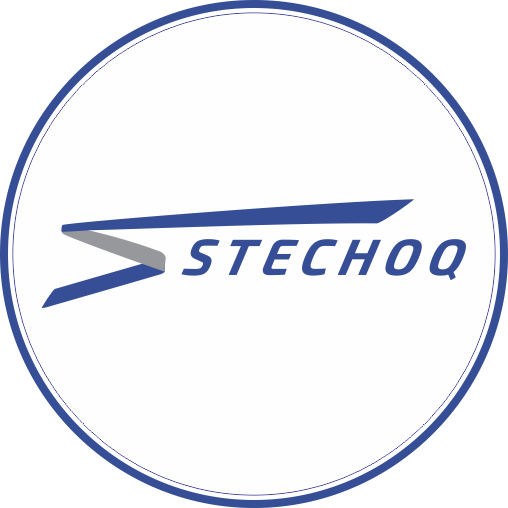
Kata “Poka Yoke” berasal dari bahasa Jepang yang artinya adalah mencegah kesalahan yang dikarenakan oleh kecerobohan oleh tenaga kerja manusia. Menurut konsep Poka Yoke, pada dasarnya sifat manusia adalah pelupa dan cenderung untuk berbuat salah. Apalagi yang sering terjadi di Tempat kerja, pekerjalah yang sering disalahkan. Hal ini bukan saja dapat mematahkan semangat kerja karyawan tersebut tetapi juga tidak dapat menyelesaikan masalah yang terjadi. Oleh karena penerapan Metode kerja POKA YOKE menjadi sangat penting dalam menghindari kesalahan yang terjadi.
Konsep Paka Yoke ini pertama diperkenalkan sekitar tahun 1960-an oleh Shigeo Shingo yang merupakan bagian dari Sistem Produksi Totoya (Toyota Production System).
Poka = Poka Misu = Kesalahan yang dikarenakan Kecerobohan (Careless Mistakes)
Yoke = Yokeru = Menghindari (avoid)
Poka Yoke adalah suatu Teknik untuk mengatasi dan menghindari kesalahan sederhana yang dikarenakan oleh manusia atau pekerja tersebut (Human Error) di tempat kerja dengan cara mencegahnya langsung dari akar penyebab (root cause) kesalahan dan menarik perhatian khusus dalam suatu pekerjaan atau tugas sehingga tidak memiliki kemungkinan untuk membuat kesalahan.
Poka-yoke yang baik memenuhi persyaratan berikut:
a. Sederhana, dengan umur panjang dan perawatan rendah
b. Reliability Keandalan tinggi
c. Biaya rendah
d. Dirancang untuk kondisi tempat kerja
Lantai produksi biasanya merupakan sumber poka-yoke terbaik.
a. Sistem Inspeksi dan Kontrol Zona
Di Toyota, konsep "kontrol zona." Ini digunakan dan Masing-masing dari wlayahnya mengukur tingkat manajemen mulai dari pemimpin tim, Human Resource, hingga manajer pabrik didorong untuk berpikir dalam hal wilayahnya. Misalnya, sebuah tim zona pemimpin adalah tim dan area kerja langsungnya. Pemasok dan pelanggan adalah tim hulu dan hilir. Ini cara berpikir memaksa pengembangan kontrol yang berlebihan, yang merupakan inti dari rekayasa keandalan.
b. Inspeksi Cacat
Ini merupakan inspeksi “good – not good”, yang tujuannya adalah untuk mencegah cacat dari sampai ke pelanggan atau ke proses hilir. Ini merupakan postmortem kegiatan yang sering dilakukan oleh departemen inspeksi terpisah, yang umumnya memerlukan sedikit akar penyebab analisis atau umpan balik untuk cacat sumber. Inspeksi penilaian tidak memperkuat proses atau orang kami, dan mereka boros. Pendekatan yang lebih efektif memang ada.
c. Inspeksi Informatif — Mengurangi Cacat
Hal Ini dirancang untuk menemukan cacat, bukan kesalahan, dan memberi umpan balik ke sumber, yang kemudian mengambil tindakan korektif. Seringkali mereka memerlukan penggunaan alat statistik seperti protokol pengambilan sampel dan SPC. Informatif inspeksi cenderung lebih unggul dari inspeksi penilaian, tetapi umpan balik dan tindakan balasan sering terlambat. Inspeksi informatif paling efektif adalah yang melibatkan pemeriksaan diri atau pengecekan yang berurutan. Memeriksa sendiri berarti operator memeriksa pekerjaannya sendiri. Cell berbentuk U mendukung pemeriksaan sendiri oleh menempatkan proses awal dan akhir secara berdampingan. Secara berurutan memeriksa proses hilir memeriksa kerusakan dan memberikan umpan balik segera. Pengecekan seperti itu harus dilakukan peer to peer karena pengawas dapat memeriksa tampaknya menghukum. Di Toyota pengecekan yang berurutan dapat dilakukan sangat efektif ketika mencakup 100% item. Jalur perakitan kondusif untuk jenis pemeriksaan ini.
