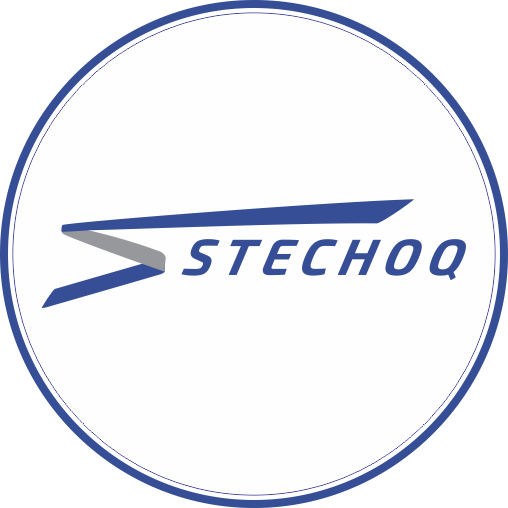
Pengumpulan data merupakan tahapan yang penting untuk memperoleh input bagi Value Stream Mapping (VSM), adapun data-data yang diperlukan adalah sebagai berikut:
Identifikasi data | Keterangan |
---|---|
Stakeholder terlibat | Meliputi supplier dan konsumen |
Proses kerja | Minimal menginformasikan 5W + 1H |
Langkah operasi yang terjadi pada material | Urutan operasi kerja dan alur material |
Cycle time | Waktu yang diperlukan untuk menyelesaikan satu siklus produksi |
Change over time | Waktu yang diperlukan untuk penggantian barang yang akan di produksi |
Mesin yang digunakan | Waktu set up, kapasitas, up and down time |
Jumlah pekerja, shift kerja, waktu kerja dan ukuran batch | - |
Berikut ini merupakan langkah-langkah pembuatan bagan aliran material dan informasi:
a. Identifikasi urutan proses
b. Identifikasi informasi apa saja yang digunakan dan dialirkan pada setiap proses. Berikut
merupakan informasi yang dibutuhkan :
Informasi yang dibutuhkan | Definisi |
---|---|
inventory type and size, |
Jenis Inventory di VSM disimbolkan dan dikategorikan secara umum dengan simbol segitiga, Namun penting untuk mengetahui aktivitas inventory apa saja yang ada (seperti kanban, FIFO, dll) dan juga berapa banyak jumlah material di inventory |
cycle time, |
Waktu yang dibutuhkan untuk menghasilkan satu produk atau informasi pada setiap proses. Di akhir semua proses, dijumlahkan semua cycle time |
change-over time, |
Waktu yang dibutuhkan untuk bertransisi dari proses sebelumnya |
machinery or process uptime and downtime, |
Uptime merupakan jumlah waktu produktif saat proses berjalan, sementara downtime adalah waktu yang tidak produktif (dikarenakan perbaikan atau gangguan proses) pada saat proses berjalan. Di VSM diberi keterangan sebagai contoh “Uptime = 90%” yang berarti ada 10% waktu downtime |
number of workers, |
Jumlah pekerja atau operator yang terlibat |
shifts worked, |
Jumlah shift pekerjaan di suatu proses |
available working hours and |
Waktu kerja di setiap proses selama satu hari |
1. Evaluasi Setiap Proses
Untuk melakukan penilaian terhadap setiap langkah terdapat syarat yang harus dipenuhi, yaitu:
a) Valuable, memberikan nilai tambah produk pada sudut pandang konsumen.
b) Capable, sejauh mana atau seberapa lama proses dapat memberikan high-quality pada produk.
c) Available, sejauh mana proses tersedia saat dibutuhkan.
d) Adequate, sejauh mana kapasitas yang tersedia untuk memenuhi permintaan.
e) Flexible, sejauh mana proses dapat berpindah ke orang lain.
