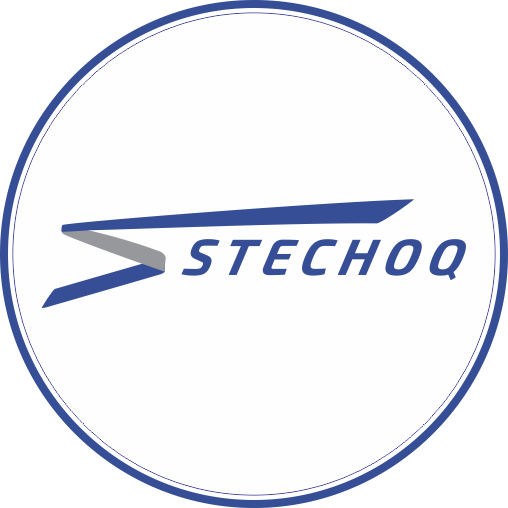
Terdapat beberapa solusi perbaikan efisiensi proses kerja yang di antaranya adalah Sortir, Susun, Sapu, Standardisasi, dan Swa disiplin (5S) dan Standarisasi kerja operator yang akan diuraikan sebagai berikut.
Operator adalah sekelompok orang yang bertugas mengoperasikan mesin, kendaraan atau sejenisnya. Pada kasus BDI Factory, operator yang dimaksud ialah orang yang bertugas mengoperasikan mesin injeksi molding. dilansir dari maxipro.co.id seorang operator memiliki tugas diantaranya memeriksa bahan bakar mesin, melaporkan temuan kerusakan pada mesin kepada pengawas lapangan, serta memastikan perawatan dari mesin tersebut. Berikut merupakan kegiatan operator mesin injeksi di BDI:
Melakukan perbaikan minor pada mesin
Beberapa kegiatan diatas bertujuan memastikan mesin digunakan dengan optimal dalam proses produksi baik dalam jangka pendek maupun jangka panjang. Optimal yang dimaksud yaitu tidak menimbulkan kesalahan yang dapat merugikan perusahaan. Selain memastikan mesin berjalan dengan baik operator juga harus memastikan bahwa dirinya aman saat bertugas.
Memastikan mesin berjalan secara optimal merupakan tanggung jawab besar bagi operator. Salah satu cara menjaga mesin dengan baik yaitu dengan meningkatkan efisiensi mesin melalui konsep 5R/5S yaitu Ringkas/sortir, Rapi/susun, Resik/sapu, Rawat/standarisasi dan Rajin/ Swa disiplin.
5R merupakan suatu cara untuk mengatur atau mengelola tempat kerja menjadi tempat kerja yang lebih baik secara berkelanjutan. Penerapan bertujuan untuk mencapai tingkat efisiensi dan produktifitas yang tinggi dalam sebuah perusahaan. Berikut merupakan tabel penjelasan setiap aspek 5R dan implementasinya pada kegiatan operator mesin injeksi. Operator mesin harus mengetahui dimana barang dan peralatan diletakan
Aspek 5R/5S | Pengertian | Implementasi pada Kegiatan Operator Mesin Injeksi |
---|---|---|
Ringkas/ Sortir | Mengatur segala sesuatu, memilah sesuai dengan aturan atau prinsip tertentu. Menyisihkan barang yang tidak diperlukan di tempat kerja dan buang. |
operator mesin harus mampu membedakan barang mana yang penting atau tidak penting saat proses produksi melalui mesin berlangsung |
Rapi/Susun | Berarti menyimpan barang di tempat yang tepat atau dalam tata letak yang benar sehingga dapat dipergunakan dalam keadaan mendadak. Hal itu merupakan cara untuk menghilangkan pencarian |
Operator mesin harus mengetahui dimana barang dan peralatan diletakan |
Resik/Sapu | Menjaga kebersihan barang sehingga menjadi bersih melalui kegiatan seperti membuang sampah, kotoran dan benda asing serta membersihkan segala sesuatu. Diutamakan sebagai pemeriksaan terhadap kebersihan dan menciptakan tempat kerja yang tidak memiliki cacat dan cela. |
Operator mesin harus menjaga kebersihan mesin saat mesin beroperasi maupun tidak |
Rawat/standarisasi | Terus-menerus dan secara berulang-ulang memelihara. Ringkas, Rapi, dan Resik. Rawat mencakup kebersihan pribadi dan lingkungan. |
Operator harus menjaga, memelihara dan memastikan barang yang tidak dibutuhkan tidak berada di area mesin, memastikan barang/peralatan tetap pada tempatnya setelah digunakan serta menjaga kebersihan mesin |
Dengan membangun kebiasan 5R atau 5S pada operator diharapkan dapat
mengoptimalkan penggunaan mesin serta meminimalisir kerugian perusahaan.
