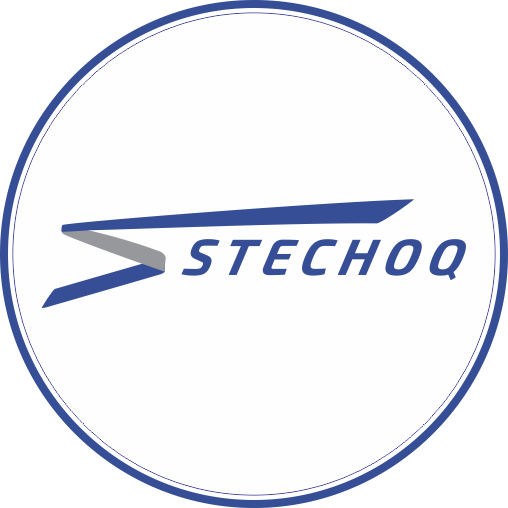
Arsenale di Venezia yang terletak Italia merupakan kompleks bekas galangan kapal dan gudang senjata di kota Venesia di Italia utara. Galangan ini bertanggung jawab atas sebagian besar kekuatan angkatan laut Venesia di bagian tengah. Ini adalah salah satu perusahaan industri berskala besar dan paling awal dalam sejarah. Proses perakitan disini terbilang unik dan modern di masanya karena menerapkan tata letak produksi dan standardisasi kerja yang meminimalkan perpindahan material dan kecepatan proses. Penemuan yang paling inovatif adalah pola assembly line yang memanfaatkan kanal, dimana rangka kapal bergerak menuju material dan bahan mengikuti desain perakitan.
Pada akhir abad ke-18, Jenderal Prancis Jean-Baptiste Vaquette de Gribeauval mempromosikan senjata standar di tempat yang dikenal sebagai Système Gribeauval setelah dikeluarkan sebagai tatanan kerajaan pada 1765. (Fokusnya pada saat itu adalah artileri lebih dari senapan atau pistol). Model perakitan senjata tersebut adalah "selective assembly", yang merupakan model perakitan yang dikerjakan secara ekonomis dengan tetap memberikan kemampuan dalam penggunannya. Model ini kemudian dipopulerkan oleh Eli Whiteney seorang Amerika dengan gagasan-gagasannya tentang Interchangeable part.
Scientific Management adalah teori manajemen yang menganalisis dan mensintesis alur kerja, konsep ini pertama kali di perkenalkan oleh Frederick Winslow Taylor dan dikenal sebagai bapak time study. Tujuan utama dari konsep ini adalah pengaturan upah dan meningkatkan efektifitas kerja serta efisiensi, terutama produktivitas tenaga kerja.
Motion study merupakan teknik memperbaiki kinerja karyawan melalui penelitian gerakan kerja. Tujuannya adalah untuk meningkatkan efisiensi karyawan, dengan cara menggabungkan teknik pengukuran waktu (time study) kerja dan gerakan kerja (motion study) karyawan. Meskipun sering dikaitkan dengan time study yang sudah diperkenalkan terlebih dahulu oleh Frederick Winslow Taylor, namun ada perbedaan yang mendasar antar kedua konsep tersebut. Jika time study sering menggunakan stopwatch sebagai alat kerja, berbeda dengan motion study yang lebih menitik beratkan pada analisa gerakan yang lebih ergonomis (ekonomis) dan efisien. Motion study pertama kali di populerkan oleh sepasang suami istri Frank Bunker Gilbreth dan istrinya Lillian Moller Gilbreth, mereka memiliki konsep 17 macam gerakan dasar yaitu "Therblig".
Jidoko berasal dari bahasa Jepang yang dapat di artikan otomatisasi cerdas atau otomatisasi dengan sentuhan manusia. Prinsip jidoka pada awalnya untuk mengoperasikan mesin pintal yang membutuhkan puluhan orang untuk mengoperasikannya, dengan menerapkan sistim otomasi ini mereka digantikan oleh seorang operator saja, Prinsip kerjanya adalah mesin pemintal mati secara otomatis ketika terjadi kesalahan/ produk cacat sehihingga dapat meminimalkan produksi cacat disetiap barang yang dihasilkan. Konsep Jidoka pertama kali diperkenalkan oleh Sakichi Toyoda. Sakichi Toyoda Lahir di Kosai, Shizuoka tanggal: 14 Februari 1867 dan wafat 30 Oktober 1930. Pada tahun 1929, Toyoda menciptakan mesin tenun otomatis pertama yaitu Toyoda Automatic Loom Work dan hak paten dijual ke Platt Brothers (perusahaan Inggris ) dengan nilai jual 100,000 pounds sterling, harga yang sangat fantastis dimasa itu dan membuat Toyota Industries menjadi terkenal dan mampu sejajar dengan pesaingnya di Eropa maupun Amerika.