2. Petakan Arus aliran Material dan informasi
Untuk mempermudah melakukan pemetaan arus aliran material dan informasi, terdapat tiga hal utama yang perlu diketahui lebih lanjut, yaitu:
Flow vs Stagnation | Arus vs Stagnasi. Yang ideal adalah agar produk tidak pernah berhenti bergerak. Hal ini dapat diukur dengan tingkat persediaan. |
---|---|
Push vs Pull | Dorong vs Tarik. Ini menunjukkan bagaimana informasi produksi ditangani. Dalam aliran nilai ideal, tidak ada informasi yang diperlukan kecuali sinyal di bagian atas aliran untuk membuat produk berikutnya. Namun pada kenyataannya, ada pemutusan antara bagian-bagian sungai. Hal ini diatasi dengan memiliki langkah-langkah yang dapat saling memberi isyarat tentang kebutuhan yang akan datang |
Level vs Erratic | Level vs Tidak menentu. Ini menunjukkan sejauh mana proses telah dihaluskan untuk efisiensi. Ini membahas konsep lean manufacturing dari mura (ketidaksetaraan), muri (pembebanan arus nilai yang berlebihan untuk mengikuti) dan muda (pemborosan.) Juga penting untuk memahami keseluruhan arus informasi dan komunikasi dalam arus nilai. Memproduksi produk atau layanan yang bernilai bagi pelanggan berarti kita perlu memahami titik sentuh komunikasi. Contohnya termasuk bagaimana pelanggan memesan produk, bagaimana pemasok dihubungi, dan bagaimana kami memastikan bahwa pelanggan mendapatkan apa yang mereka inginkan. |
Hitung inventory yang tersedia
Create Timeline > petakan setiap waktu proses dan waktu tunggu
Buat VSM keadaan sebenarnya
Mengkategorikan setiap proses ke dalam 3 kategori aktivitas: Aktivitas bernilai tambah, Aktivitas tidak bernilai tambah namun penting dan Aktivitas tidak bernilai tambah
Buat VSM perbaikan
Implementasi
Ketidaklancaran dalam mengalirkan material dan informasi merupakan akibat dari terganggunya suatu proses, baik proses itu sendiri atau proses transisi ke proses selanjutnya. Penyebab suatu proses terganggu dikarenakan adanya aktivitas yang membuat proses butuh waktu yang lama, penyebab-penyebab tersebut secara umum dikategorikan sebagai 7 waste atau 7 pemborosan. Berikut merupakan penjelasan 7 waste:
Berikut ini adalah cakupan input-output pada material dan informasi:
a. Material dan informasi apa saja yang ada pada aliran VSM dari atau ke stakeholder (pihak luar). Contohnya adalah sebagai berikut:
Mendapatkan (input) informasi pemesanan (order, weekly order, monthly order,
dll).b. Material dan informasi apa saja yang ada pada aliran VSM dari atau ke antar departemen (internal perusahaan). Contohnya adalah sebagai berikut:
Aliran spare part dari gudang ke departemen Cutting (Input material) untuk diolah
dan dialirkan selanjutnya ke departemen pewarnaan (output material).Sinyal Kanban Withdrawal untuk meminta bahan baku dari gudang (input
informasi) di tengah proses.Tujuan dari mengumpulkan data adalah pada saat penyusunan value stream mapping agar data yang terkumpul data yang lebih komprehensif dan tujuan dari memetakan data agar dapat memvisualisasi proses bisnis yang berjalan pada BDI Factory. Berikut merupakan langkah-langkah pembuatan value stream mapping:
Kebutuhan data yang diperlukan dalam penyusunan aliran Material/Produk dan Informasi diantaranya sebagai berikut :
A. Stakeholder terlibat : Meliputi supplier bahan baku, PT Stechoq Robotika Indonesia, Balai Diklat Industri Yogyakarta, dan Konsumen.
B. Proses kerja : Menginformasikan 5W + 1H diantaranya
What : Produksi yang dikerjakan di BDI Factory adalah T-Valve, Mangkok,
Sendok, Gelas dan Piring kecil.C. Langkah operasi yang terjadi pada material :
Data urutan operasi kerja mulai dari Marketing, PPIC, Purchasing, Produksi,
Distribusi.Alur material : Unloading, Warehouse Material, Proses produksi, Quality Control,
Warehouse Finish Goods, Shipping, dan Loading.D. Cycle time (CT) : Waktu yang diperlukan untuk menyelesaikan satu siklus produksi
F. Mesin yang digunakan
G. Jumlah Pekerja
Berikut ini adalah gambaran Value Stream Mapping kondisi Current yang ada di BDI Factory produksi T-Valve mesin Shibaura T130.