Standarisasi Kerja adalah peraturan pada saat membuat barang di tempat kerja, yaitu cara melakukan produksi yang paling efektif dengan urutan tanpa muda, mengumpulkan pekerjaan, dan memfokuskan gerakan manusia. Standarisasi menurut Kamus Besar Bahasa Indonesia adalah penyesuaian bentuk (ukuran, kualitas, dan sebagainya) dengan pedoman (standar) yang ditetapkan. Dalam kegiatan kerja operator mesin injeksi harus memiliki acuan dan pegangan. Akibat tidak adanya acuan dalam pelaksanaan kegiatan operator membuat organisasi tidak berfungsi dengan baik, hal ini dikarenakan para operator bingung atas pekerjaan yang mereka akan kerjakan selanjutnya, dan pihak manajemen pun tidak mempunyai pedoman dalam pengambilan keputusan, sehingga apabila ada suatu kesalahan atau kekeliruan tidak bisa dianalisis dimana kesalahan itu terjadi karena tidak memiliki alur pedoman yang jelas.
Tujuan utama dari pengukuran adalah untuk mengumpulkan data untuk digunakan dalam mengatur standar-standar pekerjaan ketatausahaan. Menurut Simamora (2004), semakin jelas standar kinerjanya, makin akurat tingkat penilaian kinerjanya. Menurut Atmoko (2011: 2) standar kerja adalah pedoman atau acuan untuk melaksanakan tugas pekerjaan sesuai dengan fungsi dan alat penilaian kinerja instansi/ perusahaan berdasarkan indikator-indikator teknis, administratif dan prosedural sesuai dengan tata kerja, prosedur kerja, dan sistem kerja pada unit kerja yang bersangkutan
Berdasarkan kegiatan operator mesin injeksi di BDI factory berikut beberapa standarisasi yang dibutuhkan operator:
a. Standarisasi 5R: yaitu pedoman kerja yang berisi semua aspek 5R atau 5S meliputi:
b. Standarisasi Safety dan K3: yaitu pedoman operator dalam mencegah terjadinya kecelakaan kerja seperti aturan-aturan, larangan operator dan kewajiban operator untuk memakai APD apabila diperlukan.
c. Standarisasi rule penanganan abnormality: yaitu pedoman bagi operator saat menemukan kondisi tidak sesuai keadaan normal contohnya ditemukan barang Not Good (NG) secara berturut-turut melebihi 3. saat menemukan kondisi tersebut langkah-langkah apa saja yang harus dilakukan operator, dimana harus melapor dan bagaimana tindakan selanjutnya harus tertera jelas.
d. Standarisasi pemasangan molding: yaitu pedoman bagi operator yang berisi langkah- langkah pemasangan/pergantian molding mesin injeksi. Standarisasi ini bertujuan untuk mempercepat waktu pergantian molding.
Standar kerja adalah sebuah pedoman atau acuan untuk melaksanakan tugas pekerjaan sesuai dengan fungsi dan alat penilaian kinerja instansi/perusahaan berdasarkan indikator- indikator teknis, administratif dan prosedural sesuai dengan tata kerja, prosedur kerja, dan sistem kerja. Beberapa dokumentasi yang dibutuhkan untuk standarisasi kerja operator yaitu:
a. Dokumen SOP (Standar Operasional Prosedur) merupakan panduan yang berkaitan dengan prosedur yang harus dijalankan. Dokumen SOP minimal memuat penjelasan SOP yang buat, tujuan, ruang lingkup, referensi, istilah dan definisi, tanggung jawab, prosedur dan pihak terkait
b. Check Sheets yaitu lembar yang dirancang sederhana berisi daftar hal-hal yang diperlukan untuk tujuan perekaman data sehingga pengguna dapat mengumpulkan data dengan mudah, sistematis, dan teratur pada saat data itu muncul di lokasi kejadian
c. Dokumen TSK (Tabel Standar Kerja) merupakan instruksi kerja yang menggambarkan dengan jelas kondisi pekerjaan di tempat tersebut yang sekaligus menggambarkan masing-masing proses tersebut di dalam suatu tempat kerja. Tabel ini menggambarkan gerakan orang dengan lay out dalam satu siklus. Tabel standarisasi kerja ini dipakai juga sebagai alat untuk pengawasan kerja yang dapat langsung terlihat. Selain itu, tabel ini juga memiliki fungsi untuk menangkap poin-poin masalah yang tertangkap secara visual di tiap line, dapat juga digunakan sebagai alat untuk instruksi kepada pelaku kerja.