d. Inspeksi Sumber — Mencegah Cacat
Hal Ini merupakan metode inspeksi yang dirancang untuk menemukan kesalahan yang mungkin mengarah pada cacat dan memberikan umpan balik cepat ke sumbernya. Target Toyota Cambridge adalah 100% inspeksi proses prioritas. Inspeksi sumber dapat dikategorikan sebagai vertikal atau horizontal.
e. Inspeksi Sumber Vertikal
Hal Ini membutuhkan pencarian hulu untuk penyebab root. Misalnya, gerinda pada potongan logam di toko perakitan mungkin memiliki sumbernya di lasan toko. Atau kebocoran air dalam perakitan mungkin karena aplikasi yang tidak tepat sealant di toko cat. Pendekatan standar untuk pemecahan masalah dan loop umpan balik yang kuat di Toyota dengan cepat mengidentifikasi dan menyerang masalah bersama. Umpan balik hulu dan hilir adalah kunci untuk meningkatkan proses kemampuan dan penahanan.
f. Inspeksi Sumber Horisontal
Hal Ini melibatkan pencarian akar penyebab dalam departemen. Misalnya, root penyebab cacat yang salah dan hilang di toko perakitan sering kali adalah ketidakhadiran.
g. Inspeksi (pencegahan kesalahan)
Inspeksi informatif (pencegahan cacat) bisa efektif, terutama ketika didasarkan pada pemeriksaan diri atau berturut-turut. Sebagai contoh:
h. Peringatan
Peringatan dalam poka-yoke mengingatkan kita akan kelainan dengan mengaktifkan bel atau cahaya. Yang paling terkenal mungkin adalah papan Toyota andon, yang mengingatkan grup pemimpin untuk masalah dengan menyalakan nomor proses, memainkan musik, atau keduanya.Toyota andon terlibat ketika seorang anggota tim menarik kabelnya yang berjalan di sepanjang garis. Garis terus bergerak sampai mencapai posisi tetap. Karena masing-masing proses memiliki posisi tetap, anggota tim dapat menyelesaikan setidaknya satu siklus operasi. Ini sangat mengurangi potensi cacat yang diciptakan oleh menghentikan garis di pertengahan siklus.
Poka-yoke dapat mendeteksi penyimpangan dalam benda kerja atau metode kerja atau penyimpangan Benda Kerja Jenis poka-yoke menggunakan perangkat penginderaan untuk mendeteksi kelainan pada berat, dimensi, atau bentuk produk, misalnya:
a. Berat: Menetapkan standar berat dan menimbang setiap produk menggunakan keseimbangan.
b. Dimensi: Membuat standar untuk ketebalan, diameter dalam dan luar, dan seterusnya, dan mengidentifikasi penyimpangan menggunakan limit switch, sumbat, JIG, mata fotolistrik, dan sejenisnya.
c. Bentuk: Membuat standar untuk sudut, jumlah dan posisi lubang, kelengkungan,dan sebagainya, dan mendeteksi penyimpangan dengan sakelar batas, pin locator, gangguan dalam peluncuran, dan detektor serupa.
Penyimpangan Metode Kerja dapat terjadi, dan itu diklasifikasikan dengan Jenis poka-yoke menggunakan sensor untuk mendeteksi kesalahan dalam gerakan standar, untuk contoh:
a. Sensor fotoelektrik menghitung berapa kali tangan pekerja istirahat balok dalam meraih bagian. Jika diperlukan jumlah hitungan tidak terpenuhi, bagian harus hilang.
b. Sebuah penghitung menghitung jumlah pengelasan spot yang dibuat pada benda kerja. Itu klem tidak akan terlepas kecuali nomor yang benar telah dibuat. Dengan jenis poka-yoke ini maka pekerjaannya harus ditata sedemikian rupa proses hilir tidak dapat dilanjutkan kecuali proses hulu telah lengkap.:
c. Dalam pengeboran dan pengelasan, jig pengelasan harus dibuat yang hanya akan pegang benda kerja yang sudah dibor.
d. Ketika merakit beberapa model, sensor fotolistrik seharusnya digunakan untuk mendeteksi bentuk model karakteristik. Sensor kemudian bisaterkait dengan bagian kontainer, sehingga hanya kontainer yang diperlukan untuk Model yang diberikan akan terbuka.