Berdasarkan gambar VSM diatas didapatkan waktu untuk memproduksi 1 kanban T- Valve dengan jumlah 200 pcs diperlukan Total Lead Time mencapai LT =1 Day 17 Minute 5 Seconds dan Total Cycle Time mencapai CT = 4 Hours 41 Minute 40 Second. Dengan rincian total waktu kegiatan Non Value Added NVA = 1 Day 17 Minute 5 Second sedangkan untuk total waktu kegiatan Value Added VA = 4 Hours 11 Minute 40 Second.
Alur proses produksi BDI Factory melalui tahapan yang dimulai dari order oleh customer dan diterima oleh tim marketing dalam bentuk informasi elektronik untuk selanjutnya diproses oleh PPIC, setelah itu dilakukan order material oleh tim purchasing kepada supplier bahan baku. Setelah proses unloading material, material akan disimpan kedalam warehouse bahan baku. Saat ada perintah produksi raw material akan dibawa dari warehouse menuju mesin inject untuk dilakukan proses input material, proses ini berlangsung bersamaan dengan proses pergantian molding inject (dandori) serta running awal mesin. Pada proses pra produksi tersebut memerlukan Total Lead Time mencapai LT = 5 Minute 35 Second dan Total Cycle Time mencapai CT = 4 Hours. Dengan rincian total waktu kegiatan Non Value Added NVA = 5 Minute 35 Second sedangkan untuk total waktu kegiatan Value Added VA = 4 Hours.
Setelah melalui proses pra produksi selanjutnya adalah proses injection molding dengan mesin Shibaura T130 diperoleh waktu Cycle Time 6 second/pcs, Change Overtime 0 detik, Uptime 100%, dan Available 8 jam, Sehingga waktu yang diperlukan untuk injection 200 pcs atau 1 kanban T-valve dengan mesin Shibaura adalah 20 menit. Setelah proses injection memasuki proses pengecekan kualitas pada QC Line dengan tugas utama untuk finishing produk, quality inspection, dan perhitungan kuantitas dengan total Cycle Time 5 detik/pcs sehingga waktu yang diperlukan untuk proses pengecekan kualitas 200 pcs T-valve pada stasiun QC Line mencapai 16 menit 40 detik.
Output dari proses pada QC Line akan dibawa ke stasiun QC Final untuk dilakukan pengecekan kualitas akhir, packaging, dan labeling produk sebelum dikirim. Setelah dari proses QC Line produk baru dikatakan sebagai Finish goods yang siap akan dikirim ke customer, namun sebelum dikirim finish goods tersebut akan disimpan ke dalam warehouse FG. Berdasarkan kondisi tersebut yang dimana kegiatan produksi masih terbilang belum optimal sehingga memungkinkan untuk dilakukan perbaikan. Hal yang dapat dilakukan diantaranya Pengadaan Tangga Ergonomis dan Save Setting Parameter Mesin, Penerapan Quality Assurance (QA), dan Penerapan Warehouse Management System (WMS).
Value atau nilai tambah pada suatu produk menjadi sangat penting bagi perusahan atau industri agar produk yang dihasilkan dapat bersaing dengan kompetitor. Memberikan nilai tambah pada produk dapat dilakukan dengan mendesain proses produksi yang lebih efektif dan efisien. Salah satu caranya adalah dengan meminimalkan atau menghilangkan waste atau pemborosan pada proses produksi. Apabila hal tersebut dapat dicapai maka perusahaan dapat memenuhi value yang diinginkan oleh konsumen dengan sumber daya yang minimal.