Standar Kerja Operator atau biasa disebut dengan SOP dibuat dengan tujuan tertentu. Tujuan dari dibuatnya SOP adalah untuk menjaga konsistensi kinerja pada setiap karyawan di perusahaan. Dalam perusahaan tertentu, seorang manajer bisa mengetahui kualitas karyawannya dari bagaimana karyawan tersebut menjalankan SOP yang berlaku. Jika seorang karyawan masih belum maksimal, maka dapat dilakukan evaluasi berupa pemberian pelatihan. Selain tujuan, SOP juga memiliki fungsi utama yaitu dapat memudahkan karyawan untuk melaksanakan pekerjaannya. Dengan berpedoman pada SOP, maka setiap karyawan akan mengetahui langkah-langkah apa saja yang harus dilakukan dan yang tidak boleh dilakukan ketika melakukan pekerjaan. Dalam menyusun sebuah standar kerja/SOP adapun langkah- langkah yang perlu dilakukan diantaranya :
Langkah pertama adalah membuat susunan kerja. Langkah ini merupakan pondasi utama yang akan mempengaruhi kualitas SOP di kemudian hari.
Setelah itu, langkah selanjutnya adalah merencanakan alur proses. Maksud dari merencanakan alur proses ini adalah membahas hal-hal yang berkaitan dengan menentukan format SOP, membuat template dan bagaimana SOP tersebut dapat diakses.
Dilanjutkan dengan melakukan wawancara kepada setiap karyawan. Hal ini bertujuan untuk mengetahui aktivitas harian karyawan dalam pekerjaan serta mengetahui bagaimana karyawan tersebut bekerja. Dengan melakukan hal ini, maka Anda mengetahui apa saja yang perlu dipaparkan dalam sebuah SOP.
Langkah berikutnya setelah melakukan wawancara karyawan adalah mulai menulis SOP. Setelah SOP selesai ditulis, sebaiknya bahas SOP tersebut dengan pihak-pihak yang terkait. Hal ini bertujuan untuk mengetahui apakah masih ada celah atau ketidaksesuaian peraturan yang ada pada SOP yang telah ditulis. Jika SOP tersebut sudah dianggap baik, maka SOP sudah dapat disosialisasikan kepada karyawan dan pihak lain yang terkait.
Setelah SOP ditulis, disetujui, dan disosialisasikan maka pelatihan perlu dilakukan supaya SOP yang sudah disusun dapat berjalan dengan baik dan sesuai dengan apa yang diharapkan. Setelah pelatihan, Anda dapat memberikan jangka waktu selama 6 sampai 12 bulan untuk akhirnya diadakan evaluasi. Evaluasi tersebut akan membahas apakah ada hal yang salah dalam SOP, baik akan ditambah atau dihilangkan. Berikut flowchart tahapan pembuatan standarisasi kerja operator mesin injeksi molding:
Operator process mapping tools merupakan peta yang memetakan proses kerja yang dilakukan operator. Salah satunya jenis operator process mapping tools adalah peta kerja. Peta kerja adalah suatu alat yang menggambarkan kegiatan kerja secara sistematis dan jelas. Melalui peta kerja ini, maka dapat dilihat semua langkah atau kejadian yang dialami oleh suatu benda kerja dari mulai masuk ke pabrik (dalam bentuk bahan baku), kemudian menggambarkan semua langkah yang dialaminya, seperti transportasi, operasi mesin, pemeriksaan, dan perakitan, sampai akhirnya menjadi produk jadi, baik produk lengkap atau bagian dari suatu produk lengkap. Dengan peta ini juga didapatkan informasi-informasi yang diperlukan untuk memperbaiki metode kerja, seperti benda kerja yang harus dibuat, waktu operasi mesin, kapasitas mesin, bahan bahan khusus yang harus disediakan, alat-alat khusus yang harus disediakan, dan sebagainya. Pada dasarnya peta-peta bisa dibagi kedalam dua kelompok besar berdasarkan kegiatannya, yaitu peta kerja keseluruhan dan peta kerja setempat.
