban, dan pull production – tanpa menghubungkan semua proses tersebut kepada pilar-pilar yang menyangga keseluruhan sistem. Konsep JIT memang perlu dipahami dengan baik, tetapi Jidoka-lah yang menjadi kunci untuk melekatkan seluruh sistem. Banyaknya implementasi TPS yang gagal pada perusahaan terjadi karena tidak membangun kedua pilar dengan baik.
Langkah Melakukan JIDOKA
4 langkah melakukan jidoka:
- Mendeteksi kesalahan
- Menghentikan mesin
- Memperbaiki kesalahan secara langsung
- Menyelidiki akar penyebab masalah da menetapkan solusi
- Dua tahapan pertama dapat dilakukan secara mekanis maupun otomatis. Tools Poka-Yoke merupakan salah satu metode yang memungkinkan suatu proses pendeteksian masalah dan menghentikan kerja mesin. Namun, apabila ditelusuri lebih mendalam, setiap mekanisme dari TPS benar-benar dirancang untuk mendeteksi adanya masalah.
- Waktu dapat menjadi mekanisme deteksi yang kuat apabila siklus kerja diarahkan pada takt time. Ada kesempatan besar untuk mendeteksi masalah apabila ada waktu untuk merespon – dan bukannya mengidentifikasikan di akhir hari atau bahkan minggu. Jika anggota tim diberikan sarana untuk segera memberikan tanda apabila terjadi masalah, respon juga akan muncul dengan segera.
- Kanban juga dapat berfungsi sebagai sistem untuk mendeteksi terjadinya masalah. Jika inventori tidak melibatkan kanban, kemungkinan akan terjadi kelebihan produksi. Semua mekanisme dari lean manufacturing selalu mengikuti pola yang sama. Mereka dirancang untuk beroperasi minimal (JIT) untuk mendeteksi kondisi yang tidak normal atau perubahan sistem yang mungkin tidak diketahui.
- Langkah kedua adalah stop atau berhenti. Banyak karyawan yang salah mengerti dengan arti kata ini karena mereka berpikir untuk menghentikan semua proses hingga masalah teratasi, padahal ternyata tidak semua masalah akan menghentikan semua proses kerja mesin.
- Langkah ketiga dan keempat tidak dapat dilakukan secara otomatis. Mereka sepenuhnya menjadi tanggung jawab semua orang karena membutuhkan adanya diagnosa, analisis, dan pemecahan masalah. Seberapa baik organisasi dapat melalui semua tahapan pemecahan masalah dan menemukan solusi yang membawa mereka menuju kepada perbaikan secara terus menerus.
- Langkah ketiga adalah untuk memperbaiki masalah – untuk menemukan solusi yang tepat sehingga proses dapat berlanjut. Langkah ini memungkinkan adanya solusi sementara untuk menghindari terjadinya pengulangan masalah.
- Langkah keempat dan merupakan langkah terakhir adalah menyelidiki akar penyebab masalah dan menentukan solusi yang permanen. Tahap ini akan menjadikan semua orang yang terlibat memperoleh pengetahuan yang lebih banyak mengenai proses dan sistem produksi. Tergantung dari sifat masalah yang muncul, hal tersebut mampu menjadi satu solusi sederhana. Pastinya, terkadang dibutuhkan bantuan dari para black belt untuk menentukan solusi terbaik.
Tujuan JIDOKA
- Menjamin hasil produksi, mencapai kualitas terbaik.
- Penyederhanaan man power produksi.
- Mencegah terjadinya down time akibat adanya kelainan pada proses produksi
- Konsep JIT merupakan pendekatan yang kuat karena akan mengurangi biaya yang tidak diperlukan dan membantu mendeteksi masalah yang menyebabkan munculnya limbah. Jidoka merupakan respon terhadap masalah. JIT memang relatif mudah untuk diimplementasikan, namun tanpa Jidoka sebagai pendukung, JIT menjadi kurang efektif dan limbah bisa muncul kembali dalam waktu dekat. Kolaborasi yang baik antara JIT dan Jidoka akan membentuk mesin Kaizen yang mendukung sistem menjadi lebih baik setiap waktu
Kelebihan JIDOKA
Dapat mengurangi pemborosan sebanyak mungkin, hal ini mencakup:
- Pergerakan tenaga kerja yang kurang menghasilkan / Tidak memiliki nilai tambah (non Value Added), menyebabkan sedikit waktu dalam memproduksi sesuai permintaan pelanggan (tepat waktu).
- Setiap langkah produksi bisa dicek, berjalan lancar dan tanpa ada kesalahan karena adanya penerapan jidoka.
- Kualitas produk terjaga dengan baik.
Kekurangan JIDOKA
- Tidak ada satu pun dalam hidup yang berjalan seperti yang kita rencanakan, pasti akan ada masalah di prosesnya, begitu juga sistem tidak bekerja sesuai diharapkan.
- Sulit, biaya tinggi untuk diimplementasikan. Untuk menerapkan sistem ini perusahaan perlu membongkar sistem sebelumnya, hingga melatih karyawan bagaimana cara menerapkannya.
- Kompleks untuk digunakan.
- Masalah pasokan. Dalam lean manufacturing mereka menyimpan sejumlah kecil persediaan di tangan, jadi mereka membutuhkan pemasok yang dapat dipercaya sepenuhnya tidak mengganggu atau menunda persediaan dan selalu sesuai jadwal.
Contoh JIDOKA
- Beberapa contoh umum penggunaan Jidoka misalnya visual control, yaitu saat mesin mendeteksi kotak yang sudah penuh, maka mesin akan memberi peringatan berupa lampu dan buzzer untuk operator segera mengambil. Saat operator salah mengambil part tertentu untuk produk tertentu, mesin juga akan memberi buzzer peringatan. Saat terjadi kerusakan pada mesin tertentu, maka ada lampu yang memberi tahu area mana yang error untuk dilakukan koreksi.
- Saat produk selesai di oven, akan ada alarm warning. Saat terjadi speed yang berlebih maka akan ada warning atau system yang mengurangi speed, dll. Jidoka paling banyak menggunakan visual control dan system poka yoke (anti salah) yang dipasang untuk membantu mempermudah pekerjaan operator dan mencegah terjadinya kesalahan.