Salah satu alat atau tools yang dapat digunakan untuk menerapkan lean adalah Value Stream Mapping (VSM). VSM merupakan metode yang menggambarkan seluruh proses yang ada pada suatu perusahaan (Rother & Shook, 1998). Gambaran seluruh proses tersebut digambarkan dengan simbol-simbol tertentu pada selembar kertas. Proses produksi yang dimaksud adalah dari bahan baku hingga produk berada pada tangan konsumen. Tujuan dari VSM adalah mengidentifikasi proses produksi agar material dan informasi dapat berjalan tanpa adanya gangguan, meningkatkan produktivitas dan daya saing, serta membantu dalam mengimplementasikan sistem (Womack dkk, 1991). Oleh karena itu VSM membantu dalam menemukan waste yang ada dalam proses produksi.
Dalam menyiapkan proses Value Stream Mapping (VSM), terdapat beberapa konsep yang perlu diidentifikasi terkait Lean Manufacturing. Lean manufacturing adalah metode untuk dapat mengidentifikasi dan menghilangkan waste atau aktivitas yang tidak memiliki nilai tambah. Tujuan dari diterapkan lean manufacturing adalah untuk meningkatkan kinerja dari industri manufaktur. Konsep yang perlu diidentifikasi lebih lanjut adalah sebagai berikut:
Program 5S (Seiri, Seiton, Seiso, Seiketsu dan Shitsuke) merupakan dasar bagi mentalitas karyawan untuk melakukan perbaikan (improvement) dan juga untuk mewujudkan kesadaran mutu (quality awareness) (Heizer and Render,2009). 5S adalah sebuah pendekatan dalam mengatur lingkungan kerja, yang pada intinya berusaha mengeliminasi waste sehingga tercipta lingkungan kerja yang efektif, efisien dan produktif (Osada, 2004). Sedangkan Hirano (1996) mendefinisikan 5S sebuah alat untuk membantu mengungkapkan masalah dan bila digunakan secara canggih, dapat menjadi bagian dari proses pengendalian visual dari sebuah sistem lean yang direncanakan dengan baik.
5S sendiri merupakan singkatan dari Seiri (Sort), Seiton (Straighten), Seiso (Shine), Seiketsu (Standardize), dan Shitsuke (Sustain). Dalam Bahasa Indonesia diterjemahkan sebagai 5R yang berarti Ringkas, Rapi, Resik, Rawat, Rajin. Konsep 5R / 5S yaitu merupakan proses perubahan sikap dengan cara menerapkan aspek penataan, kebersihan dan kedisiplinan di tempat kerja. Dengan menerapkan prinsip “A place for everything and everything in its place” maka setiap anggota organisasi dibiasakan bekerja dalam lingkungan kerja dengan standar tempat yang jelas. Pada konsep 5R / 5S juga bagian dari konsep kaizen yang memiliki arti penyempurnaan secara berkesinambungan pada kehidupan pribadi, kehidupan di keluarga, lingkungan sosial ataupun juga tempat kerja. Pengertian falsafah 5S yaitu:
Seiri/Sortir/Ringkas
Seiri adalah dengan menyisihkan barang yang dianggap tidak diperlukan dan barang
yang dianggap tidak diperlukan di tempat kerja dibuang.
Seiton/Susun/Rapi
Seiton (susun) adalah dengan menata peralatan kerja yang digunakan dengan rapi dan
menghilangkan kegiatan mencari agar alat-alat tersebut bisa dengan mudah ditemukan
secara cepat.
Seiso/Sapu/Resik
Seiso adalah dengan memelihara kebersihan pada tempat kerja. Setelah menjadi rapi,
langkah berikutnya adalah membersihkan tempat kerja, ruangan kerja, peralatan dan
lingkungan kerja.
Seiketsu/Standardisasi/Rawat
Seiketsu adalah dengan mempertahankan seiri, seiton, dan seiso agar proses tersebut
bisa berlangsung secara terus-menerus.