Yamazumi chart merupakan gambaran cycle time operator dalam bentuk grafik balok yang terdiri dari tumpukan tiga balok utama. Tiga balok tersebut menggambarkan sifat pekerjaan yang ada nilai tambah, tidak ada nilai tambah serta berjalan. Selain itu, di atas balok ketiga, digambarkan dua balok kecil berjajar sebagai gambaran tambahan cycle time akibat pekerjaan yg bersifat insidental serta yang berfluktuasi. Total nilai Cycle Time (CT) dibandingkan dengan garis Takt Time (TT) sehingga terlihat apakah beban kerjanya berlebih (CT lebih besar dari TT) atau kurang (CT lebih kecil dari TT). Cycle time adalah durasi waktu/kecepatan untuk membuat satu buah produk, sesuai kemampuan operator atau mesin, pada saat ini. Sedangkan Takt time adalah standar durasi waktu/kecepatan untuk membuat satu buah produk yang dihitung berdasar kebutuhan pelanggan.
Berdasarkan Yamazumi chart yang sudah dibuat diketahui bahwa permasalahan yang timbul tidak meratanya waktu cycle time antar proses. Hal ini menyebabkan timbulnya idle atau waktu menganggur pada operator.
Dalam melakukan proses perbaikan permasalahan yang ada dapat dilakukan dengan pengurangan pekerjaan insidental (irregular and baratsuki), berjalan (walking), tidak ada nilai tambah (non valuable work).
a. Pengurangan pekerjaan insidental (irregular and baratsuki) yaitu pengurangan pekerjaan-pekerjaan yang tidak teratur. Pekerjaan incidental terdiri dari dua yaitu pekerjaan irregular (tidak beraturan) dan pekerjaan baratsuki (penyebaran) yang tidak merata. indikator yang dapat dilakukan yaitu Analisa MURA dan MURI (ketidakteraturan & kesulitan proses). Berdasarkan yamazumi chart yang telah dibuat diketahui bawah pada setiap proses kerja di BDI factory tidak merata. Pada proses Finishing dan QC 1 memiliki cycle time 2 kali lipat dari proses QC 2.
b. Pengurangan pekerjaan berjalan (walking) yaitu pekerjaan yang membutuhkan gerak fisik dalam arti ini seperti berjalan. Indikasi yang biasa digunakan yaitu dengan memperhatikan gerakan bolak-balik memutar, naik turun di setiap elemen untuk diperkecil. Berdasarkan kasus di BDI factory ketahui bahwa gerakan bolak-balik yang sering terjadi pada proses QC dimana operator QC harus bolak balik mengambil produk jadi di area tertentu.
c. Pengurangan pekerjaan tidak ada nilai tambah (non valuable work) yaitu pekerjaan-pekerjaan yang tidak memberikan nilai tambah pada produk yang dibuat. Berdasarkan kasus di BDI Factory diketahui bahwa proses yang tidak memiliki nilai tambah yaitu proses quality control atau QC yang terjadi secara berulang selama 3 kali. Saran yang dapat diberikan yaitu pengurangan proses QC.
Stabilitas adalah suatu kemantapan, ketetapan dan keseimbangan serta kestabilan situasi yang kondusif sehingga perusahaan atau suatu lembaga bisa berjalan dengan baik. Dalam konteks proses kerja, stabilitas proses kerja merupakan kemantapan, ketetapan dan keseimbngan seta kestabilan pada proses kerja yang dilakukan operator. kestabilan proses kerja akan berpengaruh pada hasil produksi. Semakin stabil hasil produksi akan mudah dikontrol, sesuai dengan perencanaan dan sebaliknya apabila kurang stabil akan menyebabkan kesulitan operator dalam menghasilkan produk yang sesuai standar perusahaan dan berujung pada ketidaksesuaian dengan perencanaan. Faktor-faktor yang mempengaruhi stabilitas proses kerja operator yaitu:
a. Ergonomi kerja (gerakan operator), berhubungan dengan gerakan-gerakan yang dilakukan operator. Semakin besar variasi gerakan antar operator semakin kecil stabilitas proses kerja yang dilakukan. Sebaliknya semakin kecil variasi gerakan antar operator semakin besar tingkat stabilitas prosesnya. Ada 3 prinsip ekonomi gerakan menurut Mundel yaitu:
Pengumpulan data dilakukan sesuai dengan prosedur serta dilakukan genchi dan genbutsu. Genchi berasal dari Go and See yaitu observasi dan wawancara terkait permasalahan yang terjadi pada proses produksi di BDI Factory untuk mendapatkan data permasalahan yang ada di proses produksi. Sedangkan genbutsu adalah fakta atau keadaan yang sebenarnya terjadi di lapangan. Kedua teknik pengumpulan ini selalu diutamakan dalam proses pemecahan masalah karena dapat menggambarkan fakta atau keadaan sebenarnya yang ada di lapangan.