Henry Ford lahir pada 30 Juli 1863 sampai dengan 7 April 1947 dia merupakan pendiri Ford Motor Company dan mengembangkan teknik perakitan produksi masal modern pertama, dimana proses dan layout kerja berurutan sesuai proses kerja sehingga memungkinkan proses kerja dapat berjalan efektif dan efisien.
Pada masa itu Toyota masih terkendala pergantian alat (changeover) yang masih tinggi yaitu antara dua hingga delapan jam, akibatnya Toyota tidak mampu membayar waktu produksi yang hilang (lost time) sedangkan permintaan pasar yang tinggi. Untuk mengatasi masalah tersebut Taiichi Ohno yang pada saat itu bertindak sebagai manager of the machine shops pergi ke Amerika untuk mempelajari kerangka kerja dari program Pelatihan Perang Dunia II AS dalam Industri (TWI), yang disebut ECRS - Eleminate (Eliminasi), -Combine (Campurkan), -Rearrange (Tata Ulang), dan -Simplify (Sederhanakan).
Just in Time merupakan sistem yang dirancang untuk mengurangi persediaan yang berlebih, Taiichi Ohno (大野 耐) menerapkan sistem tersebut dengan tujuan yaitu sebagai berikut :
Siklus Deming berfokus pada upaya meningkatkan kualitas dan sekaligus mengurangi biaya (dengan mengurangi limbah, pengerjaan ulang, pengurangan staf dan meningkatkan loyalitas pelanggan). Kuncinya adalah mempraktekkan perbaikan terus-menerus dan menganggap manufaktur sebagai suatu sistem, tidak bisa dipisah-pisahkan satu sama lain. Siklus Deming menggunkan konsep PDCA. Siklus Deming pertama kali diperkenalkan oleh William Edwards Deming lahir pada 14 Oktober 1900 sampai dengan 20 Desember 1993. Dia adalah seorang insinyur Amerika, ahli statistik, profesor, penulis, dosen, dan konsultan manajemen. Pada tahun 1950 William Edwards Deming pergi ke Jepang untuk melatih ratusan insinyur, manajer,sarjana serta memberikan perlatihan tentang konsep kualitas dengan tujuan mambantu membangun kembali industri dan pendidikan Jepang yang porak poranda setelah bom Atom. Desember 1950 Japanese Union of Scientists and Engineers (JUSE) mendirikan Deming Prize yang bertujuan untuk memberikan penghargaan kepada William Edwards Deming sebagai balas jasa atas semua kebaikannya membangun kembali Industri dan pendidikan di Jepang pasca PD II.
Manual book Toyota Production System (TPS) untuk internal perusahaan membuat buku manual TPS oleh Fujio Cho, Sugimori, dan lainnya.
Toyota Motor Corporation menerbitkan deskripsi resmi TPS untuk pertama kalinya pada tahun 1992 dan direvisi pada tahun 1998.
Prinsip lean berasal dari industri manufaktur Jepang. Istilah ini pertama kali diciptakan oleh John Krafcik seorang akedemisi dari Massachusetts Institute of Technology, di Cambridge, Massachusetts, United States. dalam artikelnya yang berjudul "Triumph of the Lean Production System", berdasarkan tesis masternya di MIT Sloan School of Management.
James P. Womack, Daniel Jones, dan Daniel Roos membuat buku yang berisikan tentang definisi dan rencana kerja untuk perusahaan yang ingin melakukan transformasi Lean, buku tersebut berjudul The Machine That Changed the World dan menjadikan buku terlaris internasional.
Lean Six Sigma adalah metodologi yang bergantung pada upaya tim kolaboratif untuk meningkatkan kinerja dengan secara sistematis membuang limbah dan mengurangi cacat produksi. Metode ini menggabungkan lean manufacturing yang dikenal dengan kecepatan produksinya karena fokus menghilangkan pemborosan (muda) dan Six Sigma yang dikenal kualitasnya.
Konsep lean pada awalnya dikenalkan pada ford production system yang disusun pada tahun 1990-an oleh Henry Ford. Beliau mengemukakan mengenai flow production yang berarti saat suatu tugas atau aktivitas diselesaikan, maka tugas atau aktivitas yang selanjutnya harus dimulai. Konsep tersebut selanjutnya dikembangkan dan dipraktikkan pada Toyota Production System oleh Kichiro Toyoda.