Setsuke/Swa disiplin/Rajin
Setsuke adalah suatu bentuk kedisiplinan yang mana hal tersebut menjadi kebiasaan,
sehingga para pekerja menjadi biasa mematuhi peraturan dan dilaksanakan penyuluhan
kepada para pekerja agar dapat bekerja dengan profesional (Restupuri dan Wahyudin,
2019).
Just In Time atau JIT merupakan filosofi pemanufakturan yang memiliki implikasi penting dalam manajemen biaya. Ide dasar JIT sangat sederhana, yaitu produksi hanya apabila ada permintaan (pull system) atau dengan kata lain hanya memproduksi sesuatu yang diminta dan hanya sebesar kuantitas yang diminta. Filosofi JIT digunakan pertama kali oleh Toyota dan kemudian diadopsi oleh banyak perusahaan manufaktur di jepang. Semua sumber daya yang diperlukan oleh proses produksi disiapkan tepat pada waktu saat dibutuhkan saja. Prinsip dasar dalam JIT adalah pull system, continuous flow, dan takt time. Continuous flow adalah aliran produksi dilakukan berdasarkan aliran material. dan takt time adalah waktu yang tersedia untuk menghasilkan setiap unit produk untuk memenuhi permintaan pelanggan. Persoalan yang sering muncul : isu persediaan bahan baku, aliran produksi, jumlah produksi
Jidoka (autonomation) adalah pendeteksian dan pengendalian part cacat secara otomatis. Prinsip dari jidoka adalah otomasi peralatan yang bekerja secara harmonis dengan operatornya atau dapat disebut dengan machine-human automation. Dengan adanya prinsip Jidoka, sistem Toyota mengajak seluruh karyawan untuk senantiasa memiliki kepekaan dan rasa tanggung jawab terhadap kualitas part. Jidoka bertujuan untuk menjamin kualitas produksi untuk mencapai hasil 100% baik, menghemat atau menyederhanakan manpower, dan mencegah terjadinya downtime akibat adanya kelainan pada proses operasional produksi. Persoalan yang sering muncul: biaya tinggi untuk otomasi > perlu investasi lebih besar.
Standarisasi Kerja adalah peraturan pada saat membuat barang di tempat kerja, yaitu cara melakukan produksi yang paling efektif dengan urutan tanpa muda, mengumpulkan pekerjaan, dan memfokuskan gerakan manusia. Persoalan yang sering muncul: Isu Dehumanisasi pekerja > dimana pekerja dianggap sebagai mesin
Dalam melakukan kegiatan perbaikan terus-menerus (Continuous Improvement) perlu dilakukan langkah-langkah untuk mengidentifikasi masalah beserta akar penyebabnya atau dikenal dengan istilah define pada sistem manufaktur eksisting BDI Factory Yogyakarta. Adapun hal-hal yang harus diperhatikan adalah sebagai berikut:
Salah satu hal yang perlu diperhatikan dalam tahap define adalah terkait dengan penyusunan ketidaklancaran aliran material dan informasi berdasarkan VSM (Value Stream Mapping). Kegiatan ini akan membantu dalam memetakan terkait penanganan material (material handling) pada setiap proses yang ada di workshop BDI Factory Yogyakarta. Adapun tahapan yang harus dilakukan adalah sebagai berikut:
No | Proses | Value-Added Activity | Necessary Non-Value-added Activity | Non-Value-added Activity |
---|---|---|---|---|
1 | Pra Produksi |
|
|
|
2 | Mesin Injeksi |
|
|
|
3 | Quality Line |
|
|
|
4 | QC Final |
|
|
|
5 | Pemuatan ke Gudang Barang Jadi |
|
No | Proses | Defect | Transportation | Waiting Time | Over-Production | Over-Processing | Excess Motion | Inventory |
---|---|---|---|---|---|---|---|---|
1 | Pra Produksi | Trial and Error |
|
|
||||
2 | Proses Injeksi | Terdapat banyak defect produk yang diakibatkan setting parameter injeksi yang kurang baik |
|
|||||
3 | Quality Line |
|
|
|||||
4 | QC Final |
|
|
|||||
5 | Pemuatan ke Gudang |
|