Selain metode diatas, terdapat metode lain yang dapat digunakan, yang diantaranya adalah Genri, Gensoku, Genba, Genbutsu, Genjitsu. Pengumpulan data dilakukan mengikuti prinsip teori umum dan pendekatan ilmiah, kemudian memecahkan masalah serta melakukan peningkatan proses, kemudian meninjau secara langsung dimana suatu permasalahan terjadi, melihat suatu kejadian atau benda dengan matanya sendiri, serta merasakan kenyataan seperti gejala-gejala adanya permasalahan serta pengaruhnya terhadap proses produksi maupun proses kerja di dalam suatu industri. Pengumpulan data ini bertujuan untuk mengetahui kestabilan proses kerja operator karena kestabilan tersebut akan berpengaruh terhadap hasil produksi.
SOP produksi di area mesin injeksi. Perlu adanya SOP produksi diarea mesin injeksi di maksudkan untuk mengurangi Human Error dan proses produksi menjadi lebih
produktif dan efisien.SOP Changeover Molding. Penyusunan SOP Changeover Molding ditujukan untuk
menciptakan kemudahan dan keteraturan dalam proses penggantian molding hingga tidak mengganggu proses produksi.SOP Kesehatan dan Keselamatan Kerja. Adanya penerapan K3 dimaksudkan untuk
memberikan informasi kepada pekerja agar melaksanakan tugas dan tanggung jawab dengan aman dan nyaman sehingga terhindar dari penyakit atau kecelakaan akibat kerja.Stabilisasi proses kerja operator merupakan Persoalan kerja operator dalam setiap elemen kerja yang ditetapkan sesuai dengan target takt time. Alternatif solusi perbaikan stabilisasi proses kerja operator diidentifikasi agar operator dapat bekerja dengan stabil. Alternatif solusi perbaikan dikoordinasikan sesuai prosedur berdasarkan ruang lingkup dan tanggung jawab kegiatan perbaikan stabilisasi proses kerja operator. Rencana kegiatan perbaikan stabilisasi proses kerja operator disusun sesuai kemampuan dan kebutuhan perusahaan.
Berdasarkan kasus di BDI factory mengenai metode dan prosedur perbaikan proses kerja operator ketahui bahwa, dari analisis perbaikan Pengurangan pekerjaan insidental (irregular and baratsuki) didapat data bahwa pada setiap proses kerja di BDI factory tidak merata. Pada proses Finishing dan QC 1 memiliki cycle time 2 kali lipat dari proses QC 2. Selain itu, dari analisis perbaikan Pengurangan pekerjaan berjalan (walking) sering terjadi gerakan bolak-balik pada proses QC dimana operator QC harus bolak balik mengambil produk jadi di area tertentu. Berdasarkan hasil analisis perbaikan pengurangan pekerjaan tidak ada nilai tambah (non valuable work) diketahui bahwa proses yang tidak memiliki nilai tambah yaitu proses quality control atau QC yang terjadi secara berulang selama 3 kali.
Selain itu, kondisi lapangan BDI Factory diketahui bahwa gerakan operator pada saat melakukan proses kerja masih kurang efisien karena operator sering membutuhkan waktu cukup lama saat mencari barang atau peralatan yang dibutuhkan. Hasil temuan di BDI Factory, menampilkan bahwa operator mesin injeksi sudah melaksanakan 5S namun dalam kenyataannya sering mengalami kendala karena minimnya pengawasan. Operator mengenakan APD yaitu sarung tangan dan sepatu karet. Diketahui di BDI Factory ditemukan alat-alat dalam kondisi baik, namun masih diletakkan pada tempat atau lokasi yang belum pasti. sehingga operator sendiri kadang kesulitan saat melakukan pencarian barang.
Dilakukan proses observasi dan wawancara terkait permasalahan (genchi genbutsu) pada proses produksi di BDI Factory untuk mendapatkan data-data permasalahan proses produksi. Pada observasi didapatkan 2 data proses yang tim nilai memiliki banyak aktivitas yang tidak bernilai tambah, proses tersebut adalah proses di mesin injeksi dan proses changeover molding, berikut merupakan datanya.
a. Proses di area mesin injeksi
Berikut merupakan proses di area mesin injeksi yang dimuat dalam tabel di bawah
Proses di mesin injeksi terdiri dari aktivitas yang bernilai tambah dan tidak bernilai tambah serta di dalamnya ditemukan juga banyak aktivitas yang dinilai sebagai waste activity. Aktivitas tersebut harus diminimasi melalui perbaikan lini kerja dan juga pemberlakukan SOP.