Konsep lean yang kemudian mengantarkan Toyota sebagai perusahaan manufacturing terhebat di dunia. Menciptakan Toyota Way yang merupakan bentuk continous improvement yang bertujuan untuk mengeleminasi waste yang menyebabkan kerugian atau tidak menghasilkan nilai sama sekali, sehingga terciptalah budaya lean. Keberhasilan Toyota diperoleh karena memiliki kemampuan membangun strategi dalam menumbuh kembangkan kepemimpinan, tim dan budaya yang digunakan membangun hubungan dengan supplier, serta membentuk organisasi yang selalu belajar (learning organization).
1 Identify VALUE
VALUE dalam perspektif pelanggan adalah segala aktivitas yang memberi nilai tambah pada produk sehingga pelanggan mau membayar untuknya.
2 Map the VALUE STREAM
Value Stream adalah langkah yang harus diterapkan setelah mengetahui apa yang dianggap bernilai dimata pelanggan meliputi proses-proses membuat, memproduksi dan menyerahkan produk. mengidentifikasi semua tahapan proses mana yang memberikan nilai tambah bagi konsumen akhir dan mana yang tidak memberikan nilai tambah sehingga harus dieleminasi.
3 Create FLOW
Buat langkah-langkah yang bernilai tambah sehingga proses mengalir lancar sampai ke konsumen. Langkah ini bisa digambarkan dalam future state of VSM.
4 Establish PULL
Setelah aliran proses mengalir lancar, buat sistem tarik (PULL), jangan dorong (PUSH). Sistem PULL berarti konsumen menarik nilai (VALUE) dari aktivitas sebelumnya (upstream activity).
5 Seek PERFECTION
Setelah nilai dan alirannya teridentifikasi, pemborosan dihilangkan, proses dibuat mengalir lancar, dan sistem tarik diterapkan, mulai lagi proses perbaikan sampai kondisi proses terjadi tanpa pemborosan.
No | Tools | Keterangan |
1. | 5S | Pengaturan area kerja untuk mengeliminasi pemborosan yang ditimbulkan akibat area kerja yang kurang terorganisir. 5S = Seiri (Sort), Seiton (Storage), Seiso (Shining), Seiketsu (Standardize), Shitsuke (Self-Discipline) |
2. | Andon | Sistem visual yang menginformasikan status proses sehingga abnormalitas bisa langsung terdeteksi dan tindakan bisa segera diambil. |
3. | Gemba | Pengamatan langsung di lapangan tempat di mana proses/aktivitas dilakukan untuk meningkatkan pemahaman proses beserta permasalahannya. |
4. | Heijunka | Bentuk penjadwalan produksi yang bertujuan untuk membuat batch lebih kecil dengan pengurutan/kombinasi varian produk dalam proses yang sama. |
5. | Hoshin Kanri | Penyelarasan antara strategi perusahaan, perencanaan manajemen, dan pekerjaan di lantai produksi. |
6. | Jidoka | Perancangan alat yang memiliki kemampuan otomatisasi parsial dan bisa berhenti saat ada cacat terdeteksi. |
7. | Kaizen | Strategi di mana para pekerja bekerja sama secara proaktif untuk melakukan perbaikan dalam proses produksi. |
8. | Kanban | Metode pengaturan aliran barang, baik internal maupun eksternal, dengan menggunakan kartu sinyal. |
9. | OEE | Teknik pengukuran produktivitas suatu proses berdasarkan tiga ukuran: availabilitas, kinerja, dan kualitas. |
10. | Poka Yoke | Perancangan deteksi dan pencegahan kesalahan untuk mencapai zero defects. |
11. | Single Minute Exchange of Die | Pengurangan waktu setup. |
12. | Takt Time | Penyeimbangan kecepatan produksi dengan permintaan pelanggan. |
13. | Total Productive Maintenance | Pendekatan pemeliharaan sistem/mesin yang menyeluruh yang bersifat proaktif dan preventif untuk memaksimalkan waktu operasional sistem/mesin. |
14. | Visual Management | Indikator atau kontrol visual yang digunakan di tempat produksi untuk meningkatkan penyampaian informasi. |
Six Sigma adalah usaha yang terus menerus untuk mengurangi pemborosan, menurunkan variansi dan mencegah cacat. Six sigma merupakan sebuah konsep bisnis yang berusaha untuk menjawab permintaan pelanggan terhadap kualitas yang terbaik dan proses bisnis yang tanpa cacat. Kepuasan pelanggan dan peningkatannya menjadi prioritas tertinggi, dan Six sigma berusaha menghilangkan ketidakpastian pencapaian tujuan bisnis.