Penghitung sangat berguna dalam hal ini. Sebagai contoh:
a. Saklar batas dapat digunakan untuk menghitung jumlah lubang yang dibor dalam Benda kerja.
b. Kiat las dapat diubah saat jumlah tertentu tercapai. Sebuah penghitung menghentikan mesin las ketika jumlah yang diperlukan tercapai dan tidak akan memulai ulang hingga tip baru dipasang.
Metode bagian yang hilang juga bisa efektif. Sebagai contoh:
a. Jika jumlah komponen dalam kit perakitan terstandarisasi, sisa komponen akan menunjukkan kesalahan kelalaian. Ukur kondisi kritis seperti tekanan, suhu, tegangan, atau parameter proses lainnya. Pekerjaan tidak dapat dilanjutkan kecuali nilainya ada direntang yang telah ditentukan. Sebagai contoh:
b. Pengukur tekanan mematikan proses saat tekanan berlebih atau bocor terdeteksi.
c. OuplPasangan ganda dimatikan motor saat suhu berlebih terdeteksi di bantalan.
d. Kunci pas torsi menyediakan torsi dalam kisaran target dan ditutup di luar jangkauan.
3. Alat Deteksi Poka-Yoke
Teknologi sensor adalah area yang kaya dan berkembang. Di Toyota kami terbatas hanya dengan kreativitas kita. Sensor dapat diklasifikasikan sebagai kontak dan nonkontak perangkat (Dennis, 2015).
a. Sensor Kontak
Sensor kontak yang paling umum adalah
b. Metode Non-kontak
Perangkat ini mendeteksi gangguan dalam sinar fotolistrik, kedekatannya benda padat, bagian logam, serat, warna, sinar ultraviolet, cahaya inframerah, menghitung kelainan, berkas elektron, dimensi, tekanan, suhu, fluktuasi arus listrik, dan getaran. Berikut ini beberapa yang biasa digunakan perangkat (Dennis, 2015):
1) Photoelektrik: Digunakan secara luas sebagai layar cahaya untuk memastikan alat berat area bersih sebelum mesin bergerak; juga digunakan untuk menghitung tindakan, jatuh benda, dan dimensi benda kerja.
2) Detektor bagian logam: Digunakan untuk menghitung jumlah sekrup yang dipasang, verifikasi apakah suatu bagian dikeluarkan dari pers, dan konfirmasikan keselamatan itu kandang tertutup.
3) Suhu: Termometer dan termokopel digunakan untuk mendeteksi perubahan suhu mati, motor, dan. oven curing
4) Tekanan: Pengukur tekanan mendeteksi penyumbatan cairan pada pipa dan tekanan berlebih dalam mesin.
5) Fluktuasi arus listrik: Banyak digunakan dalam pengelasan spot untuk memeriksa arus sekunder yang membahayakan integritas lasan. Poka-yoke merupakan inti dari langkah 1 dan 4, dan dengan demikian meningkatkan proses keduanya Kemampuan dan penahanan cacat. Poka-yoke membantu kami menangkap kesalahan dan Cacat lebih dekat dengan kondisi aktual yang menyebabkan mereka. Masalah kita pemecah memiliki kesempatan yang lebih baik untuk sampai ke akar penyebab karena proses kondisi tidak akan banyak berubah. Poka-yoke membantu memastikan “TKP,” untuk menggunakan CSI (TKP investigasi) metafora, belum berubah ketika kita sampai di sana. Sebaliknya, inspeksi setelah terlambat sudah terlambat; TKP dan petunjuk telah manja.
Untuk terus meningkatkan kualitas, kita perlu strategi jidoka jangka panjang. Untuk mempertahankan jidoka, sistem harus mendorong improvement process atau biasa disebut dengan kaizen. mendefinisikan tingkat kemampuan dan pengungkungan untuk proses kami. Ini pada gilirannya dapat diterjemahkan ke dalam skor dan peringkat untuk setiap proses. Sistem penilaian kami harus sederhana dan tidak bergantung pada statistic metode (Dennis, 2015).