b. Changeover molding
Berikut merupakan proses pergantian molding yang dimuat dalam tabel di bawah
No | SOP Existing | Waktu |
---|---|---|
1 |
Crane menuju mesin | 5 menit |
2 | Unreleased molding lama | 5 menit |
3 | Menuju gudang molding dan meletakan molding | 5 menit |
4 | Mengambil molding baru dan menuju ke mesin | 5 menit |
5 | Memasang molding baru | 20 menit |
6 | Crane menuju gudang molding | 5 menit |
7 | Selesai | |
Total | 45 menit |
Proses changeover molding merupakan aktivitas tidak bernilai tambah, urutan SOP di atas dinilai oleh tim (berdasarkan pengamatan) sebagai proses yang tidak efektif, maka perlu dilakukan perbaikan SOP untuk meminimasi waktu yang dibutuhkan pada proses ini. Selain itu, tim juga melihat bahwa di lantai produksi belum diberlakukan aturan atau standar Kesehatan dan Keselamatan Kerja (K3) yang berlaku untuk operator serta aktivitasnya dan juga ditemukan permasalahan terkait penggunaan inventaris dan sumber daya yang tidak teratur.
Yamazumi chart berguna untuk membandingkan jumlah pekerjaan di setiap jenis proses dan jenis kendaraan dengan mengklarifikasi beban kerja dan dan rata-rata beban kerja. Bagian- bagian penting dalam grafik yamazumi adalah skala waktu yang diisi dengan menuliskan waktu dalam unit detik, takt time yang digambarkan dengan garis samping yang disesuaikan dengan nilai waktu takt time, proses yang dicatat dengan mengelompokkannya sesuai dengan model kendaraan yang akan dimaksud, yamazumi pekerjaan yang digambarkan dengan elemen pekerjaan setiap model kendaraan sesuai tipe kendaraan dengan waktu jalan yang diperhitungkan, dan kalkulasi waktu kerja.
Pada BDI factory komponen beban kerja operator dibedakan menjadi dua yaitu task dan proses/step. Task merupakan tugas yang harus dilakukan operator pada setiap proses/step. Sedangkan process/step merupakan urutan langkah-langkah dalam memproduksi barang. Berikut tabel beban kerja operator mesin injeksi BDI:
Nilai takt-time didapatkan dari
= total waktu kerja per hari (detik) / rata-rata demand harian
= (7 jam x 60 menit x 60 detik) / 960
= 26,25 detik
Berikut merupakan yamazumi chart pada operator mesin injeksi BDI kondisi saat ini:
Berdasarkan yamazumi chart yang telah dibuat diketahui bawah pada setiap proses kerja di BDI factory tidak merata. Pada proses Finishing dan QC 1 memiliki cycle time 2 kali lipat dari proses QC 2. Maka dari itu perlu dilakukan proses line balancing pada setiap bagian proses dengan cara menggabungkan, efisiensi, atau mengeliminasi proses pada setiap bagian (lini). Perbaikan sendiri sudah dilakukan pada tahap detailing point 4 sebagai alternatif perbaikan ke-1, Merumuskan solusi perbaikan proses yang mengalir antar lini serta di dalam lini produksi pada proyek Lean Manufacturing, Serta detailing point 5 sebagai alternatif perbaikan ke-2, Penerapan Built in Quality (Quality Assurance) pada proyek Lean manufacturing yang mana dampak dari perbaikan tersebut dapat diproyeksikan ke dalam Yamazumi Chart Improvement dibawah ini :
● Yamazumi Chart Improvement Alternatif 1 (Penerapan Meja Kara-Kuri)
Berikut ini merupakan Tabel beban kerja operator mesin injeksi BDI setelah penerapan solusi Alternatif 1 :
Berikut ini adalah gambar Yamazumi Chart Alternatif 1
● Yamazumi Chart Improvement Alternatif 2 (Penerapan Quality Assurance)
Berikut ini merupakan Tabel beban kerja operator mesin injeksi BDI setelah penerapan solusi Alternatif 2 :
Berikut ini adalah gambar Yamazumi Chart Alternatif 2
Takt Time adalah waktu yang tersedia untuk menghasilkan setiap unit produk untuk memenuhi permintaan pelanggan. Dengan kata lain, Takt Time adalah kecepatan yang harus dicapai oleh produksi untuk memenuhi kebutuhan pelanggan. Dengan demikian, Manajemen yang menangani produksi harus mengatur prosesnya sesuai dengan Takt Time yang ditentukan agar jumlah unit yang diproduksi sesuai dengan jumlah unit yang dibutuhkan oleh Pelanggan.