Adalah Carl Frederick Gauss (1777-1885) yang pertama kali memperkenalkan konsep kurva normal dalam bidang statistik. Konsep ini kemudian dikembangkan oleh Walter Shewhart di tahun 1920 yang menjelaskan bahwa 3 sigma dari nilai rata-rata (mean) mengindikasikan perlunya perbaikan dalam sebuah proses. Pada akhir tahun 1970, Dr. Mikel Harry, seorang insinyur senior padaMotorola's Government Electronics Group (GEG) memulai percobaan untukmelakukan problem solving dengan menggunakan analisa statistik. Denganmenggunakan cara tsb, GEG mulai menunjukkan peningkatan yang dramatis: produk didisain dan diproduksi lebih cepat dgn biaya yg lebih murah. Metoda tsb kemudian ia tuliskan dalam sebuah makalah berjudul "The StrategicVision for Accelerating Six Sigma Within Motorola". Dr. Mikel Harryb kemudian dibantu oleh Richard Schroeder, seorang mantan executive Motorola, menyusun suatu konsep change management yang didasarkan pada data. Hasil dari kerja sama tersebut adalah sebuah alat pengukuran kualitas yang sederhana yg kemudian menjadi filosofi kemajuan bisnis, yang dikenal dengan nama Six Sigma. Strategi penerapan six sigma yang diciptakan oleh DR. Mikel Harry dan Richard Schroeder disebut sebagai The Six Sigma Breakthrough Strategy. Strategi ini merupakan metode sistematis yang menggunakan pengumpulan data dan analisis statistik untuk menentukan sumber-sumber variasi dan cara-cara untuk menghilangkannya.
Six sigma merupakan kegiatan yang dilakukan oleh semua anggota perusahaan yang menjadi budaya dan sesuai dengan visi dan misi perusahaan. Tujuannya meningkatkan efisiensi proses bisnis dan memuaskan keiginan pelanggan, sehingga meningkatkan nilai perusahaan. Strategi penerapan six sigma yang diciptakan oleh DR. Mikel Harry dan Richard Schroeder disebut sebagai The Six Sigma Breakthrough Strategy. Strategi ini merupakan metode sistematis yang menggunakan pengumpulan data dan analisis statistik untuk menentukan sumber-sumber variasi dan cara-cara untuk menghilangkannya. Proyek six sigma mempunyai pengaruh besar terhadap kepuasan konsumen dan pengaruh yang signifikan pada bottom-line. Proyek didefinisikan secara jelas dalam hal expected key deliverables, yaitu DPMO level atau sigma quality levels, RTY, Quality Cost dsb. Dalam pendekatan keseluruhan, masalah nyata diterjemahkan dalam bentuk data satistik. Hal ini dilakukan dengan pemetaan proses, yaitu mendefinisikan variablevariabel kunci input proses (key process input variables KPIVs or ‘ x’s) dan variable-variabel kunci output proses (key process output variables KPOVsor ‘ y’s). kekuatan statistical tools digunakan untuk menentukan statistical solution. Ada lima tahap atau langkah dasar dalam menerapkan strategi Six Sigma ini yaitu Define-Measure–Analyze-Improve-Control (DMAIC), dimana tahapannya merupakan tahapan yang berulang atau membentuk siklus peningkatan kualitas dengan Six Sigma. Siklus DMAIC dapat digambarkan sebagai berikut :
Six Sigma merupakan pendekatan menyeluruh untuk menyelesaikan masalah dan peningkatan proses melalui fase DMAIC (Define, Measure, Analyze, Improve, Control). DMAIC merupakan jantung analisis six sigma yang menjamin voice of costumer berjalan dalam keseluruhan proses sehingga produk yang dihasilkan memuaskan pelanggan.
Dasar Lean Manufacturing Taiichi Ohno menyusun sistem Lean. Ini telah diperluas dan diperdalam oleh serangkaian praktisi yang luar biasa, termasuk (Dennis, 2015):
a. Hiroyuki Hirano : sistem 5S.
b. Seiichi Nakajima : Pemeliharaan produktif total (TPM)
c. Kenichi Sekine : Aliran berkelanjutan
d. Shigeo Shingo : Jidoka dan SMED
Terdapat fokus 6 pilar pada Lean Manufacturing House, yaitu :