a. Proses produksi di area Mesin Injeksi
Permasalahan stabilitas proses kerja operator di area mesin injeksi yakni belum adanya kejelasan jobdesk antara proses finishing, inspeksi, rekapitulasi hasil produksi, dan packaging material ke plastik sehingga membuat keseimbangan beban kerja dan konsistensi kerja operator tidak stabil.
b. Proses changeover molding
Proses changeover molding merupakan aktivitas penting yang tidak bernilai tambah, proses ini sangat sukar sekali dieliminasi, di dalamnya juga terdiri dari beberapa sub urutan proses yang berulang, tidak efektif, tidak efisien, dan membahayakan pekerja. Sub urutan proses inilah yang sekiranya bisa dieliminasi atau dilakukan efektivitas serta perbaikan.
c. Kesehatan dan Keselamatan Kerja Operator
Aspek K3 di lantai produksi belum diterapkan, penggunaan alat pelindung diri untuk bekerja atau melakukan aktivitas yang berbahaya seperti melakukan peruncingan logam dengan gerinda dan aktivitas lain, belum tersedia dan diterapkan sehingga menimbulkan resiko kecelakaan kerja yang tinggi.
d. 5R (Ringkas, Rapi, Resik, Rawat, dan Rajin)
Di lantai produksi, penggunaan fasilitas, alat, dan barang belum dilakukan secara efisien, belum tertata dengan baik dan juga bersih. Hal ini mengganggu proses kerja yang mempengaruhi performansi kerja operator baik dari segi kenyamanan serta efektivitas kerja.
e. Penggunaan Inventaris
Penggunaan inventaris ini merupakan penjabaran lebih lanjut terkait elemen Rapi pada 5R. Penggunaan alat penunjang produksi seringkali sulit untuk dilacak dan tidak kembali dengan waktu dan tempat yang sesuai atau bahkan hilang karena belum adanya aturan atau tata cara penggunaan pada inventaris. Semenatara itu untuk penggunaan barang, seringkali digunakan secara tidak efektif dan efisien karena belum adanya aturan dan perencanaan pengadaan yang optimal yang diakibatkan tidak adanya data untuk mengevaluasi metode pengadaan.
a. Pembuatan SOP
Kemungkinan Kesulitan
Diperlukan penyesuaian dan waktu yang tidak sedikit untuk sosialisasi dan pelatihan
(jika diperlukan) dengan bagian-bagian terkait
b. Pembuatan TSK & TSKK
Kemungkinan Kesulitan, Pada proses pemetaan dan penggambaran kondisi kerja yang aktual diperlukan tingkat ketelitian serta kecermatan yang tinggi. Proses ini dilakukan secara bersamaan dengan proses menggambarkan masing-masing proses kerja sekaligus menggambarkan gabungan antara gerakan manusia dengan mesin di dalam satu cycle time sehingga proses yang cukup panjang tersebut bisa menjadi poin kesulitan yang akan dihadapi dalam proses penyusunan TSK & TSKK.
Dampak Positif, Standar TSK digunakan untuk melihat urutan kerja dan berapa lama waktu kerja tersebut berlangsung akan mudah dimengerti, dipergunakan juga untuk menemukan poin-poin yang diperlukan untuk melakukan kaizen pekerjaan. Sedangkan untuk standar TSKK digunakan untuk menggambarkan gerakan orang dengan lay out dalam satu siklus. Tabel standarisasi kerja ini dipakai juga sebagai alat untuk pengawasan kerja yang dapat langsung terlihat.
Dalam menciptakan proses kerja yang terstandarisasi diperlukan suatu upaya menstandarkan pekerjaan lewat dibentuknya Standar Operasional Prosedur (SOP) untuk masing-masing kegiatan. SOP ini nantinya kan menjadi acuan dasar untuk setiap pekerjaan sehingga dapat dengan mudah untuk mengevaluasi kinerja dari setiap proses yang ada. Pada sub bab ini akan dibuat rencana kerja untuk perbaikan efisiensi proses kerja operator pada industri inject molding.
Sesuai dengan kemampuan perusahaan, di dalam SOP area mesin injeksi memuat prosedur standar untuk kegiatan proses produksi, Quality Inspection, dan Abnormality Rule. Selain itu, yang kedua yaitu SOP Change Over Molding yang mana akan memuat prosedur standar untuk kegiatan pergantian mold pada mesin inject molding. Selanjutnya yang ketiga yaitu SOP Warehouse Finish Good yang mengatur prosedur standar untuk kegiatan input kanban dan pulling delivery. Keempat, SOP Warehouse Raw Material yang mengatur standar prosedur untuk kegiatan penggunaan raw material dan input material ke mesin. Kelima, SOP K3 yang mengatur standar prosedur untuk penggunaan APD (Alat Pelindung Diri) pada setiap operator yang disesuaikan dengan proses yang dijalani. Keenam, yaitu SOP Inventaris yang mengatur standar prosedur untuk kegiatan penggunaan alat dan penggunaan barang yang ada di workshop produksi.
a. SOP di area Mesin Injeksi
1. Proses produksi
Produksi didefinisikan sebagai kegiatan untuk menciptakan atau menambah nilai suatu barang. Dengan demikian, proses produksi adalah serangkaian tahapan yang harus
dilalui untuk dapat menghasilkan barang atau jasa. Berikut merupakan gambar Standar
Operasi Proses (SOP) proses produksi di area mesin injeksi BDI Factory:
2. Quality Inspection
Quality inspection bertujuan untuk melihat dan mengecek proses produksi yang berlangsung. Entah itu bahan baku atau raw materialnya yang harus dicek. Ataukah
mesin produksinya (work center), atau bahkan proses produksi dan bahkan dalam
beberapa kasus, bisa melibatkan kebersihan dari operator yang menjalankan proses manufakturing. Berikut merupakan gambar Standar Operasi Proses (SOP) Quality
Inspection BDI Factory:
3. Abnormality Rule
Abnormality atau Kondisi Abnormal adalah Bila proses kerja tidak mengikuti Standard yang sudah ditetapkan, karena adanya problem/penyimpangan. Berikut merupakan gambar rule penanganan abnormality di BDI Factory:
b. SOP Changeover Mold
Changeover berarti proses pergantian aktivitas produksi di suatu lini produksi dari satu produk ke produk lainnya. Artinya Change Over Mold adalah sebuah proses pergantian mold pada mesin injeksi, Berikut merupakan gambar Standar Operasi Proses (SOP) pergantian mold pada mesin injeksi di BDI Factory:
c. SOP Warehouse Finish Good
1. Input Kanban
Kanban adalah salah satu metode dalam manajemen proyek dengan cara membuat visualisasi menggunakan papan, kolom, dan kartu untuk mengelola tugas dan alur kerja secara lebih efektif. Berikut merupakan gambar Standar Operasi Proses (SOP) input kanban di BDI Factory:
2. Pulling Delivery
Berikut merupakan gambar Standar Operasi Proses (SOP) Pulling Delivery di BDI Factory
d. SOP Warehouse Raw Material
1. Penggunaan Raw Material
Raw material atau disebut juga sebagai bahan mentah atau bahan baku merupakan bahan dasar yang dibeli oleh industri manufaktur, kemudian barang yang sudah dibeli tersebut langsung disimpan di dalam gudang bahan baku dan kemudian akan diolah. Bahan dasar ini nantinya akan berubah menjadi barang jadi (finish good) yang siap untuk dijual. Berikut merupakan gambar Standar Operasi Proses (SOP) penggunaan Raw Material pada Warehouse Raw Material di BDI Factory
2. Input Material ke Mesin
Berikut merupakan gambar Standar Operasi Proses (SOP) input material ke mesin di BDI Factory:
e. SOP K3
Keselamatan dan Kesehatan Kerja (K3) adalah semua Ilmu dan Penerapannya untuk mencegah terjadinya kecelakaan kerja, penyakit akibat kerja (PAK), kebakaran, peledakan dan pencemaran lingkungan. Berikut merupakan gambar Standar Operasi Proses (SOP) penerapan Kesehatan dan Keselamatan Kerja (K3) di BDI Factory
f. SOP Inventaris
1. Penggunaan alat
Berikut merupakan gambar Standar Operasi Proses (SOP) penggunaan alat pada inventaris di BDI Factory :
2. Penggunaan barang
Berikut merupakan gambar Standar Operasi Proses (SOP) penggunaan barang pada inventaris di BDI Factory
7) TSK (Tabel Standar Kerja)
Tabel standarisasi kerja adalah instruksi kerja yang menggambarkan dengan jelas kondisi pekerjaan di tempat tersebut yang sekaligus menggambarkan masing-masing proses tersebut di dalam suatu tempat kerja. Berikut merupakan gambar Tabel Standar Kerja (TSK) di BDI Factory
8) TSKK (Tabel Standar Kerja Kombinasi)
Tabel standar kerja kombinasi adalah instruksi kerja yang menggambarkan gabungan antara gerakan manusia dengan mesin di dalam satu cycle time, yang menggambarkan seberapa area kerjanya, dan bagaimana urutan kerja tersebut dilakukan. Berikut merupakan gambar Tabel Standar Kerja Kombinasi (TSKK) di BDI Factory: